The vertical semi-solid squeeze casting machine generally adopts the structure system of vertical clamping and clamping, bottom transverse feeding, bottom injection casting and vertical clamping cylinder secondary cavity extrusion molding, as shown in Figure 1.
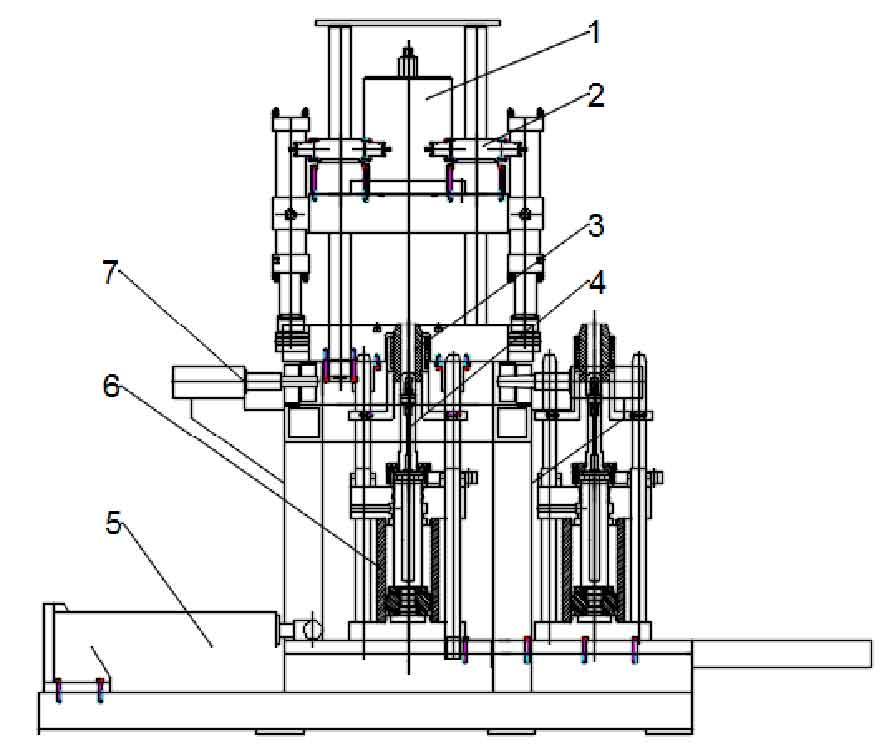
It mainly includes locking mechanism, injection part, hydraulic system and electrical control system. The main technical parameters are closing force 3000kN, injection force (maximum) 940kn, and the inner spacing of the table rod 620 × 620mm.
The operation of the squeeze casting machine is divided into three steps
(1) Operation preparation: ① before starting the machine, it is necessary to comprehensively check whether the mold, mechanical parts, motor and other devices are abnormal, and whether the lubricating oil connected to the lubricating pump and the hydraulic oil connected to the hydraulic pump are sufficient. ② Turn on the cooling water source connected to the oil cooler (such as the main switch of water supply, the switch of cooling tower, etc.) and adjust the water quantity to a proper size. In the following work, the flow rate should be adjusted to the appropriate size at any time to ensure that the oil temperature does not exceed 55 ℃. ③ When the main power supply of squeeze casting molding machine is connected, all contactors and transformers in the control cabinet should be in the power on state, and then turn the power key switch of control circuit to the power on position. ④ Start the oil pump: press the “start pump” button on the control cabinet door. At this time, the main motor starts according to the Y – △ step-down starting mode. At the same time, because there is no action command, the proportional relief valve is in the unloading state, and the total pressure of the pressure gauge is zero. The actual pressure value is not displayed until the control system gets the action command.
(2) Manual operation: manual operation is mainly used to install the mold, adjust the mold or adjust the machine. In this working state, the manual button or switch sends out a command, which makes the machine execute an action according to a single command. To achieve manual control, first turn the linkage / manual selection button to “manual”. In the manual operation state, in order to facilitate the installation and debugging of the mold, part of the safety interlock function is cancelled. Therefore, special attention must be paid to leave the dangerous area to avoid personal injury when the machine moves. Especially when more than one person works at the same time, they must give feedback to each other. Only after all operators confirm that they are safe can they issue operation instructions to avoid accidents.
(3) Linkage operation: turn the manual / linkage transfer switch to the “linkage” position, and the machine will enter the linkage preparation state. In the linkage mode, only two operation commands need to be executed in the whole squeeze casting process, and the rest actions are executed in automatic sequence. The start of linkage operation must and can only be carried out when each oil cylinder is in the designated original position and meets the interlocking requirements. At this time, the “home” signal light is on. The command to start linkage operation is to press two closing buttons with both hands at the same time. At this time, the injection support moves to the left, closes the mouth after moving to the right, closes the pin after closing the mouth, closes the mold after the pin is in place, holds the brake after closing the mold, locks the mold after the brake is in place, and the length of the mold locking is controlled by the time (adjusted according to the mold size). When the mold locking time is up, the injection lamp is allowed to be on, the slow injection is allowed to be on after the injection lamp is on, and the fast injection is allowed after the injection stroke rod disconnects the proximity switch Pressurization: when the pressurization pressure reaches the set pressure, the extrusion begins; when the extrusion pressure reaches the set pressure, the extrusion begins; when the extrusion time arrives, the cooling time begins. After injection, the time of waiting for the casting to solidify is used to supply pressure oil to the accumulator. According to the amount of pressure oil consumed in the accumulator after each injection, the pressure storage time should be set. After reaching the set time, the hydraulic oil pump will unload automatically. When the cooling time is up, the next action is to extrude and retreat (the length of extrusion and retreat stroke is controlled by time), die locking and retreat (the length of die locking and retreat stroke is controlled by time). After the die locking is in place, it is to release the brake and retreat to the position, it is to open the mold, open the mold and eject at the same time, open the mold and eject after the set ejection time The rod and injection rod automatically return, press back to the position, enter the latch back, the latch back to the position, enter out of the mouth, leave the mouth in place, enter the injection support to the right, the injection support to the right, and the original position light is on. At this time, one operation cycle ends and is ready to receive the closing instruction of the next cycle.
The physical drawing of the equipment site is shown in Figure 2. The equipment has two emergency stop safety buttons. The red mushroom button is set on the control cabinet door and the operation box to stop all actions immediately. After pressing this button, the control power is cut off immediately, all contactors are disconnected, all running motors stop rotating, and all hydraulic valves return to their original positions.