During the casting production process, various defects that affect the performance of castings are prone to occur in cast steel parts. Analyzing the porosity defects encountered in thick and large cast steel parts during production, optimizing the molding process and improving the melting process can effectively reduce the occurrence of porosity, thereby solving the problem of porosity defects in thick and large cast steel parts during production and improving the quality of castings.
During the casting production process, various defects that affect the performance of castings are prone to occur in cast steel parts. Analyzing the porosity defects encountered in thick and large cast steel parts during production, optimizing the molding process and improving the melting process can effectively reduce the occurrence of porosity, thereby solving the problem of porosity defects in thick and large cast steel parts during production and improving the quality of castings.
Thick cast steel parts are essential components in fields such as machinery, chemical engineering, and energy, and their quality stability is crucial. In the production process, quality problems such as porosity and cracks are not uncommon, which not only lead to delayed delivery cycles, but also may shorten the service life of castings and even cause safety accidents. The occurrence of porosity defects often stems from unreasonable molding processes, improper melting processes, and uneven quality of casting materials. By studying the causes of porosity defects in thick and large cast steel parts and proposing preventive measures, the quality of castings can be improved Quantity and performance.
After opening the casting, dense and obvious porosity defects appeared on the outer surface, with smooth inner walls and a surface color of iron oxide. The defect depth was about 20 mm, and the length and width were between 80 and 150 mm. By observing the pore characteristics on the surface of the casting, it is determined that these pores belong to invasive pores. The formation of such pores mainly originates from casting manufacturing Excessive sand consumption during the process, coupled with poor breathability of the sand mold. Due to the relatively thick wall of the casting, the time for the surface layer to crust will be relatively long. In this process, if the gas generated in the sand mold cannot escape from the sand mold or from the interface between the sand mold and the molten steel before the crust is formed, a gas holding phenomenon will form at certain positions, especially at the outer edge near the riser position. Due to gas compression, the shell that is still in a high temperature state is prone to plastic deformation. As the temperature gradually decreases, these plastic deformations will be permanently retained, thereby forming pores., During the casting process, a large amount of gas is generated, especially at the interface between the sand mold and the molten steel, where a series of violent chemical reactions occur.
Under the influence of temperature and pressure differences in the sand mold, although most of the gas can be discharged through channels such as permeable sand molds, risers, exhaust ropes, and air holes, a small amount of gas will still accumulate in certain areas to form pores. Sometimes these gases may even be adsorbed by the molten steel and diffuse into the interior of the casting, forming internal pores. However, from the final processed casting, there were no needle shaped pores formed inside. Therefore, the possibility of gas intrusion into the interior of the casting is ruled out. To address the issue of porosity, it has been decided to upgrade the bottom casting process of Model II castings to a stepped casting process. On this basis, a special inner runner was added to lead up to 150mm from the base of the riser. This design not only significantly reduces the static pressure of the bottom steel, but also effectively introduces the high-temperature steel in the ladle into the open riser, thereby greatly improving the shrinkage capacity of the riser and effectively avoiding the situation where the riser is cold and the casting is hot. To further improve the quality of the castings, an external cooling iron was added to the outer circle to ensure a sand consumption of about 40mm between the external cooling iron and the castings. This measure aims to reduce the total amount of gas generated by the resin curing agent under high temperature conditions. At the same time, the thickness of the cold iron is designed to be 200 mm, which can quickly cool the outer surface of the casting, ensure that it will crust as soon as possible, and effectively prevent gas from entering the interior of the casting or forming pores in local areas. By optimizing the pouring system, adding external cooling iron, improving sand cores and other measures, the efficiency of riser shrinkage can be ensured, reducing gas generation and facilitating exhaust. Furthermore, by optimizing the smelting process, the gas content in the molten steel can be reduced. This series of process improvements and optimizations have successfully solved the problem of porosity in thick cast steel parts during production. Taking two castings as an example, after unboxing, the surface of the castings is smooth and there are no visible porosity defects. After heat treatment and mechanical processing, the surface smoothness of the casting is further improved without any porosity defects, and the finished casting does not require welding or repair. Compared with the previous casting quality, the porosity defects of the casting have been significantly improved.
Through the analysis and research of porosity defects in thick cast steel parts, a series of preventive measures have been proposed, mainly including optimizing the pouring system, adding external cooling iron, improving sand cores, optimizing smelting processes, etc. Through practice, these measures Significant achievements have been made in improving the porosity defects and enhancing the quality of castings.
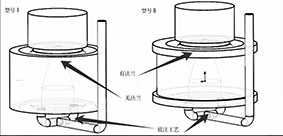