1. Process Measures
(1) The riser on the long platform of the support steel casting was originally placed in the middle, but the shrinkage hole was at the inner end, so the riser was extended towards the inner end.
(2) Although there is no shrinkage around the casting hole of the support steel casting, there is still shrinkage porosity at the nearby hot spot. The casting hole cannot be further enlarged and the feeding riser cannot be placed. Therefore, it is considered to use external cold iron and replace the sand core of the casting hole with round steel to increase the cooling effect.
(3) There are large shrinkage holes at the internal hot joints of the support steel casting. Due to the coated sand shell, the external cold iron cannot be placed, and the feeding riser is also difficult to place. After multiple combinations of the shell structure, it was found that the outer wall and inner cavity of the shell can be utilized to add plugs and form a concealed feeding riser. After grinding and shrinking the channel, shaping the shape of the hidden riser, and pasting the plug, a intact hidden riser was formed. The three-dimensional diagram of the improved design of the casting process for bracket steel castings is shown in Figure 1.
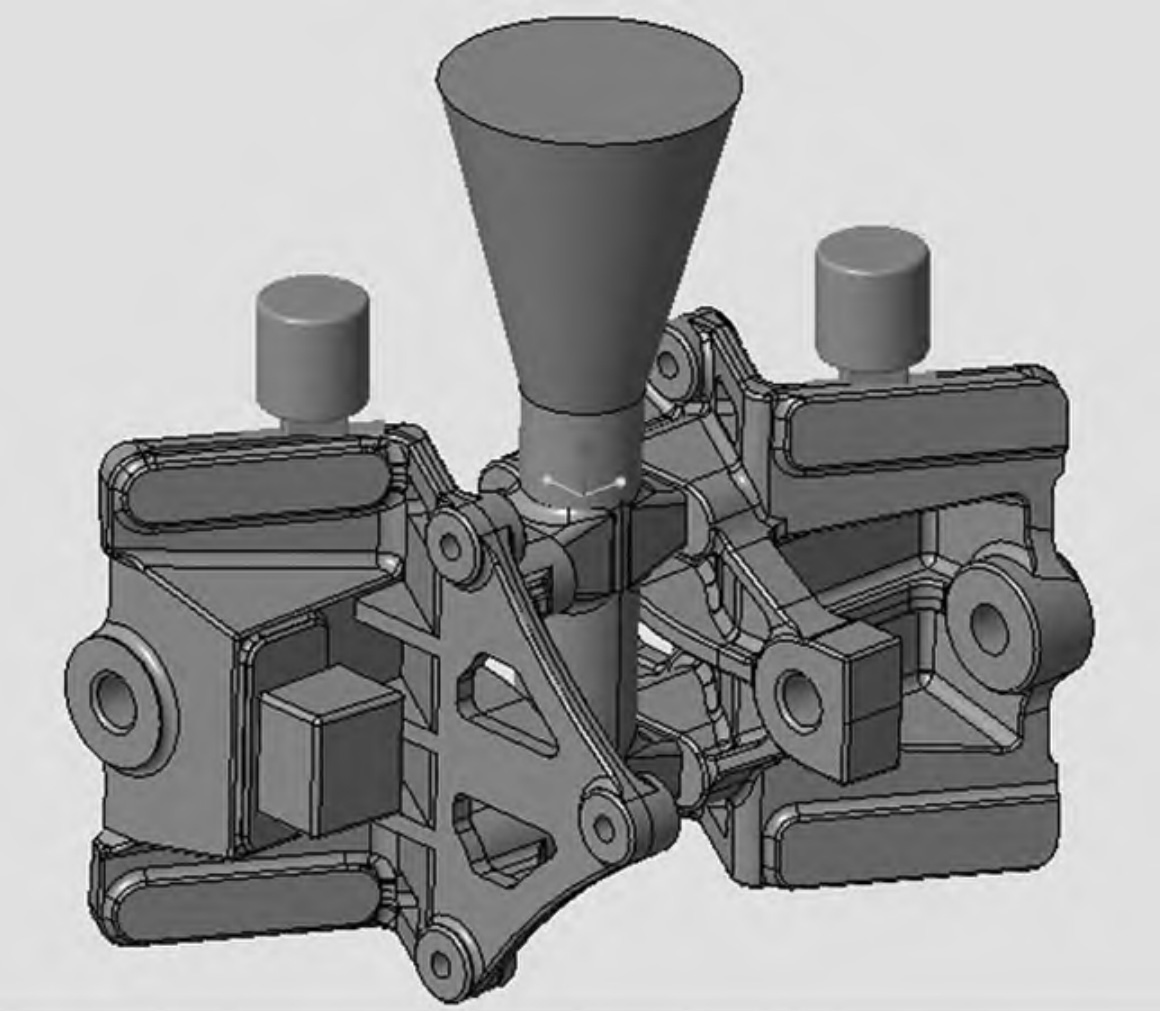
2. Production validation
The improved bracket steel castings were verified in production. Through ultrasonic and cutting inspections, no shrinkage or porosity was found inside the bracket steel castings, indicating that the product is qualified and the improved process measures are effective. The photo of the bracket cast steel after dissection (without defects) is shown in Figure 2.
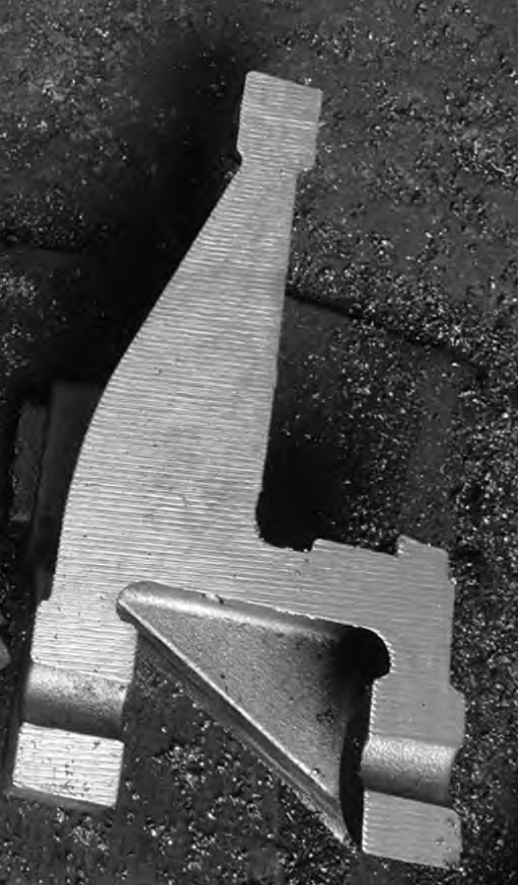