The casting hot spot is generally divided into structural hot spot and process hot spot. The structural hot spot refers to the node or area where the metal accumulation volume is large and the heat released during solidification is more than that of the adjacent structure of the main reducer housing casting geometry structure, which is composed of the casting geometry structure. Due to the requirements of the casting process, the hot spot formed on the casting due to the setting of risers, internal runners, vents, etc. or the upgrading of the original structure hot spot form is called the process hot spot. Due to the long solidification time of hot spot and the large volume loss caused by volume shrinkage, shrinkage cavity and shrinkage porosity are easy to occur under the condition of defect and shrinkage supplement measures, which will affect the casting quality.
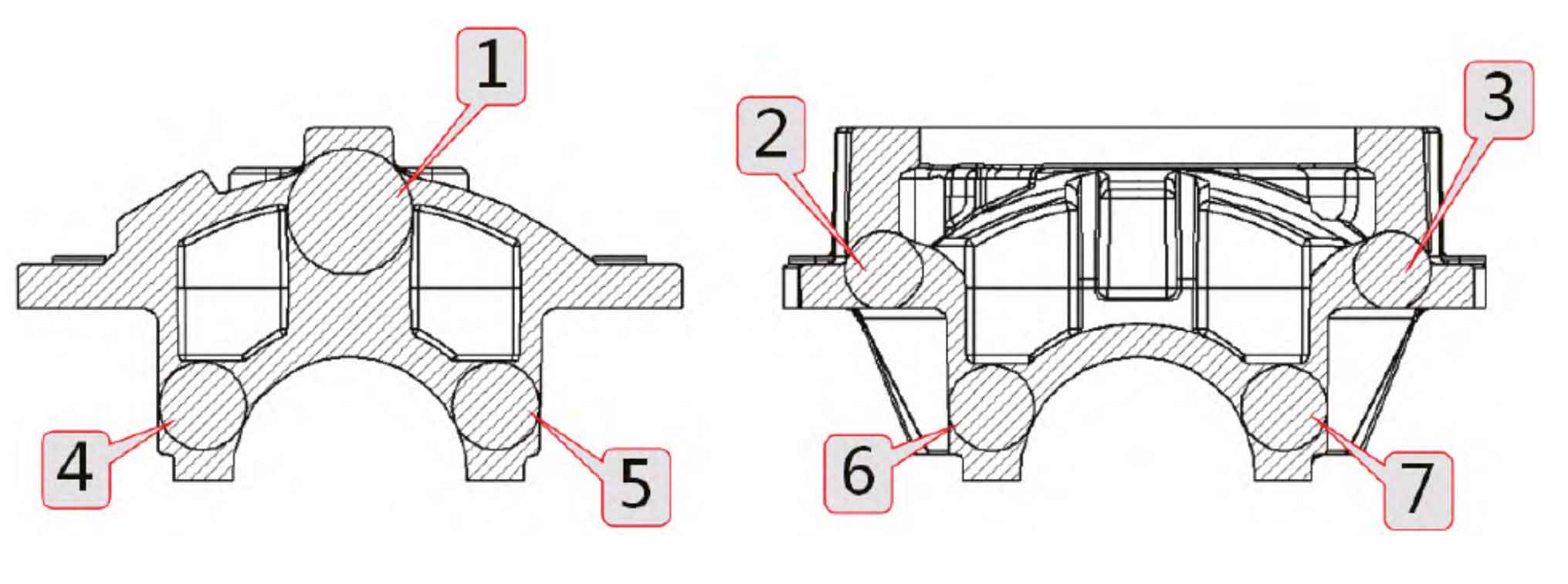
According to the structural characteristics and pouring position of the existing main reducer shell, the position of the casting hot spot is analyzed. There are mainly seven structural hot spots as shown in Figure 1. From the actual production situation, the hot spots 4, 5, 6 and 7 are located in the lower box, and the hot spots are relatively small. The gravity self-feeding effect is good. No shrinkage holes are found during the production process and the dissection of the production parts. The main defects of shrinkage and porosity are hot spots 1, 2 and 3.

Analysis of the existing casting process: ① In terms of chemical composition, the original process meets the requirements by comparing with the same material product process and calculating the carbon equivalent; ② In the design of gating and riser system, in order to improve the production efficiency and process yield, the original process arranged three pieces of one type in the KW line. The riser selection only conforms to the modulus method, not the volume method, the riser is too small, and the amount of molten iron provided is insufficient; ③ The boss position is far away from the flange, and the existing gating and riser can not feed it. The existing process is simulated by intercepting one of them. The simulation results show that the feeding channel is disconnected from the flange during the solidification of the boss position, and an isolated liquid phase zone is formed inside the product, that is, adding a riser outside the flange can not feed the boss position, as shown in Figure 2.