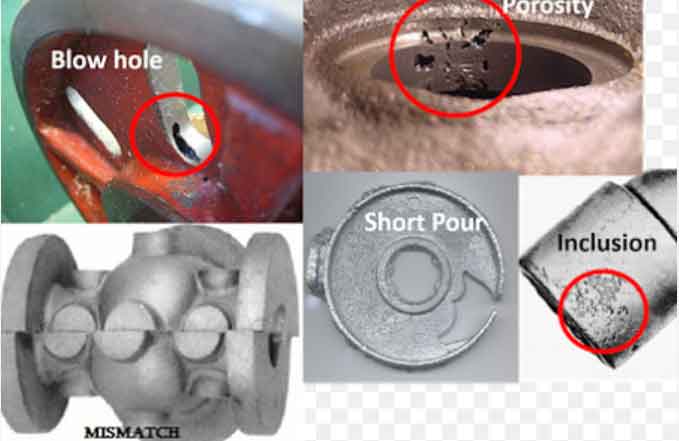
Casting defects can significantly impact the quality and integrity of metal castings. To effectively prevent and address these defects, it is crucial to identify their root causes. By understanding the underlying factors that contribute to casting defects, manufacturers can implement targeted solutions and improve casting quality. This article aims to unveil the culprits behind casting defects by exploring their root causes and providing insights into their identification.
- Process Parameters and Control:
- Pouring Temperature: Inadequate pouring temperature can lead to defects like cold shuts, misruns, or porosity. Temperature control during pouring is critical to ensure proper flow and solidification.
- Cooling Rate: Improper cooling rates can result in shrinkage defects, distortion, or residual stresses. Controlling cooling rates is essential to achieve uniform solidification and minimize defects.
- Mold Design and Venting: Inadequate mold design or insufficient venting can cause defects like porosity, gas entrapment, or inadequate filling. Proper mold design and venting ensure efficient gas escape and complete mold filling.
- Material Properties and Composition:
- Alloy Selection: Inappropriate alloy selection can result in defects such as porosity, inclusions, or cracking. The alloy’s fluidity, solidification characteristics, and compatibility with the casting process should be considered.
- Metal Cleanliness: Contaminants in the metal, such as oxides, slag, or impurities, can lead to inclusions, reduced mechanical properties, or surface defects. Ensuring proper metal cleanliness through melt treatment and filtration is crucial.
- Mold and Core Issues:
- Mold Material and Permeability: Improper choice of mold material or inadequate permeability can cause defects like rough surfaces, erosion, or metal penetration. Selecting suitable mold materials and optimizing permeability is essential.
- Core Design and Quality: Incorrect core design, improper core assembly, or core shift can result in defects like dimensional variations or misruns. Ensuring proper core design, alignment, and quality control is necessary.
- Process Control and Variability:
- Gating System Design: Poor gating system design can cause turbulence, inadequate metal flow, or incomplete mold filling. Optimizing gating system design improves metal flow and minimizes defects.
- Process Variability: Inconsistent process parameters, such as pouring techniques, mold preheating, or mold coating application, can contribute to defects. Establishing standardized procedures and process control measures reduce variability.
- Environmental Factors:
- Humidity and Moisture: Excessive humidity or moisture in molds can cause defects like gas porosity, rough surfaces, or mold degradation. Proper moisture control and mold storage conditions are necessary.
- Atmospheric Conditions: Changes in atmospheric pressure or gas composition can affect the casting process and lead to defects. Monitoring and controlling atmospheric conditions in the casting area are important.
Identifying the root causes of casting defects is vital for effective defect prevention and control. By considering process parameters, material properties, mold and core issues, process control, and environmental factors, manufacturers can pinpoint the culprits behind casting defects. Implementing appropriate measures to address these root causes, such as optimizing process parameters, improving material quality, enhancing mold design, and controlling process variability, allows for the production of high-quality castings. Continuous monitoring, analysis, and improvement of the casting process will help reduce defects, enhance casting quality, and optimize overall manufacturing efficiency.