Due to the small structure of the steel casting and the relatively uniform wall thickness of the steel casting, the pouring system adopts an open pouring system with central pouring. This pouring system has the advantages and disadvantages of both top and bottom pouring systems, ensuring a smooth filling process with a small temperature difference between the upper and lower molds of the liquid metal, and avoiding sand inclusion defects caused by the direct impact of the liquid metal on the sand core.
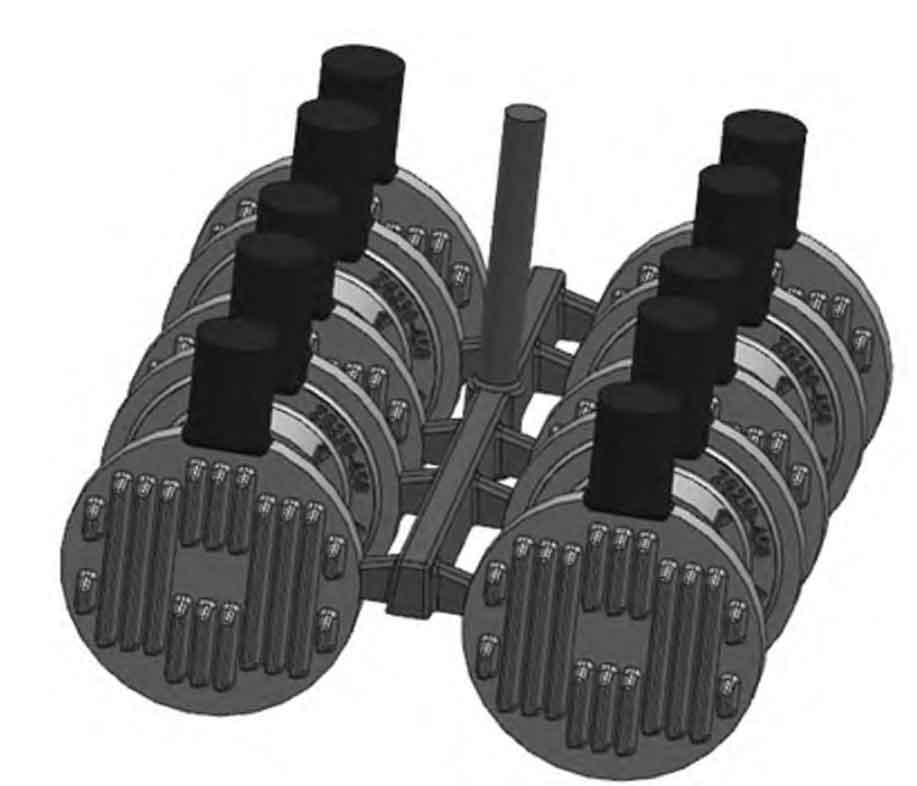
Steel castings are melted using a medium frequency induction furnace with argon blowing for degassing. During tapping, aluminum particles are used for deoxidation. Due to the small thickness of the product, it is necessary to ensure the temperature of the molten steel. Before tapping, the ladle should be baked to ensure that the temperature of the ladle is ≥ 800 ℃. The tapping temperature should be controlled at 1650~1670 ℃. After tapping and slag removal, the temperature can be measured to 1585~1595 ℃ before pouring.