Graphite in grey cast iron is flaky, and its distribution shape can be divided into a, B, C, D, e and F. Different distribution shapes have different effects on the mechanical properties, service properties, physical properties and technological properties of gray cast iron.
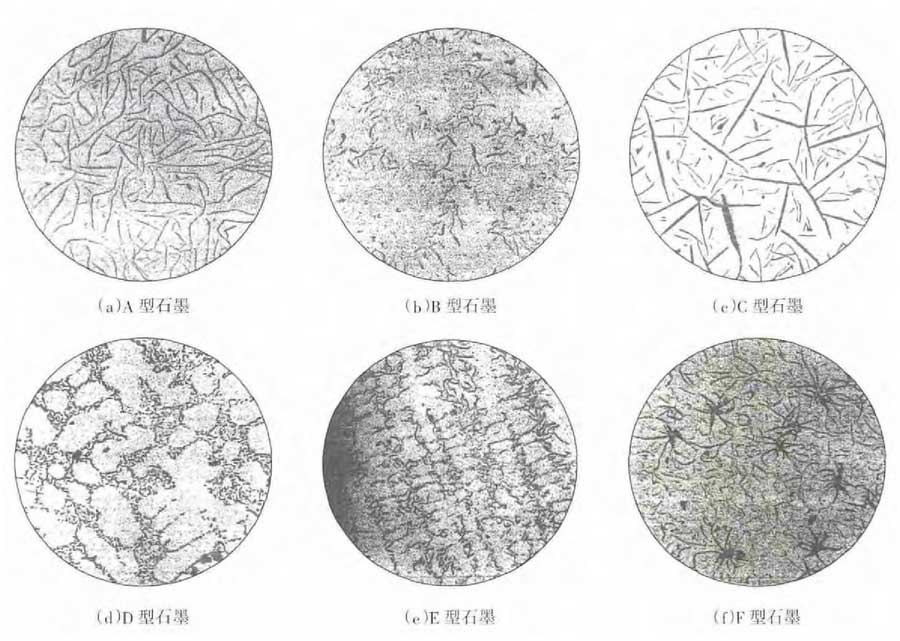
The graphite distribution shape of gray cast iron is described in the previous relevant standards [1-2]. In 2009, the new standard GB / T 7216-2009 metallographic examination of grey cast iron was issued and implemented. The standard mainly adopts the type I flake graphite part of ISO 945-1:2008 “microstructure of cast iron part I: classification and visual inspection of graphite”. The old standard, especially the type and connotation of graphite distribution shape, has been greatly modified.
(1) both C-type and F-type graphite are primary graphite, and graphite is precipitated from molten iron under hypereutectic composition. The characteristics of C-type graphite are long, thick and straight. F-type graphite only appears in castings as thin as single casting piston rings. The walls of single casting piston rings are very thin. CE needs to be improved. Hypereutectic composition is used. Under the condition of thin-wall rapid cooling, F-type graphite is produced. This primary graphite bifurcates in the shape of star (or spider spider). The claw of spider-like graphite is straight, and the claw end is slightly bent.
(2) graphite of a, B, D and e exist in hypoeutectic cast iron. They are eutectic graphite produced in the process of eutectic. The pearlite content in the structure of high-strength gray cast iron with HT250 or above should be more than 98%, and the graphite should be distributed uniformly without direction, i.e. type a graphite. In the case of A-type graphite as the main body, some B-type graphite will appear in the local field of vision. This is due to the condition of increasing supercooling degree in some micro areas of eutectic iron with low macro supercooling degree, resulting in supercooled graphite. Once the supercooled graphite appears, it will release latent heat of crystallization, which will reduce the degree of supercooling. Therefore, the graphite with the same heat dissipation direction is crystallized around the fine supercooled graphite at a slightly higher temperature. In this way, the graphite produced successively gathers into chrysanthemum like distribution, which is called B-type graphite. It is not surprising that the appearance of B-type graphite does not affect the tensile strength of cast iron. D-type and E-type graphite are produced in the later stage of eutectic. D-type graphite is a kind of supercooled graphite formed under a large degree of supercooling. The graphite flakes are small and curly, and there is no directional distribution between austenite dendrites. Under the condition of low CE and high cooling rate, primary austenite dendrites have been developed during eutectic solidification. Eutectic graphite can only precipitate between the secondary branches of dendrites to form directional distribution and E-type graphite. E-type graphite is not supercooled graphite, not short.
The classification of graphite distribution in grey cast iron is crucial because it significantly influences the material’s mechanical properties and overall performance. Grey cast iron, known for its excellent castability and machinability, derives its characteristics mainly from the form and distribution of graphite within the iron matrix. Here’s how graphite distribution is typically classified:
1. ASTM A247 Graphite Classification
- Type I: Flakes are long and thin, often referred to as ‘kish’ graphite. This type is typical in castings cooled slowly or in thicker sections of cast iron.
- Type II: Shorter and thicker flakes. Found in medium thickness castings and provides a good balance between strength and ductility.
- Type III: Worm-like or vermicular graphite. This type offers better tensile strength and ductility compared to Type I and II.
- Type IV: Randomly oriented short flakes and a mix of type I and II characteristics. Common in uniformly cooled castings.
- Type V: Interconnected or coalesced flakes forming large clusters. This type is less common and generally indicates poor control of the casting process.
2. Size of Graphite Flakes
- Size 1 to 8: The size of the graphite flakes is also graded, with size 1 being the largest and size 8 the smallest. The larger the flakes, generally, the more brittle the cast iron.
3. Distribution of Graphite
- Distribution A to E: The distribution pattern of graphite flakes is graded from A to E, with A being a uniform distribution and E being a clustered distribution. Uniform distributions (A) typically offer better mechanical properties.
Influence on Properties
- Strength and Brittleness: Larger, longer graphite flakes (Type I) tend to create weak points, leading to increased brittleness. Smaller, more uniformly distributed flakes (Type II, IV) improve strength.
- Impact and Fatigue Resistance: Vermicular or nodular graphite forms (Type III) greatly improve the impact and fatigue resistance of the cast iron.
- Thermal Conductivity and Damping: The graphite structure also impacts thermal conductivity and vibration damping, crucial for applications like engine blocks and machine beds.
Applications
- Different types of grey cast iron are chosen based on the required properties for specific applications. For instance, Type I may be used in applications where strength is not a primary concern but machinability is, whereas Type III might be selected for parts requiring higher strength and ductility.
Modern Developments
- Metallurgical Control: Advances in metallurgy allow for more precise control over graphite formation, leading to the development of specialized grey cast irons for specific applications.
- Alternative Graphite Forms: Research into different graphite shapes, like compacted graphite iron, provides materials with a mix of beneficial properties for more demanding applications.
Understanding the classification and impact of graphite distribution in grey cast iron is essential for selecting the right type of iron for specific applications and for predicting the behavior of the material under different working conditions.