Lost wax casting is a precision manufacturing process that has been utilized for centuries to create intricate and detailed metal components. In recent years, significant advancements in this technique have made it particularly valuable for producing high-performance alloys. These advancements have enabled the production of components with enhanced durability and efficiency, making them suitable for demanding applications in industries such as aerospace, automotive, and energy. This article explores the techniques involved in lost wax casting for high-performance alloys and their impact on component durability and efficiency.
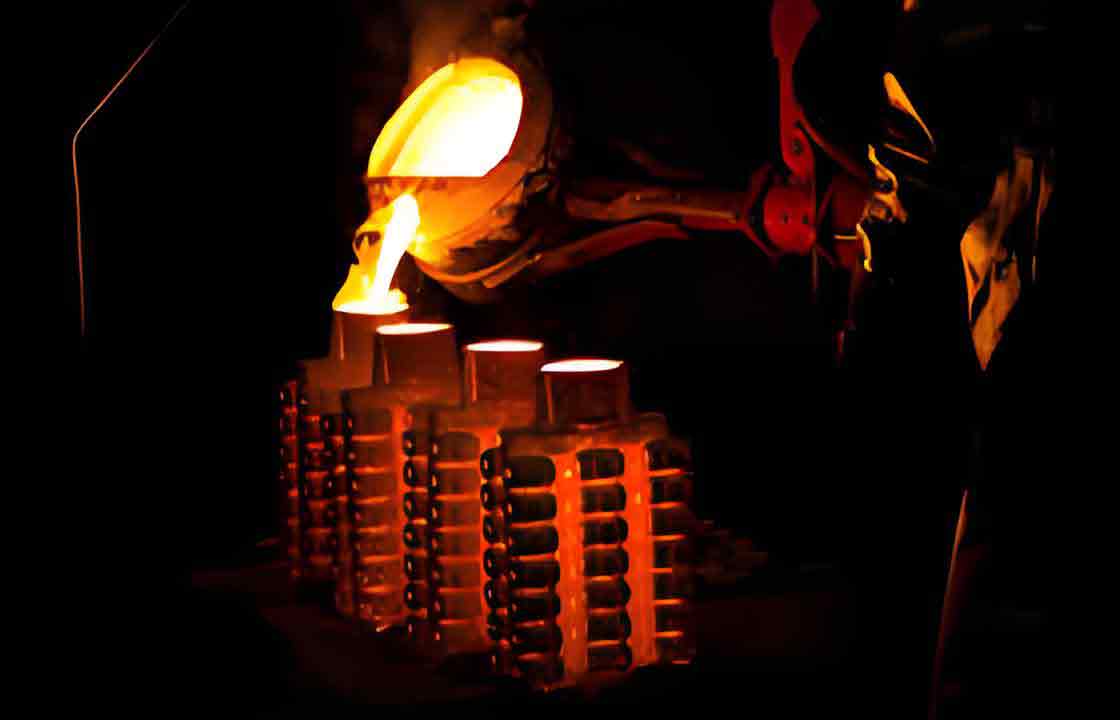
Introduction
Lost wax casting involves creating a wax model of the desired part, which is then coated with a ceramic shell. Once the shell hardens, the wax is melted away, leaving a mold into which molten metal is poured. This process allows for the production of components with complex geometries and high precision. The use of high-performance alloys further enhances the properties of these components, making them suitable for applications that require exceptional strength, corrosion resistance, and thermal stability.
Techniques in Lost Wax Casting for High-Performance Alloys
- Advanced Pattern Creation:
- 3D Printing of Wax Patterns: Utilizes additive manufacturing technologies to create highly detailed and complex wax patterns, improving the precision and repeatability of the casting process.
- Improved Wax Formulations: Development of waxes with better dimensional stability and lower thermal expansion to reduce defects in the final cast parts.
- High-Performance Alloy Selection:
- Superalloys: Use of nickel-based, cobalt-based, and iron-based superalloys that offer superior mechanical properties at high temperatures.
- Titanium Alloys: Known for their excellent strength-to-weight ratio and corrosion resistance, making them ideal for aerospace and biomedical applications.
- Ceramic Shell Improvements:
- Advanced Ceramic Materials: Development of stronger and more heat-resistant ceramic materials for building molds that can withstand the high temperatures and stresses of casting high-performance alloys.
- Optimized Shell Building Techniques: Multi-layer shell construction and controlled drying processes to enhance mold stability and reduce the risk of cracking or deformation.
- Precision Casting Process:
- Vacuum Casting: Implementation of vacuum environments to reduce gas entrapment and improve the quality of the final cast parts.
- Directional Solidification: Control of the solidification process to align grain structures and improve the mechanical properties of the cast components.
- Quality Control and Inspection:
- Non-Destructive Testing (NDT): Techniques such as X-ray, ultrasonic testing, and CT scanning to inspect the internal structure of cast parts and detect any defects.
- Simulation Software: Use of advanced simulation tools to model the casting process, predict potential issues, and optimize parameters for better quality and efficiency.
Impact on Component Durability and Efficiency
- Enhanced Durability:
- Improved Mechanical Properties: High-performance alloys offer superior strength, toughness, and fatigue resistance, extending the lifespan of components.
- Corrosion and Wear Resistance: Alloys such as titanium and superalloys provide excellent resistance to corrosion and wear, reducing maintenance requirements and downtime.
- Increased Efficiency:
- Lightweight Components: The use of high-strength, lightweight alloys reduces the overall weight of components, improving fuel efficiency and performance in aerospace and automotive applications.
- High-Temperature Stability: Components made from high-performance alloys can operate effectively at higher temperatures, improving the efficiency of engines and turbines.
Applications in Key Industries
- Aerospace:
- Turbine Blades and Vanes: Use of superalloys and advanced casting techniques to produce components that can withstand extreme temperatures and stresses.
- Structural Components: Production of lightweight and durable parts for aircraft frames and engine housings.
- Automotive:
- Engine Parts: Manufacturing of high-performance engine components such as turbocharger housings and pistons using lightweight alloys.
- Transmission Components: Precision casting of gears and other transmission parts to improve performance and longevity.
- Energy:
- Turbine Components: Casting of high-temperature, corrosion-resistant parts for gas and steam turbines in power generation.
- Oil and Gas Equipment: Production of durable and reliable components for exploration and drilling operations.
Case Study: Enhancing Durability of Aerospace Turbine Blades
Background: An aerospace manufacturer sought to improve the durability and performance of turbine blades used in jet engines. The goal was to produce blades capable of withstanding higher temperatures and prolonged stress.
Approach:
- Material Selection:
- Chose a nickel-based superalloy known for its high-temperature resistance and mechanical strength.
- Integrated ceramic matrix composites to enhance thermal performance.
- Pattern Creation:
- Utilized 3D printing to create highly detailed wax patterns with intricate cooling channels.
- Improved wax formulations for better dimensional accuracy and surface finish.
- Ceramic Shell Formation:
- Used advanced ceramic materials to build stronger and more heat-resistant shells.
- Applied multi-layer shell construction to prevent cracking and deformation during casting.
- Precision Casting:
- Implemented vacuum casting to reduce gas entrapment and improve overall quality.
- Controlled solidification process to achieve optimal grain structure and mechanical properties.
- Quality Control:
- Conducted X-ray and CT scanning to inspect the internal structure of the cast blades.
- Used simulation software to predict and mitigate potential defects.
Results:
- Achieved a 25% increase in the operating temperature of the turbine blades.
- Enhanced fatigue and creep resistance, extending the blades’ operational lifespan by 35%.
- Improved precision and surface finish, reducing the need for post-casting machining.
- Lowered production costs through automation and reduced defect rates.
Table: Comparative Analysis of High-Performance Alloys in Lost Wax Casting
Alloy Type | Key Properties | Typical Applications |
---|---|---|
Nickel-based Superalloys | High-temperature resistance, excellent mechanical strength | Turbine blades, engine components, structural parts |
Cobalt-based Superalloys | Superior wear and corrosion resistance, good thermal stability | Aerospace bearings, medical implants, turbine parts |
Iron-based Superalloys | Cost-effective, good mechanical properties at high temperatures | Industrial valves, power generation components |
Titanium Alloys | High strength-to-weight ratio, excellent corrosion resistance | Aerospace frames, biomedical implants, automotive parts |
Aluminum Alloys | Lightweight, good thermal and electrical conductivity | Automotive components, aerospace structures |
Conclusion
Lost wax casting techniques have undergone significant advancements, making them highly effective for producing high-performance alloys with enhanced durability and efficiency. These techniques enable the creation of complex, precise components that meet the stringent requirements of modern industries. By leveraging advanced materials, improved pattern creation, and state-of-the-art quality control methods, manufacturers can produce components that offer superior performance and longevity. The continued evolution of lost wax casting promises even greater potential for innovation and efficiency in the production of high-performance alloys, ensuring their vital role in the aerospace, automotive, and energy sectors.