Abstract
This study investigates the influence of rare earth Ce on the microstructure and properties of semi-solid squeeze casting AlSi10Cu3Fe alloy through a comprehensive experimental approach. The effects of varying Ce concentrations on the alloy’s microstructure, mechanical properties, electrical conductivity, and fracture morphology are analyzed using various characterization techniques. The results reveal that the addition of Ce significantly refines the alloy’s microstructure and enhances its mechanical and electrical properties, with an optimal Ce content identified.
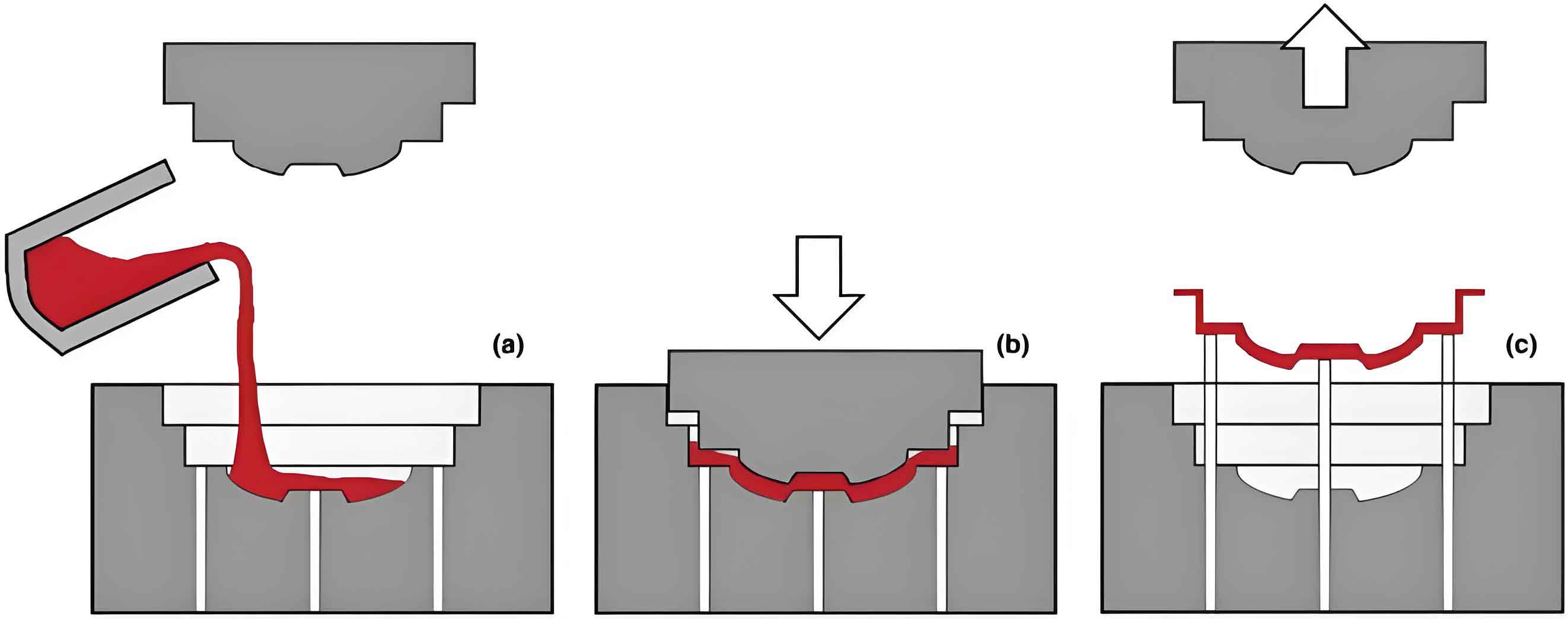
Introduction
Aluminum-silicon (Al-Si) alloys are widely used in various industries due to their excellent castability, machinability, and good mechanical properties. However, the pursuit of even higher performance alloys has led to the exploration of alloying elements such as rare earths. Rare earth elements, particularly cerium (Ce), have been shown to effectively refine microstructures and improve mechanical properties in aluminum alloys. In this study, the effects of Ce addition on the semi-solid squeeze casting AlSi10Cu3Fe alloy are systematically investigated.
Materials and Methods
Materials
The base alloy used in this study was AlSi10Cu3Fe, which was prepared by melting pure aluminum, silicon, copper, and iron in a well-controlled furnace. Rare earth Ce was added in the form of an Al-10Ce master alloy to ensure uniform distribution.
Squeeze Casting Process
The alloy was melted at 750°C and held at this temperature for 10 minutes to ensure complete melting. After degassing with C2Cl6, different amounts of Ce (0%, 0.25%, 0.5%, and 0.75% by weight) were added, and the melt was stirred thoroughly to ensure homogeneity. The melt was then cooled to 605°C and held for an additional 10 minutes before being poured into a preheated (250°C) mold using a semi-solid squeeze casting machine. The casting process was conducted at a pouring temperature of 600°C, a pressure of 150 MPa, and a dwell time of 15 seconds.
Characterization Techniques
- Microstructure Analysis: Optical microscopy (OM), scanning electron microscopy (SEM), and energy-dispersive X-ray spectroscopy (EDS) were used to analyze the microstructure and phase composition.
- Mechanical Testing: Tensile tests were performed using an electronic universal testing machine at room temperature to determine the ultimate tensile strength, yield strength, and elongation.
- Hardness Testing: Vickers microhardness tests were conducted to evaluate the hardness of the alloys.
- Electrical Conductivity Measurements: The electrical conductivity of the alloys was measured using a digital eddy current conductivity meter.
Results and Discussion
Microstructure Analysis
Base Alloy (0% Ce)
The microstructure of the base alloy (0% Ce) consisted primarily of coarse dendritic α-Al grains and eutectic Si phases. The α-Al grains exhibited a non-uniform and disorganized distribution, with eutectic Si phases clustering at grain boundaries.
Alloys with Ce Addition
The addition of Ce led to significant microstructural refinements. At 0.25% Ce (Figure 1b), the α-Al grains began to transition from dendritic to equiaxed shapes, with some rounded grains observed. As the Ce content increased to 0.5% (Figure 1c), the microstructure was uniformly refined, with mostly equiaxed and spherical α-Al grains. The eutectic Si phases were also more evenly distributed. However, at 0.75% Ce (Figure 1d), the microstructure coarsened slightly, with some elongated α-Al grains reappearing.
Grain Size and Shape Factor
The average grain size and shape factor of the α-Al grains were quantified, as shown in Table 1. The addition of 0.5% Ce resulted in the finest microstructure, with an average grain size of 48 µm and a shape factor of 0.75.
Ce Content (wt.%) | Average Grain Size (µm) | Shape Factor |
---|---|---|
0 | 99 | 0.49 |
0.25 | 78 | 0.61 |
0.5 | 48 | 0.75 |
0.75 | 67 | 0.62 |
Mechanical Properties
Tensile Properties
The addition of Ce significantly improved the tensile properties of the alloy. The ultimate tensile strength and elongation at break both peaked at 0.5% Ce, with values of 231.98 MPa and 7.8%, respectively.
Hardness
Similar trends were observed in the Vickers microhardness measurements . The hardness increased with Ce addition, peaking at 0.5% Ce (HV100.15), before decreasing at higher Ce contents.
Electrical Conductivity
The electrical conductivity of the alloys, measured in percent International Annealed Copper Standard (IACS), increased with Ce addition up to 0.5% . The highest conductivity (43.27% IACS) was achieved at this optimal Ce content, which was attributed to the refined microstructure and reduced porosity.
Fracture Morphology
The fracture surfaces of the alloys were analyzed using SEM to gain insights into their failure mechanisms. The base alloy exhibited a brittle fracture mode with distinct cleavage facets (Figure 5a). With the addition of Ce, the fracture surfaces transitioned to a more ductile mode, with the presence of dimples at 0.5% Ce (Figure 5c). However, excessive Ce addition (0.75%) led to a return to a more brittle fracture mode .
Discussion
Microstructure Refinement
The microstructural refinements observed with Ce addition can be attributed to several mechanisms. Firstly, the low solubility of Ce in Al leads to its segregation at the solid-liquid interface during solidification, promoting heterogeneous nucleation and thus refining the grain structure. Secondly, the formation of rare earth intermetallics can act as potent nucleation sites, further contributing to grain refinement.
Mechanical Property Enhancement
The improvement in mechanical properties can be explained by the Hall-Petch relationship, which states that the yield strength of a material increases with decreasing grain size. The refined microstructure observed with optimal Ce addition results in higher yield and ultimate tensile strengths. The increased elongation can be attributed to the more uniform and ductile grain structure.
Electrical Conductivity
The enhanced electrical conductivity at optimal Ce contents can be linked to the refined microstructure and reduced porosity. Porosity acts as scattering centers for electrons, reducing conductivity. Therefore, the reduction in porosity with Ce addition contributes to the improved electrical properties.
Fracture Morphology Analysis
The transition from brittle to ductile fracture modes with Ce addition suggests an improvement in the alloy’s plastic deformation capabilities. The dimpled fracture surfaces observed at optimal Ce contents further confirm the ductility enhancement.
Conclusion
This study comprehensively investigates the effects of rare earth Ce on the microstructure, mechanical properties, electrical conductivity, and fracture morphology of semi-solid squeeze casting AlSi10Cu3Fe alloy. The addition of Ce significantly refines the alloy’s microstructure, leading to improved mechanical properties and electrical conductivity. An optimal Ce content of 0.5% by weight is identified, which results in the finest microstructure, highest mechanical strength, and best electrical conductivity. These findings provide valuable insights into the potential of rare earth alloying for enhancing the performance of aluminum alloys in semi-solid squeeze casting applications.