Based on the simulation results and analysis of the initial process of precision casting turbine guide, it can be concluded that there are severe turbulence phenomena, high risk of slag entrapment, many shrinkage porosity defects, and low metal utilization rate in the initial precision casting process. Therefore, this section optimizes the initial precision casting process based on the concept of excellent metallurgical quality and engineering technology cost control.
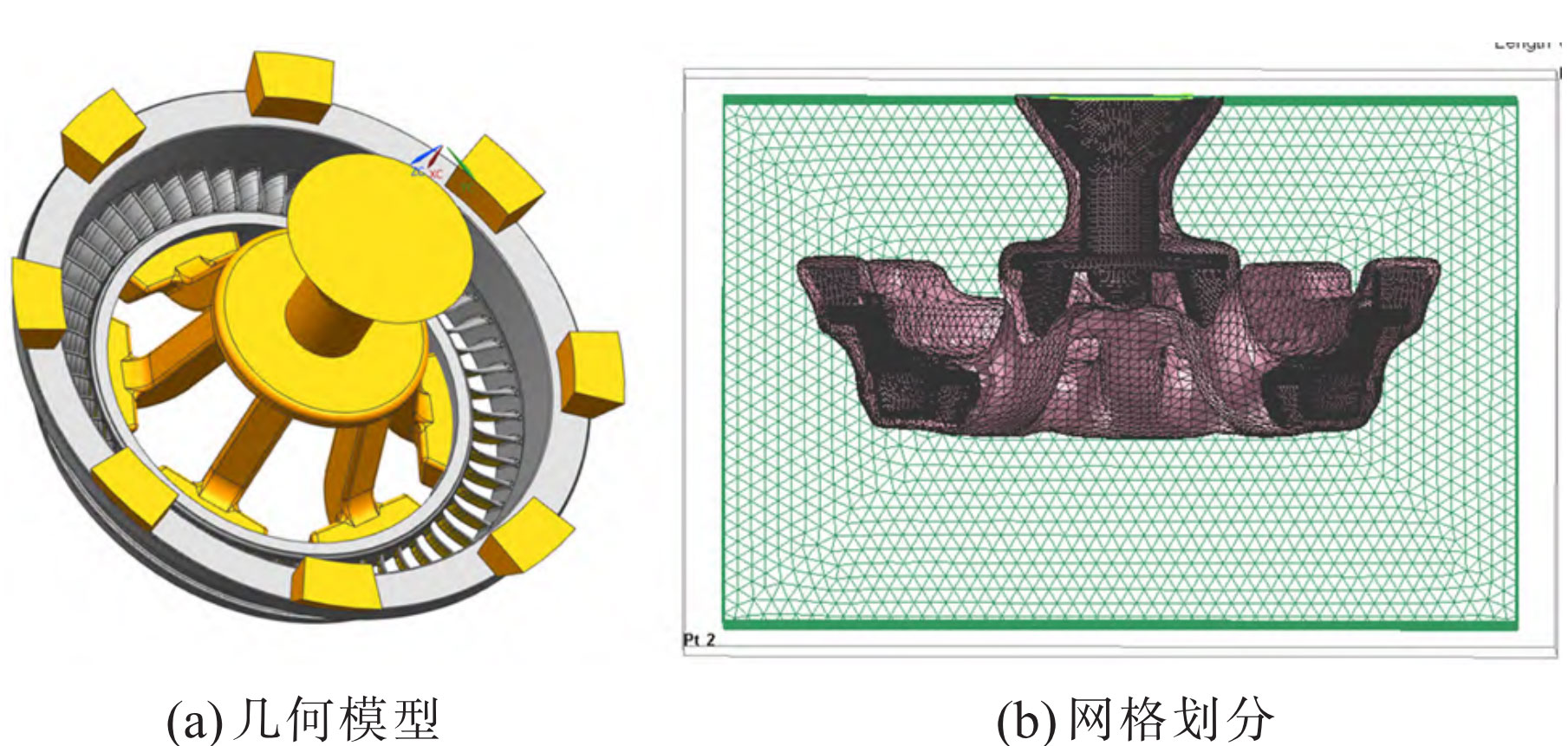
Firstly, the original top bottom composite pouring method was changed to bottom pouring, and the “gyroscope” shaped gate cup was changed to a “funnel+cylinder” shape to eliminate the turbulence phenomenon of alloy liquid in the outer ring flange area and ensure the smooth filling of metal liquid; Then, adjust the length of the original riser from 110mm to 40mm, increase the number of risers from 6 to 8, and evenly distribute them in the flange area to avoid shrinkage defects caused by hot joints in the flange; Subsequently, fill the gap between the two blades with iron sand to ensure the sequential solidification of the blade interior, blade to inner ring, and blade to outer ring areas, in order to avoid the occurrence of shrinkage porosity and porosity defects; Finally, ProCAST software is used to model and simulate the optimized process of precision casting turbine guide, and its geometric modeling and grid micro element are shown in the figure.
In addition, using ProCAST software, it was found that the mass of the optimized precision casting turbine guide gating system was reduced by 42.98kg compared to the initial gating system, and the metal utilization rate of the optimized process was 43.18%, which is about 3.6 times that of the initial process.