Copper can promote the formation of pearlite structure, improve the uniformity of microstructure and properties of nodular cast iron, increase the tensile strength and hardness of nodular cast iron, and reduce the low-temperature impact toughness and elongation. The figure shows the effect of copper on mechanical properties.
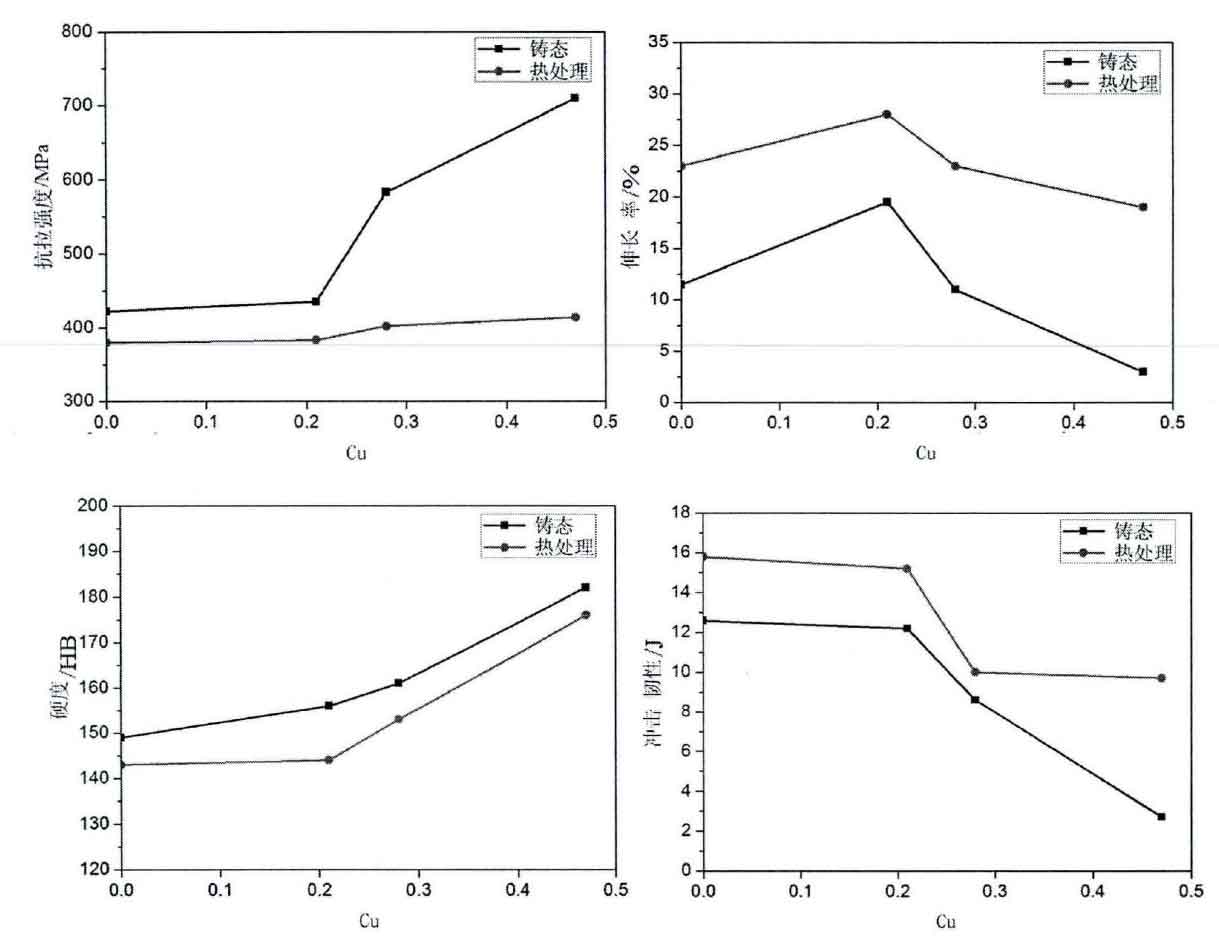
It can be seen from the figure that when WCu < 0.2%, the tensile strength, elongation and hardness of nodular cast iron as cast and heat treatment increase slightly, and the low-temperature impact toughness decreases slightly. When WCu > 0.2%, the tensile strength and hardness of nodular cast iron increase rapidly, and the elongation and low temperature impact toughness decrease significantly. After heat treatment, except for the obvious improvement of tensile strength, other mechanical properties are basically the same as those of nodular cast iron as cast. When 0.3% copper is added, the effect is obvious.
Copper is one of the alloying elements commonly added to nodular cast iron (also known as ductile iron) to modify its mechanical properties. The primary effects of copper in nodular cast iron are related to its influence on the matrix structure and the precipitation of secondary phases, which can significantly impact the iron’s strength, hardness, and wear resistance. Here’s how copper content affects the mechanical properties of nodular cast iron:
Strength and Hardness
- Increased Strength: Adding copper to nodular cast iron can increase its tensile and yield strength. Copper enhances the strength by promoting the formation of pearlite in the iron matrix. Pearlite is a microstructure that is stronger and harder than ferrite, which is the softer and more ductile phase typically present in nodular cast iron.
- Enhanced Hardness: The presence of copper increases the hardness of nodular cast iron. This is primarily due to the increased pearlite content, as pearlite is harder than ferrite. The hardness is beneficial for wear resistance but may reduce machinability.
Wear Resistance
- Improved Wear Resistance: Copper additions can improve the wear resistance of nodular cast iron. The enhanced wear resistance is a result of the increased hardness and strength provided by the copper-induced pearlitic structure. This makes copper-alloyed nodular cast iron suitable for applications involving high wear conditions, such as gears and valve components.
Impact on Ductility
- Reduced Ductility: While copper improves the strength and hardness of nodular cast iron, it can also lead to a reduction in ductility. The increased pearlite content, while beneficial for strength and hardness, makes the material less ductile compared to a ferritic matrix. This trade-off between strength/hardness and ductility needs to be carefully considered in the design and use of copper-alloyed nodular cast iron.
Corrosion Resistance
- Potential Improvement in Corrosion Resistance: Copper is known to enhance the corrosion resistance of some iron-based alloys. In nodular cast iron, the effect of copper on corrosion resistance can be positive, especially in certain environments. However, the extent of improvement depends on the specific composition of the alloy and the environmental conditions.
Optimal Copper Content
The optimal amount of copper added to nodular cast iron depends on the specific requirements of the application, including desired mechanical properties and operational conditions. Typically, copper content in nodular cast iron can range from about 0.5% to 2.5%. The precise effect of copper on the mechanical properties of nodular cast iron will vary with its content, the casting process, and the heat treatment applied, among other factors.
In summary, copper is used to enhance the strength, hardness, and wear resistance of nodular cast iron, at the expense of some reduction in ductility. The balance of these properties can be adjusted through careful control of the copper content and the overall alloy composition, making nodular cast iron adaptable to a wide range of industrial applications.