CAE (Computer Aided Engineering Analysis) simulation can increase design functionality, reduce design costs, and shorten design cycles; Adopt optimization design to find the best product design scheme and reduce material consumption or cost. As shown in the table, it is a table of product simulation parameters.
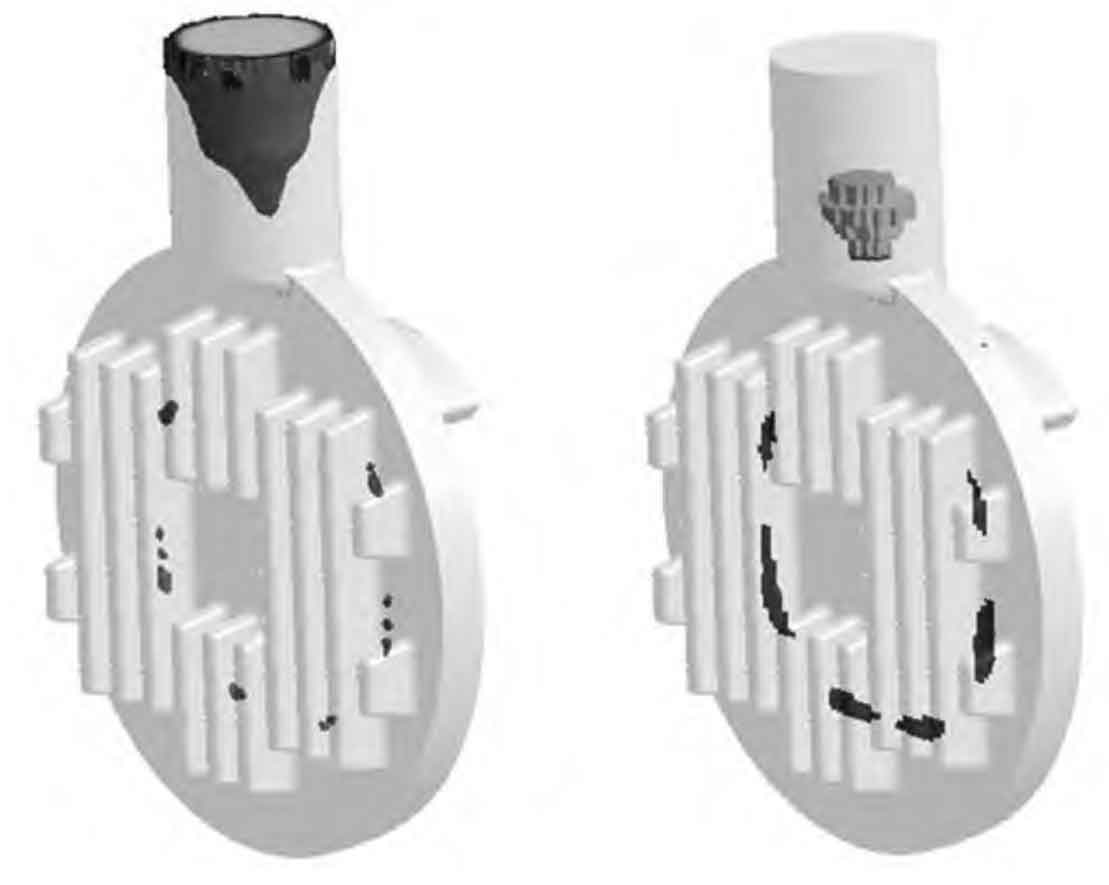
The CAE simulation software is used to simulate and analyze the casting process of the product. The simulation results are used to determine the tendency of shrinkage and porosity in the steel casting, and the casting process risers, chills, and subsidies are adjusted and optimized to ensure the internal quality of the product. Through optimization and adjustment, the final CAE simulation results show that the product and riser modulus meet the sequential solidification requirements, the riser finally solidifies, and the product has no shrinkage tendency. As shown in the figure, it is a porosity and heat node diagram.
At the same time, conduct mold filling simulation on whether the product pouring system is reasonably designed, whether the liquid metal rises steadily in the mold, and whether there are turbulence, splash, and entrainment processes. The simulation results show that the product pouring system design meets the requirements, conforms to the design specifications of the pouring system, and the liquid metal filling process is stable and free of splashes.