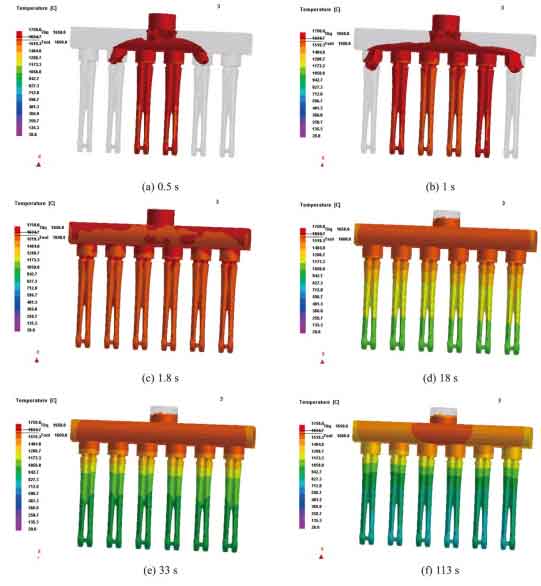
Figure 1 shows the mold filling and solidification of the investment casting process plan. From Figure 1, it can be seen that the investment casting conforms to the mold filling characteristics of the open gating system when filling. First, the middle two investment castings are filled, and then the mold is filled to both sides in sequence. After the completion of the mold filling in 18 seconds, the solidification begins. The temperature field of the six products during solidification is the same, and the temperature field from bottom to top shows the sequential solidification. Figure 2 shows the shrinkage defects formed in the hot spot and the area where the shrinkage is not in place after solidification. The shrinkage defects are distributed at the large wall thickness ratio of the rod opening, and the other is φ 10 mm hole. It can be seen from Figure 2 that in order to prevent deformation, the hole is cast solid and anti-deformation reinforcement is added. The diameter of anti-deformation reinforcement is φ 7mm, the increase of anti-deformation reinforcement introduced the generation of hot spots, resulting in shrinkage defects at the hot spots of the two rod ends of the product.
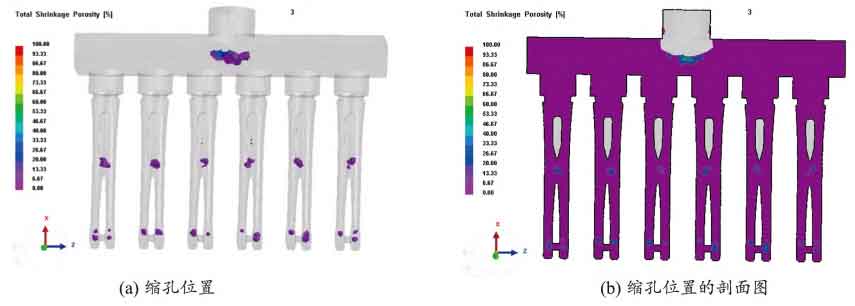
Figure 3 shows the stress distribution of the investment casting process plan. From Figure 5, it can be seen that the stress is concentrated at the anti-deformation rib at the end of the rod and at the large wall thickness ratio of the rod opening. The stress at the anti-deformation reinforcement at the end of the rod is greater than 300 MPa. When the anti-deformation reinforcement is cut off, the stress release will cause large deformation. The stress at the large wall thickness ratio of the rod opening is greater than 120 MPa, and there are also large shrinkage defects. In the process of use, the stress release and shrinkage defects interact, which is easy to form crack defects and affect the service performance of investment castings.
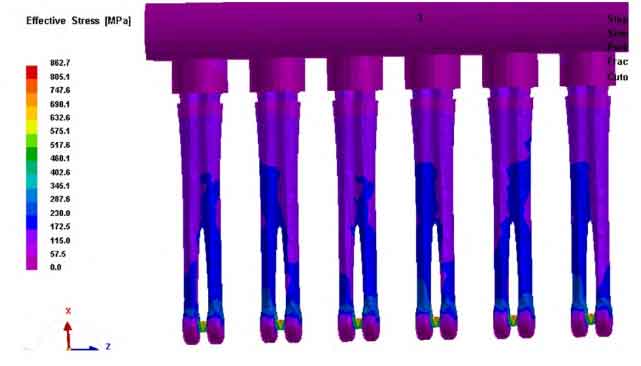