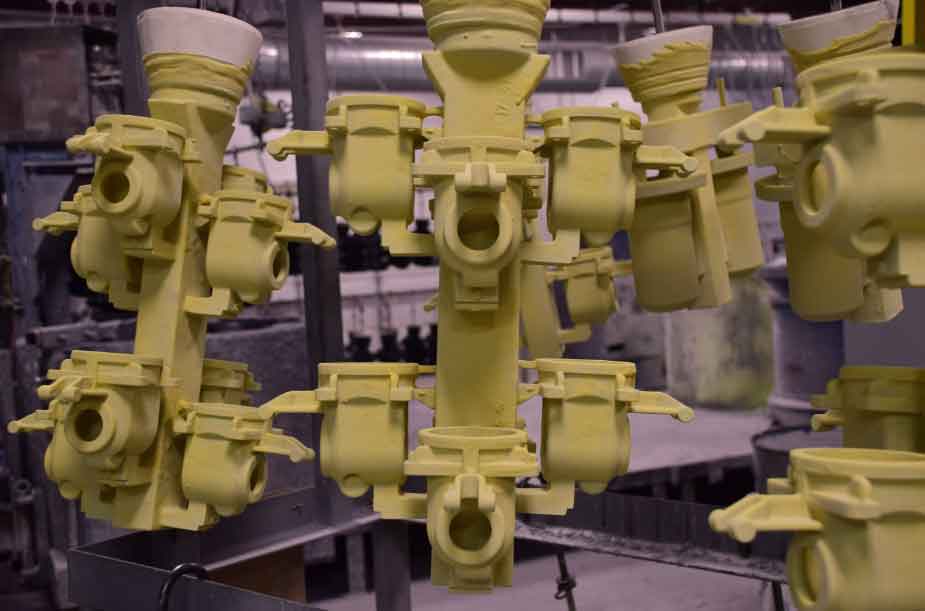
Investment casting, also known as lost-wax casting, offers sustainable solutions for responsible manufacturing. Here’s how investment casting contributes to sustainability in the manufacturing process:
1. Material Efficiency:
Investment casting minimizes material waste by utilizing molds that closely match the final component shape. The near-net shape manufacturing process reduces the amount of material that needs to be machined away, resulting in significant material savings. This reduces the consumption of raw materials and conserves natural resources.
2. Reduced Energy Consumption:
Investment casting requires less energy compared to other manufacturing processes such as machining or forging. The process involves melting the metal at lower temperatures, resulting in lower energy consumption during the casting phase. Additionally, the near-net shape manufacturing reduces the need for extensive machining operations, further reducing energy requirements.
3. Recycling and Reusability:
Investment casting enables the recycling and reusability of materials. Excess metal and sprues generated during the casting process can be recycled and reused for future casting cycles. This reduces the need for virgin materials and minimizes waste generation, contributing to a more sustainable manufacturing process.
4. Waste Reduction:
Investment casting generates minimal waste compared to other manufacturing methods. The molds used in investment casting are made from ceramic or other materials that can be reused multiple times, reducing waste generation. Additionally, the near-net shape manufacturing process reduces the need for additional machining operations, further minimizing waste production.
5. Emissions Reduction:
Investment casting has lower emissions compared to other manufacturing methods. The lower melting temperatures used in investment casting result in reduced greenhouse gas emissions. Furthermore, investment casting can utilize vacuum or controlled atmosphere melting processes, reducing the release of harmful pollutants into the environment.
6. Product Longevity:
Investment cast components are known for their durability and longevity. The high-quality castings produced through investment casting have excellent mechanical properties and corrosion resistance, resulting in longer product lifecycles. This reduces the need for frequent replacements and contributes to a more sustainable manufacturing process.
7. Design Optimization:
Investment casting allows for design optimization, which can lead to more sustainable products. The process enables engineers to consolidate multiple components into a single casting, reducing the overall part count and assembly requirements. This minimizes the use of additional fasteners or joining methods, reducing material consumption and simplifying end-of-life recycling processes.
8. Collaboration for Sustainability:
Investment casting involves collaboration between manufacturers, casting experts, and material suppliers to achieve sustainability goals. Collaboration in the supply chain allows for the selection of sustainable materials, efficient manufacturing processes, and responsible waste management practices.
By focusing on material efficiency, energy reduction, recycling, waste reduction, emissions reduction, product longevity, design optimization, and collaborative sustainability efforts, investment casting offers sustainable solutions for responsible manufacturing. Implementing investment casting in manufacturing processes contributes to resource conservation, waste reduction, and a lower environmental footprint, aligning with the principles of sustainable development.