Lost wax casting is a timeless method for producing detailed and precise metal components. While its origins can be traced back thousands of years, recent innovations have significantly advanced the process, making it highly suitable for precision manufacturing in today’s demanding industries. This article explores the latest advancements in lost wax casting and their implications for precision manufacturing.
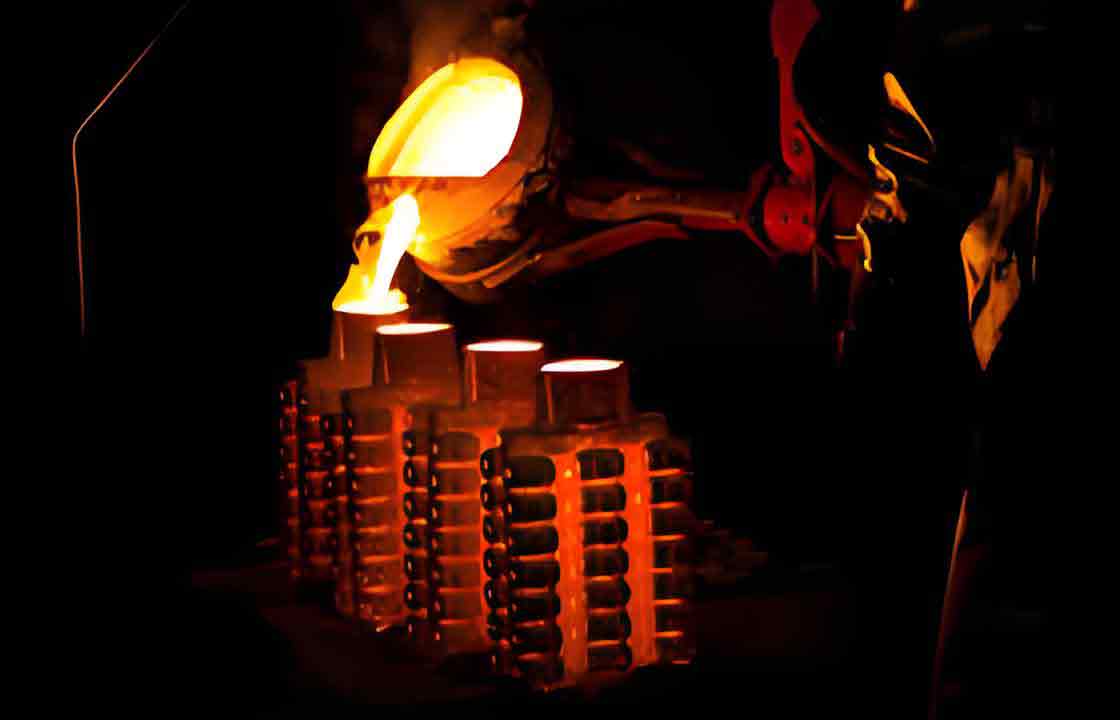
Introduction
Lost wax casting involves creating a wax model of the desired part, coating it with a ceramic shell, and then melting the wax away to form a mold. Molten metal is then poured into the mold to create the final part. This process allows for the production of components with intricate geometries and high dimensional accuracy. Modern advancements in materials, processes, and technologies have further refined lost wax casting, enhancing its precision and efficiency.
Key Innovations in Lost Wax Casting
- 3D Printing for Wax Patterns:
- Additive Manufacturing: Utilizes 3D printing to create highly detailed and complex wax patterns, enabling rapid prototyping and design flexibility.
- Precision and Repeatability: Improved accuracy and consistency in wax patterns, reducing defects and enhancing the quality of final cast parts.
- Advanced Ceramic Shell Materials:
- High-Performance Ceramics: Development of stronger and more heat-resistant ceramic materials for creating molds that can withstand extreme casting conditions.
- Multi-Layer Shell Construction: Techniques to build durable and stable ceramic shells, reducing the risk of cracking and deformation.
- Enhanced Alloy Development:
- High-Performance Alloys: Introduction of new alloys, including superalloys and titanium alloys, with superior mechanical properties and corrosion resistance.
- Customizable Material Properties: Ability to tailor alloy compositions to meet specific application requirements, improving performance and longevity.
- Process Automation and Control:
- Robotic Systems: Implementation of robotic systems for precise shell coating, mold handling, and metal pouring, ensuring consistent quality.
- Real-Time Monitoring: Advanced monitoring and control systems to detect and correct defects during the casting process, improving yield and reducing waste.
- Quality Control and Inspection Technologies:
- Non-Destructive Testing (NDT): Utilization of X-ray, ultrasonic testing, and CT scanning to inspect internal structures and detect defects without damaging the parts.
- Simulation and Modeling: Use of sophisticated simulation software to model the casting process, predict potential issues, and optimize parameters.
Impact on Precision Manufacturing
The advancements in lost wax casting have a profound impact on precision manufacturing, offering numerous benefits across various industries.
- Improved Component Quality:
- High Dimensional Accuracy: Achieving precise dimensions and intricate details, reducing the need for post-casting machining.
- Superior Surface Finish: Producing components with excellent surface finishes, often eliminating secondary finishing processes.
- Increased Efficiency:
- Reduced Waste: Near-net shape production minimizes material waste and reduces overall costs.
- Faster Production Cycles: Rapid prototyping and automated processes accelerate production timelines.
- Enhanced Durability:
- Stronger Materials: Use of advanced alloys and ceramics results in components with superior strength, toughness, and resistance to wear and corrosion.
- Longer Lifespan: Improved material properties extend the operational lifespan of components, reducing maintenance and replacement costs.
Applications in Various Industries
- Aerospace:
- Turbine Blades and Vanes: Precision casting of high-performance superalloy components capable of withstanding extreme temperatures and stresses.
- Structural Components: Lightweight and durable parts for aircraft frames and engine housings.
- Automotive:
- Engine Parts: Manufacturing of intricate engine components, such as turbocharger housings and pistons, using lightweight and strong alloys.
- Transmission Components: Precision casting of gears and other critical transmission parts for improved performance and longevity.
- Medical:
- Surgical Instruments: Production of highly precise and biocompatible surgical tools and implants.
- Prosthetics: Custom-made prosthetic components with detailed and patient-specific designs.
- Energy:
- Turbine Components: Casting of high-temperature-resistant parts for gas and steam turbines in power generation.
- Oil and Gas Equipment: Durable and reliable components for exploration, drilling, and production operations.
- Industrial Machinery:
- Pump and Valve Components: Production of robust parts capable of withstanding harsh operating conditions in industrial applications.
- Heavy Machinery Parts: Precision casting of components for heavy-duty machinery and equipment.
Table: Comparative Analysis of Advancements in Lost Wax Casting
Innovation | Benefits | Key Applications |
---|---|---|
3D Printing for Wax Patterns | Rapid prototyping, high detail accuracy | Aerospace, automotive, medical |
Advanced Ceramic Shell Materials | Improved mold stability, high-temperature resistance | Energy, industrial machinery |
High-Performance Alloys | Enhanced strength, corrosion resistance | Aerospace, automotive, medical |
Process Automation and Control | Consistent quality, reduced human error | All industries |
Quality Control Technologies | Defect detection, improved reliability | All industries |
Case Study: Advancements in Lost Wax Casting for Medical Implants
Background: A medical device manufacturer aimed to improve the quality and customization of titanium implants used in orthopedic surgery. The goal was to produce implants with superior biocompatibility, precision, and durability.
Approach:
- Material Selection:
- Chose a biocompatible titanium alloy known for its strength, corrosion resistance, and compatibility with the human body.
- Pattern Creation:
- Utilized 3D printing to create detailed wax patterns tailored to patient-specific anatomies.
- Improved wax formulations for better dimensional accuracy and surface finish.
- Ceramic Shell Formation:
- Used advanced ceramic materials to build strong and heat-resistant shells.
- Applied multi-layer shell construction to prevent cracking and deformation during casting.
- Precision Casting:
- Implemented vacuum casting to reduce gas entrapment and improve overall quality.
- Controlled solidification process to achieve optimal grain structure and mechanical properties.
- Quality Control:
- Conducted X-ray and CT scanning to inspect the internal structure of the cast implants.
- Used simulation software to predict and mitigate potential defects.
Results:
- Achieved implants with superior precision and surface finish, reducing the need for post-casting machining.
- Enhanced biocompatibility and mechanical properties, leading to better patient outcomes.
- Customized implants tailored to individual patient anatomies, improving surgical fit and function.
- Lowered production costs and reduced lead times through process automation and improved yield.
Conclusion
Innovative advancements in lost wax casting have revolutionized precision manufacturing, enabling the production of high-quality, durable, and efficient components across various industries. The integration of 3D printing, advanced ceramic materials, high-performance alloys, process automation, and sophisticated quality control techniques has significantly enhanced the capabilities of lost wax casting. These advancements allow manufacturers to meet the stringent demands of modern applications, delivering components that offer superior performance, longevity, and cost-effectiveness. As technology continues to evolve, lost wax casting will play an increasingly critical role in the future of precision manufacturing.