This article comprehensively analyzes low-pressure casting technology. It elaborates on its basic principles, process parameters, technological characteristics, common defects and countermeasures, and future development trends. Through in-depth research and analysis, it provides a theoretical basis and practical guidance for the application and development of low-pressure casting technology.
1. Introduction
Low-pressure casting has a long history and has played an important role in the field of non-ferrous metal casting. With the development of modern industry, the demand for high-quality, precision castings is increasing, and low-pressure casting technology has attracted more and more attention due to its unique advantages.
2. Basic Principles of Low-Pressure Casting
Low-pressure casting is a casting process in which the molten metal is filled into the mold cavity under a certain pressure. The pressure used is relatively low, usually in the range of 0.02 MPa – 0.06 MPa. The basic process is as follows: In a sealed crucible or sealed tank, dry compressed air or inert gas is introduced. Under the action of gas pressure, the molten metal rises steadily along the riser tube and enters the cavity through the ingate. The gas pressure on the liquid surface in the crucible or sealed tank is maintained until the casting is completely solidified. Then, the gas pressure on the molten metal surface is released, and the unfrozen molten metal in the riser tube flows back into the crucible. Finally, the casting is ejected.
3. Process Parameters of Low-Pressure Casting
3.1 Liquid Rising Pressure
The pressure required to raise the molten metal surface to the vicinity of the gate is called the liquid rising pressure. It reflects the rising speed of the molten metal in the riser tube. The rising speed should be as slow as possible to facilitate the discharge of gas in the cavity and prevent the molten metal from splashing when entering the gate.
Parameter | Value Range | Effect |
---|---|---|
Liquid Rising Pressure | Depends on specific casting requirements | Controls the rising speed of molten metal in riser tube |
3.2 Filling Pressure
The gas pressure required for the molten metal to rise to the top of the mold during the filling process is the filling pressure.
3.3 Filling Speed
The rising speed of the molten metal surface during the filling process is the filling speed. To prevent cold shut and misrun defects, the filling speed should be higher than the minimum value, but not too fast to avoid the generation of oxidation inclusions caused by turbulent molten metal entraining gas.
Parameter | Value Range | Effect |
---|---|---|
Filling Speed | Appropriate value to avoid cold shut and misrun | Affects the quality of casting surface and internal structure |
3.4 Crystallization Pressure
After the molten metal fills the cavity, the pressure is further increased to make the crystallization and solidification of the casting proceed under a certain pressure. The larger the crystallization pressure, the better the feeding effect of the casting, and the denser the obtained casting structure and the better the mechanical properties. However, increasing the pressure through crystallization to improve the casting quality cannot be adopted in all cases. The usual value range of crystallization pressure is 0.1 MPa – 0.25 MPa.
Parameter | Value Range | Effect |
---|---|---|
Crystallization Pressure | 0.1 MPa – 0.25 MPa | Affects the density and mechanical properties of casting |
3.5 Holding Time
After the molten metal pressure is increased to the crystallization pressure, it will be maintained at the crystallization pressure for a period of time until the casting is completely solidified. The time required for pressure holding and solidification is called the holding time. If the holding time is insufficient, the casting will be “emptied” and scrapped; if the holding time is too long, the gate residue will be too long, which will not only reduce the process yield but also cause the molten metal in the gate and riser tube to “freeze”, making it difficult to remove the casting. Therefore, an appropriate holding time must be selected in production.
Parameter | Value Range | Effect |
---|---|---|
Holding Time | Depends on casting size and material | Ensures complete solidification of casting |
3.6 Mold Temperature
Low-pressure casting can use various molds. For non-metallic molds, the working temperature is generally room temperature. For metal molds, there are certain requirements. For example, when low-pressure casting aluminum alloys, the working temperature of metal molds is generally controlled at 200 °C – 250 °C, and when casting thin-walled and complex parts, it can even be as high as 300 °C – 350 °C.
Parameter | Value Range | Effect |
---|---|---|
Mold Temperature (Metal Mold for Aluminum Alloy) | 200 °C – 350 °C | Affects the solidification process and quality of casting |
3.7 Pouring Temperature
In practice, it has been proved that under the premise of ensuring the formation of the casting, the lower the pouring temperature, the better. The pouring temperature of low-pressure casting is generally 10 °C – 20 °C lower than that of gravity casting.
Parameter | Value Range | Effect |
---|---|---|
Pouring Temperature | Lower than gravity casting by 10 °C – 20 °C | Affects the fluidity and quality of molten metal |
4. Technological Characteristics of Low-Pressure Casting
4.1 Advantages
4.1.1 High Purity of Molten Metal
Since the slag usually floats on the surface of the molten metal, and the low-pressure casting process fills and pours the molten metal at the bottom of the crucible through the riser tube, the possibility of slag entering the cavity can be effectively avoided, and the purity of the molten metal is high, resulting in fewer inclusions in the casting.
4.1.2 Stable Filling Process
The low-pressure casting process adopts a bottom gating process and the pressure is balanced, so the molten metal filling is relatively stable, which can effectively reduce or avoid turbulence and splashing of the molten metal during the filling process, and reduce the possibility of defects such as double oxide films and oxide inclusions in the casting.
4.1.3 Good Formability
The molten metal is filled under pressure, which can improve the fluidity of the molten metal to a certain extent, and is beneficial to the formation of castings with good surface finish and clear contours. It is especially advantageous for the forming of complex thin-walled castings.
4.1.4 Good Feeding Effect
The casting solidifies under a certain pressure and can achieve top-down sequential solidification. The feeding effect is good, the casting structure is relatively dense, and there are fewer shrinkage porosity and shrinkage cavity defects.
4.1.5 High Metal Yield
Low-pressure casting generally does not require risers, and the unfrozen molten metal in the riser tube can flow back to the crucible for reuse. Therefore, the metal yield is high, generally reaching more than 90%.
4.2 Disadvantages
4.2.1 High Equipment Cost
The equipment cost of low-pressure casting is high, and the initial investment is large. The production efficiency is relatively low, and it is generally used for casting non-ferrous alloys.
4.2.2 Erosion Problem
When producing aluminum alloy castings, the crucible and riser tube are in long-term contact with the molten metal, which are easily eroded and scrapped, and also cause the iron content in the molten metal to increase, resulting in the deterioration of the casting performance.
5. Common Defects and Countermeasures in Low-Pressure Casting
5.1 Gas Porosity
5.1.1 Morphological Characteristics
The morphology of gas porosity is mostly circular or elliptical, with a smooth inner wall and often a slight oxidized color.
5.1.2 Causes
- The filling speed of the molten metal is too fast, the liquid flow is turbulent and entrains gas, and the gas cannot be discharged smoothly and timely, resulting in the generation of gas porosity defects.
- After the molten metal is filled, the sand mold and sand core are heated for a long time and generate gas, causing the gas to invade the unfrozen molten metal and resulting in the generation of gas porosity defects.
- The exhaust is not smooth, and there are air pockets in the cavity, resulting in the generation of gas porosity defects.
5.1.3 Prevention Measures
- Select an appropriate filling speed. Under the premise of ensuring no cold shut and misrun, try to ensure the stability of the molten metal filling and avoid the generation of gas entrainment.
- Optimize the exhaust conditions of the sand mold and sand core to prevent the gas generated by the sand mold and sand core from entering the molten metal. In addition, under the premise of ensuring the strength of the sand mold and sand core, reduce the resin content of the sand mold and sand core to reduce the gas generation amount.
- Avoid blocking the exhaust holes, exhaust plugs and other exhaust structures.
5.2 Shrinkage Porosity and Shrinkage Cavity
5.2.1 Morphological Characteristics
The morphological characteristics of shrinkage porosity and shrinkage cavity are mostly irregular holes, and the inner walls of the holes are relatively rough, with many dendrite protrusions, mostly occurring at the hot spots or the last solidified parts.
5.2.2 Causes
After the molten metal is filled, during the crystallization and solidification process, a top-down temperature gradient cannot be formed, and sequential solidification cannot be achieved. Therefore, the hot spots at the last solidified part cannot be well fed, resulting in the generation of shrinkage cavity defects.
5.2.3 Prevention Measures
- Strengthen the heat dissipation ability of the hot spots (such as arranging chills).
- Reduce the pouring temperature as much as possible without causing cold shut.
- Increase the holding pressure during crystallization and solidification to improve the fluidity of the molten metal and enhance the feeding ability of the shrinkage cavity parts.
5.3 Cold Shut
5.3.1 Morphological Characteristics
The morphological characteristic of cold shut is the existence of cold shut lines, that is, the front ends of the two counter-flowing molten metals cannot be well fused.
5.3.2 Causes
- The pouring temperature is too low or the cooling capacity of the mold is strong. At the confluence of the molten metal, it is easy to cause cold shut defects.
- The filling pressure is insufficient, and the fluidity of the molten metal is poor, which also easily leads to cold shut defects.
5.3.3 Prevention Measures
- Appropriately increase the pouring temperature of the molten metal.
- For the cold shut lines caused by the too fast cooling speed of the cold iron bars, the cold iron bars can be moderately heated.
- Appropriately increase the filling pressure of the molten metal to improve the fluidity of the molten metal.
5.4 Inclusions
5.4.1 Morphological Characteristics
The morphology of inclusions is irregular, and the color at the defect is significantly different from that of the casting body.
5.4.2 Causes
- For the formation of non-metallic inclusions, most of them come from the foreign matter that falls into the cavity during the mold cavity processing and is not cleaned up, and then enters the molten metal during the filling process to form inclusion defects.
- Oxide inclusions are mostly caused by the fast filling speed of the molten metal, the turbulent and splashing of the liquid surface, and the formation of double oxide films.
5.4.3 Prevention Measures
- During the mold cavity processing, clean the processing cavity thoroughly.
- Adjust the filling pressure to avoid the turbulent and splashing of the molten metal caused by too fast filling speed or add a filter screen at the riser opening to play a role in filtering and stabilizing the molten metal.
6. Development Trends of Low-Pressure Casting Technology
6.1 Numerical Simulation Technology
With the development of computer technology, numerical simulation technology has been widely used in low-pressure casting. By developing accurate numerical models that match the actual filling flow and solidification crystallization sequence of the molten metal, the casting process can be optimized in advance, reducing the trial and error costs in the production process.
6.2 In-situ Detection Technology
Improving the in-situ detection ability of casting performance is also an important development trend. For example, using ultrasonic equipment to detect the residual stress of the casting or using thermal analysis technology to predict the mechanical properties of key parts of the casting can avoid destructive testing of the casting and timely reflect the accurate casting situation, realizing the precise control of the casting process and casting performance.
6.3 New Materials and Processes
The research and development of new materials and processes suitable for low-pressure casting will continue. For example, the development of high-performance aluminum alloys and the improvement of the low-pressure casting process for special alloys will expand the application range of low-pressure casting technology.
7. Conclusion
Low-pressure casting technology has unique advantages in the field of non-ferrous metal casting, but it also has some disadvantages. By continuously optimizing process parameters, improving process control, and strengthening defect prevention and detection, the quality and production efficiency of low-pressure casting can be further improved. At the same time, with the development of related technologies, low-pressure casting technology will have broader application prospects in the future.
In the process of writing this article, due to the lack of specific requirements for generating pictures, it is recommended to use relevant software to draw pictures according to the content of the article, such as process flowcharts, defect schematic diagrams, etc., to enhance the visual effect of the article.
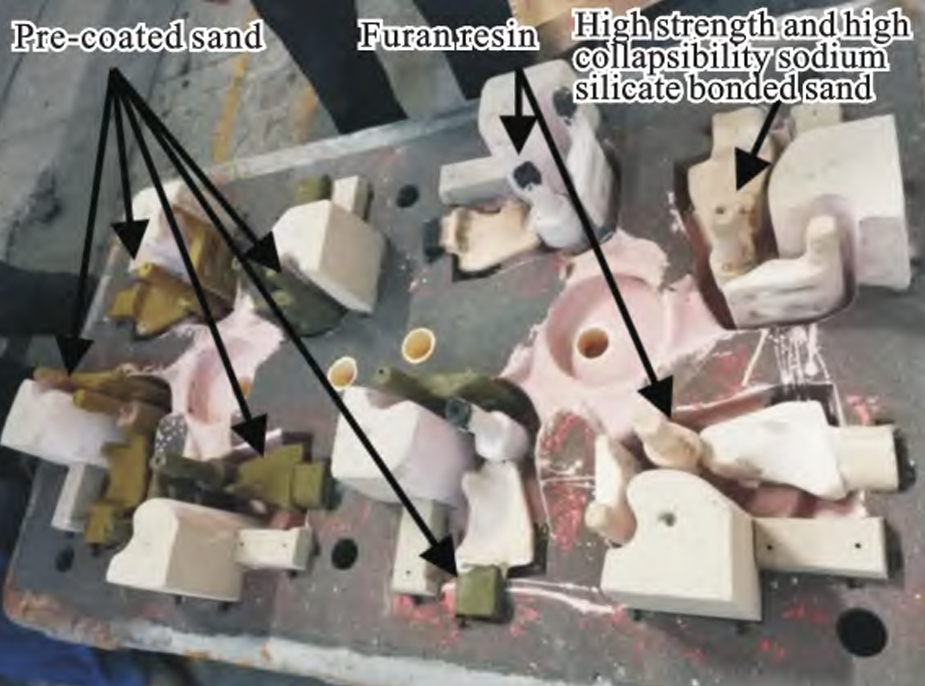