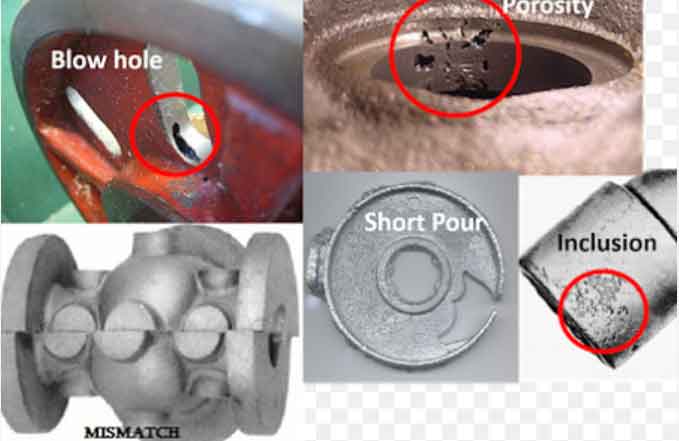
Casting defects can pose challenges in the production process, impacting the quality and performance of castings. Effective troubleshooting and resolution strategies are essential to identify the root causes of defects and implement appropriate corrective actions. This article explores key strategies for unmasking casting defects and achieving effective troubleshooting and resolution.
- Defect Characterization:
- Thoroughly examine and characterize the casting defects. Identify the type, location, size, and frequency of occurrence. Gather visual evidence, perform dimensional measurements, and document the defect characteristics.
- Process Parameter Analysis:
- Analyze the process parameters involved in the casting operation. This includes factors such as melting, pouring, cooling, solidification, mold and core materials, and gating system design. Identify any deviations or abnormalities in these parameters.
- Data Collection and Analysis:
- Collect and analyze relevant data related to the defect occurrence. This may include process parameters, material properties, environmental conditions, and inspection results. Utilize statistical tools and techniques to identify patterns and trends in the data.
- Root Cause Analysis:
- Conduct a systematic root cause analysis to identify the underlying factors contributing to the casting defects. Utilize tools like fishbone diagrams, Pareto analysis, or failure mode and effects analysis (FMEA) to identify potential causes and their interactions.
- Collaborative Approach:
- Involve cross-functional teams comprising process engineers, metallurgists, quality control personnel, and operators in the troubleshooting process. Encourage collaboration and knowledge sharing to gain different perspectives and insights.
- Experimental Testing:
- Perform targeted experimental tests to validate hypotheses and eliminate potential causes. This may involve conducting small-scale trials, adjusting process parameters, or modifying tooling and equipment to evaluate their impact on defect formation.
- Computer Simulation:
- Utilize computer simulation software to model and simulate the casting process. This can provide insights into the flow behavior, solidification, and defect formation mechanisms, allowing for virtual experimentation and optimization.
- Process Optimization:
- Optimize the casting process based on the findings from the root cause analysis and experimental testing. Adjust process parameters, modify tooling or gating design, and optimize cooling and solidification conditions to minimize or eliminate the identified root causes.
- Continuous Improvement:
- Implement a culture of continuous improvement by learning from past defects and incorporating lessons learned into future production. Regularly review and update standard operating procedures (SOPs) and work instructions based on the resolved defects.
- Documentation and Knowledge Management:
- Maintain detailed documentation of the defect analysis, root cause investigation, and corrective actions taken. Develop a knowledge base or database to capture and share troubleshooting experiences and solutions for future reference.
Unmasking casting defects requires a systematic and data-driven approach. By characterizing the defects, analyzing process parameters, conducting root cause analysis, and utilizing experimental testing and computer simulation, manufacturers can effectively troubleshoot and resolve casting defects. Collaboration among cross-functional teams, continuous improvement practices, and thorough documentation contribute to the accumulation of knowledge and the prevention of future defects. With these strategies in place, manufacturers can enhance their casting processes, improve quality, and achieve defect-free castings.