According to the optimal parameter combination, conduct numerical simulation verification on the casting process of aluminum alloy sleeves. The comparison of scheme results is shown in the table. By comparing the optimized prediction scheme with the actual simulation scheme, it can be seen that the relative error of shrinkage porosity volume is 1.29%, and the relative error of SDAS value is 0.66%. This indicates that the optimization method has relatively small error and is accurate and reliable. By comparing the optimized process plan with the initial process plan, it can be seen that the shrinkage volume and SDAS value of the optimized plan have decreased by 13.2% and 0.14%, respectively. The forming quality of the casting has been improved and the mechanical properties have been improved.
Plan | Initial process plan | Optimization plan (prediction) | Optimization plan (actual) |
Shrinkage volume/cm^3 | 0.3199 | 0.2741 | 0.2777 |
SDAS/μm | 36.41 | 36.12 | 36.36 |
The figure shows a numerical simulation comparison between the initial plan and the optimized plan. From the shrinkage and porosity diagram, it can be seen that the optimized casting eliminates shrinkage defects and significantly reduces shrinkage defects, especially in the lower wall area of the casting, where the forming quality has been improved to a certain extent. From the SDAS diagram, it can be seen that although the maximum reduction in SDAS after optimization is relatively small, the reduction in SDAS on the casting wall is more significant and uniform, with a denser grain structure and improved overall mechanical properties.
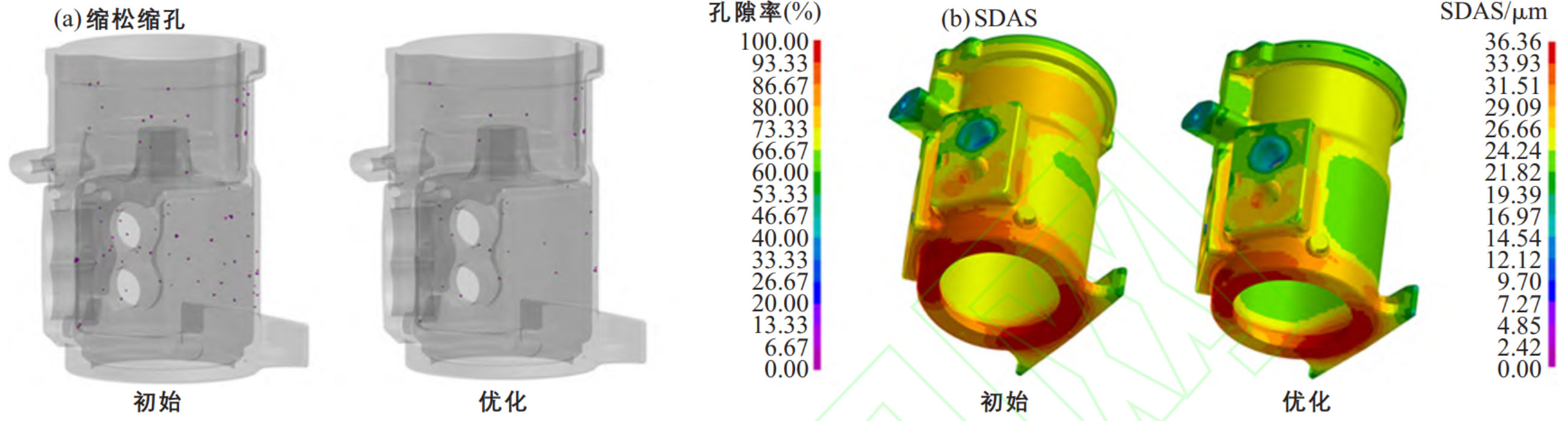
(1) The response surface analysis method was used to analyze the effects of process parameters and their interactions on the molding quality and mechanical properties of castings. For shrinkage and porosity, the weight of factors is: preheating temperature of the side mold>preheating temperature of the upper mold>pouring temperature>preheating temperature of the lower mold; For the SDAS value, the factor influence weight is: lower mold preheating temperature>side mold preheating temperature>pouring temperature>upper mold preheating temperature.
(2) Based on the response surface model, a genetic algorithm model was constructed. After iterative optimization, the optimal process parameter combination for low-pressure casting was obtained: the preheating temperature of the upper mold was 307 ℃, the preheating temperature of the side mold was 330 ℃, the preheating temperature of the lower mold was 394 ℃, and the pouring temperature was 701 ℃.
(3) Numerical simulation verification was conducted on the optimized process parameters, and the shrinkage volume of the casting decreased by 13.2%, the SDAS value decreased by 0.14%, and the molding quality and mechanical properties were improved.
(4) The optimized castings have eliminated shrinkage defects, but there are still a small number of shrinkage defects, indicating that the current mold system has certain limitations. Subsequent work will revolve around the optimization of the cooling system.