Casting defects can occur due to various factors during the metal casting process. Understanding the causes, effects, and appropriate remedies for these defects is crucial for improving casting quality and performance. In this article, we will discuss some of the most common casting defects, their causes, the effects they have on castings, and the remedies to address them effectively.
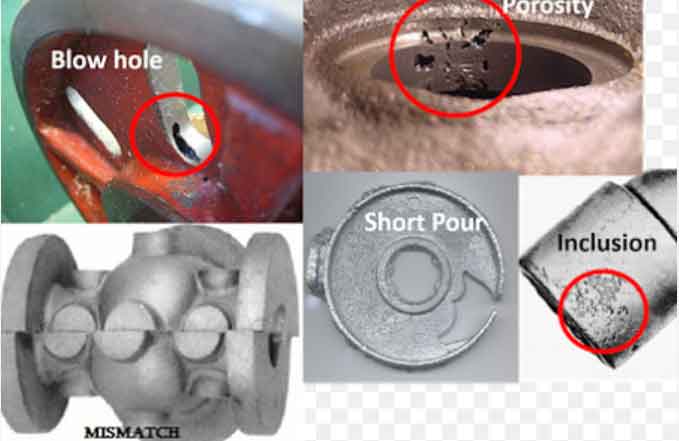
1.Porosity: Causes:
- Entrapped gases in the molten metal due to improper degassing or inadequate venting of the mold.
- High pouring temperature leading to excessive gas generation.
- Inadequate mold permeability preventing the escape of gases.
Effects:
- Reduced mechanical strength and structural integrity.
- Increased susceptibility to cracking and failure under load.
- Diminished corrosion resistance and leak potential.
Remedies:
- Improve mold permeability through the use of appropriate molding materials and additives.
- Optimize mold venting and gating design to allow efficient gas escape.
- Implement proper degassing techniques, such as vacuum or fluxing, to remove gases from the melt.
2.Shrinkage: Causes:
- Insufficient feeding of molten metal during solidification.
- Inadequate riser design or placement.
- Improper cooling rate leading to premature solidification.
Effects:
- Formation of voids, cavities, or shrinkage porosity in the casting.
- Reduced mechanical properties, such as strength and ductility.
- Dimensional inaccuracies and distortion.
Remedies:
- Increase the size and efficiency of risers to provide sufficient molten metal for feeding.
- Optimize cooling rates to promote uniform solidification and minimize shrinkage.
- Use chills or controlled solidification techniques in critical areas to prevent shrinkage defects.
3.Inclusions: Causes:
- Contamination of molten metal by foreign materials such as sand, slag, oxides, or refractory particles.
- Insufficient filtration or inadequate melt treatment.
Effects:
- Weakening of mechanical properties and reduced structural integrity.
- Impaired surface finish and appearance.
- Increased susceptibility to cracking and corrosion.
Remedies:
- Employ effective filtration systems to remove impurities from the molten metal.
- Ensure proper handling and storage of raw materials to prevent contamination.
- Implement appropriate melt treatment practices, such as fluxing or refining, to remove inclusions.
4.Surface Defects: Causes:
- Mold erosion or degradation leading to sand or mold particles adhering to the casting surface.
- Improper mold or core coatings.
- Insufficient mold release agents.
Effects:
- Aesthetic issues, such as rough surfaces, scabs, or sand inclusions.
- Impaired functionality, especially in cases where surface smoothness is critical.
- Increased susceptibility to corrosion or fatigue failure.
Remedies:
- Regular maintenance and replacement of molds and cores to prevent erosion.
- Proper application of mold coatings and release agents to facilitate easy mold separation.
- Use of suitable mold materials and coatings to minimize surface defects.
5.Misruns and Cold Shuts: Causes:
- Insufficient fluidity of molten metal.
- Inadequate gating system design or improper pouring techniques.
- Premature solidification or inadequate mold filling.
Effects:
- Incomplete castings or sections with incomplete fusion.
- Diminished mechanical properties due to incomplete solidification.
- Reduced dimensional accuracy and integrity.
Remedies:
- Optimize gating system design to ensure smooth and efficient metal flow.
- Control pouring temperature and rate to promote proper mold filling.
- Modify alloy composition or use alloys with better fluidity characteristics.
Understanding the causes, effects, and appropriate remedies for common casting defects is essential for improving casting quality. By addressing the root causes and implementing appropriate remedies, manufacturers can minimize defects, enhance casting performance, and ensure the production of high-quality castings. Implementing proper process control, employing suitable materials and techniques, and continuously monitoring and improving the casting process are key to achieving defect-free castings and maximizing customer satisfaction.