Due to the defects of insufficient pouring at the top of the cylindrical part of the shell in Scheme 1 and Scheme 2, through analysis of Figure 7 and Figure 9, it is found that there are also many porosity defects in Scheme 1 and Scheme 2, and there is also shrinkage and porosity at the base in actual production. Therefore, a third scheme (see Figure 1) was designed, and the position of the inner gate was adjusted. Four open risers were designed, two of which have a diameter of 110mm and a height of 350mm. The other two exposed risers are stepped in shape, with a lower diameter of 200mm and a height of 32.5mm, and an upper diameter of 135mm and a height of 330mm.
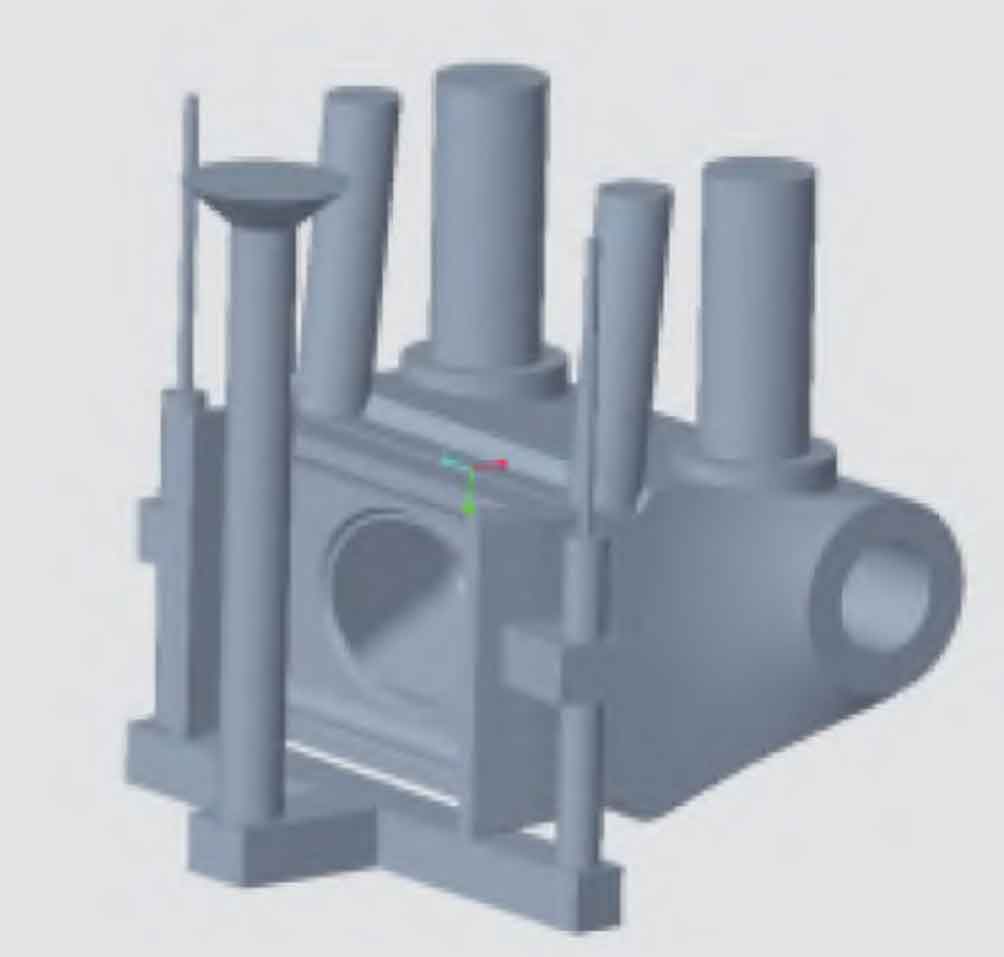
The filling process of the third process scheme is shown in Figure 2. When liquid metal enters the mold cavity, it fills both the lower part of the inner gate and the right side of the inner gate, and then fills from bottom to top. The filling process starts from bottom to top, which is conducive to the discharge of gas from the mold cavity and reduces the formation of air holes in the steel casting. From the perspective of temperature distribution during the mold filling process, during the entire mold filling process, the temperature of the base part of the steel casting is basically low, while the temperature of the cylindrical part is high. When the initial pouring temperature is 1560 ℃, the minimum temperature at the end of mold filling is about 1100 ℃. From the temperature field during the mold filling process, it can be seen that the temperature of the molten metal at the inner runner is slightly higher. At the initial stage of pouring, the temperature of the molten metal decreases relatively quickly, while as the pouring continues, the temperature decline rate of the molten metal decreases and is basically at a stable stage. That is, at the beginning of pouring, the heat loss of molten metal is relatively serious, while as the pouring time increases, the heat loss is relatively small.
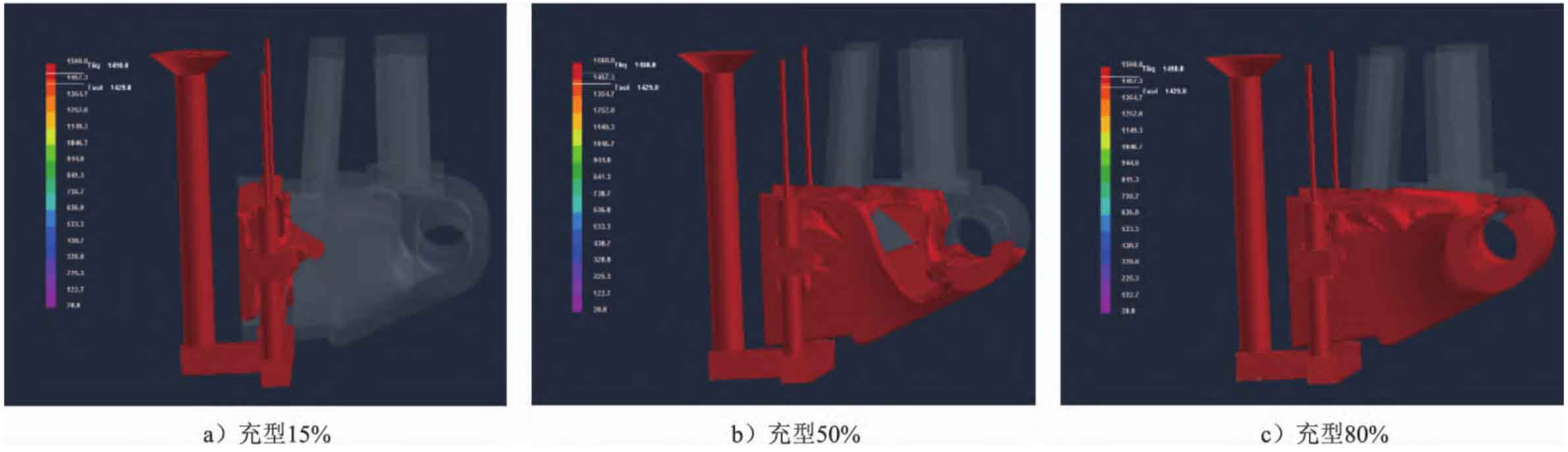
The solidification process of liquid metal is shown in Figure 3. Overall, the time required for complete solidification of steel castings is relatively long, and the solidification speed is much slower than mold filling. The temperature distribution of the steel casting during the entire solidification process is basically gradually increasing from the base to the cylindrical part. The temperature at the base is relatively low, solidification occurs first, and the temperature at the cylindrical part is relatively high, that is, the thin-walled part of the steel casting solidifies first, and the thicker part of the wall solidifies later. Risers are installed at the post solidification part to enhance feeding. After solidification, the steel casting has no defects, which proves that this process is reasonable.
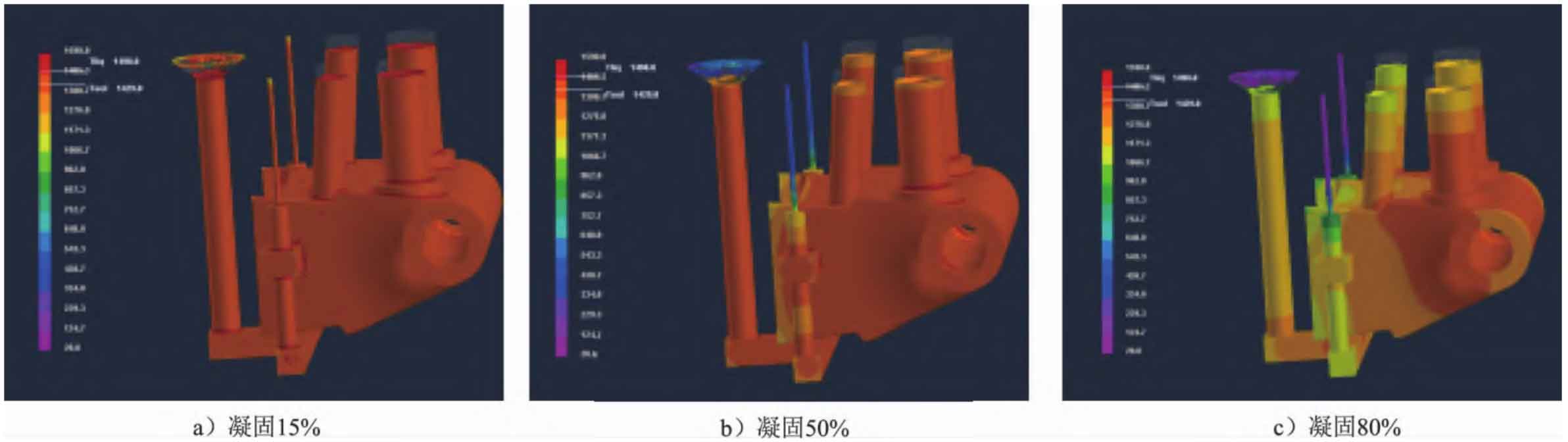