The metal pressure vessel industry involves technologies such as casting, forging, welding, heat treatment, and surface treatment. The production process is complex, with a high degree of technical integration, and it often operates for a long time in environments such as high temperature, high pressure, and corrosion. The media involved are often flammable, explosive, highly toxic, and harmful substances, which require high reliability, stability, safety, and operational effectiveness of the product. In addition, metal pressure vessel products are usually non standardized and are usually tailored by manufacturers based on the technical parameters provided by customers. Low pressure casting technology The obtained castings have good overall structural integrity, high reliability, light weight, and low processing costs, making them suitable for casting pressure vessel related parts. The working environment of aluminum alloy sleeves used for pressure vessels is special, with extremely high requirements for the hardness, tensile strength, and airtightness of the parts themselves. Therefore, the author conducted research on aluminum alloy sleeves used for pressure vessels and used Flow-3D Casting software to simulate the casting process, in order to predict and eliminate possible defects in production through simulation, obtain the optimal low-pressure casting process plan, effectively improve the process yield of parts, and provide reference for the process design of aluminum alloy casting sleeves.
The pouring temperature of the sleeve is 710 ℃, using sand mold low-pressure casting based on drying and scrubbing sand. The initial temperature of the mold is 200 ℃, and the material is A356. A356 is one of the most common die cast alloys with excellent casting, mechanical, and physical properties, widely used in various fields such as aluminum alloy wheels, engine parts, and chassis for automotive components. However, due to its shrinkage during solidification and easy dissolution of hydrogen in the molten state, it inevitably contains a certain number of casting defects, such as pores and non-metallic inclusions. The casting technology requires that there should be no casting defects such as porosity and shrinkage. Using low-pressure casting method, the castings are subjected to shot peening, heat treatment, and mechanical processing after completion. Simultaneously complete the testing of chemical composition, mechanical properties, appearance, material quality, and dimensions. Finally, conduct water pressure test, air tightness test, and water pressure failure test.
Casting pouring system and distribution of cold iron. Set up a top pouring system according to the principle of sequential solidification, and design the inner runner to be evenly distributed on the thick wall of the casting, so that each part of the casting is cooled evenly and the stress is low. The flange position of the sleeve is 38 mm thick, the middle of the sleeve is 12 mm thick, and the top of the sleeve is 16 mm thick, and it belongs to the final filling position. Therefore, installing cold iron at the top of the flange and sleeve can effectively ensure the quality of the casting product. Low pressure casting is a molding process that combines the filling principle of anti gravity casting with the crystallization principle of castings under pressure conditions.
Conclusion
Analyze the structure and production requirements of the sleeve, design the pouring system, propose three casting process schemes, and calculate the pressure curve for each scheme. After simulating three different process schemes and comparing them, the following conclusions were drawn:
(1) Analyzing the flow state of molten metal in different process schemes, it was found that casting defects such as curling and turbulence are prone to occur at the pouring channel and flange positions inside the sleeve. The reason for this is that the filling pressure is high and the flow rate of the metal liquid is too fast.
(2) During the filling process of Plan 3, the gas entrapment disappears, the turbulence weakens, the liquid level rises steadily, the amount of oxide slag produced decreases, the temperature distribution gradient is small, and the solidification sequence of the castings is reasonable. This is the optimal plan, which can effectively reduce the possible casting defects that may occur in the actual production process.
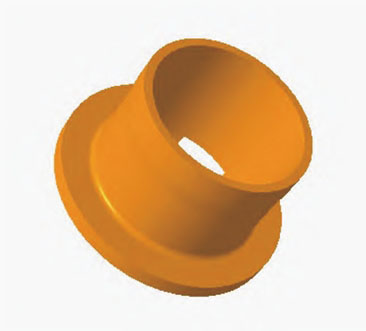
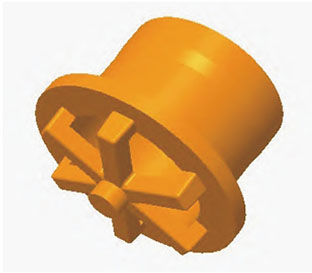
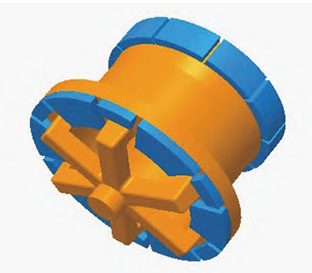