There are many casting process parameters that affect the forming quality of fixed disk investment castings, such as liquid metal pouring temperature, shell preheating temperature, pouring speed, deoxidization, and cooling speed of fixed disk investment castings. The first three factors are mainly analyzed to study their impact on the quality of the fixed disk during investment casting.
In the investment casting process of general castings, the pouring temperature is generally 50 to 100 ℃ higher than the alloy liquidus temperature. When conducting simulation analysis on thin-walled castings with small overall size and complex structure, it is generally 70 ℃ higher. Combining with the actual pouring process, the pouring temperature is selected as 1550, 1560, and 1580 ℃. The mold shell preheating temperature of general alloy steel castings is between 800 and 1015 ℃. Considering that the fixed disk is a thin-walled part and has a complex structure, in order to ensure its forming quality, it is necessary to appropriately increase the preheating temperature of the mold shell. Therefore, in this simulation, the mold shell preheating temperatures are selected as 900, 1000, and 1100 ℃, respectively.
The pouring speed of molten metal has a significant impact on the quality of fixed disk investment castings and the entire casting process. Excessive speed can cause impact damage to the surface of fixed disk investment castings, while too low speed can affect production efficiency. Based on the theoretical calculation of the pouring speed and comprehensive production experience, it is recommended that the pouring time is generally 3-5 seconds and the pouring speed is 200~400 mm/s. The pouring speeds are selected as 200, 300, and 400 mm/s.
level | Pouring temperature/℃ | Pouring speed/(mm · s ^ – 1) | Shell preheating temperature/℃ |
1 | 1550 | 200 | 900 |
2 | 1560 | 300 | 1000 |
3 | 1580 | 400 | 1100 |
Through orthogonal experimental method, an orthogonal experimental Table 1 was designed and established to optimize the process parameters of the fixed disk.
Experiment No | Pouring temperature/℃ | Pouring speed/(mm · s ^ – 1) | Shell preheating temperature/℃ | Filling time/s | Shrinkage ratio (%) |
1 | 1 | 1 | 1 | 3.9216 | 1.8529 |
2 | 1 | 2 | 2 | 3.7005 | 1.9368 |
3 | 1 | 3 | 3 | 3.3782 | 1.8499 |
4 | 2 | 1 | 2 | 3.1731 | 1.8775 |
5 | 2 | 2 | 3 | 3.7413 | 1.7984 |
6 | 2 | 3 | 1 | 3.6028 | 1.8182 |
7 | 3 | 1 | 3 | 3.5219 | 1.8972 |
8 | 3 | 2 | 2 | 3.3782 | 1.9170 |
9 | 3 | 3 | 1 | 3.0732 | 1.8877 |
According to the orthogonal experimental method, 9 sets of experimental schemes for process parameters of L9 (33) orthogonal experiments can be obtained. Finite element models are established for numerical simulation of these 9 sets of schemes, and the filling time of each set of experimental schemes is obtained. The sum of shrinkage and porosity values is calculated in the view CAST module. This is used as the optimization reference value, as shown in Table 2.
Process parameters | Shell thickness/mm | Shell preheating temperature/℃ | Pouring temperature/℃ | Pouring speed/(mm · s^-1) | Filling time/s | Setting time/s | Shrinkage ratio (%) |
Numerical Value | 6 | 1100 | 1560 | 300 | 3.74 | 368.67 | 1.80 |
As can be seen from Table 2, the shrinkage ratio of L5 experiment is 1.7984%, which is the minimum value in 9 groups of experiments; The shrinkage rate of L2 experiment was 1.9368%, which was the largest in 9 groups of experiments. The forming quality of fixed disk investment castings was the most unsatisfactory. Based on the results of orthogonal experiments, referring to the shrinkage ratio of each group of experiments, and based on the principle that the smallest shrinkage ratio is the best, the optimal process parameter group A2B2C3 is obtained by range analysis. The process parameter scheme is shown in Table 3.
The mold filling state diagram, solidification state diagram, and shrinkage porosity distribution diagram of the optimal fixed disk scheme are shown in Figures 1 to 3, respectively.
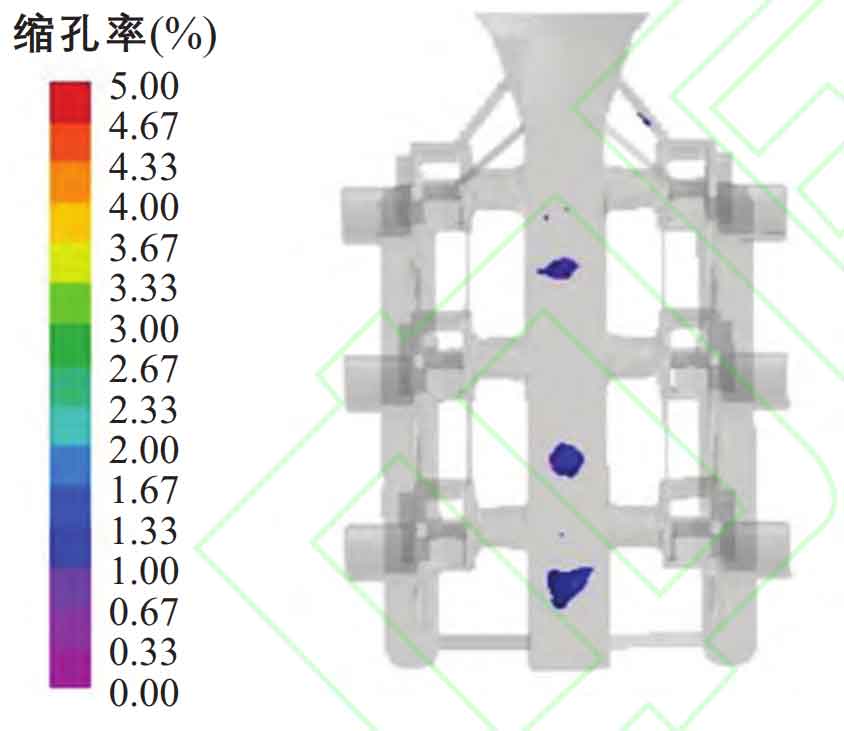