This paper focuses on the casting process of spiral series thick and large ductile iron castings to address the issues of shrinkage porosity and slag defects. By optimizing the cold iron and riser processes and adopting the bottom pouring gating system, the quality of the castings is significantly improved. The experimental results show that this approach can effectively solve the problems of shrinkage porosity and slag defects in spiral products.
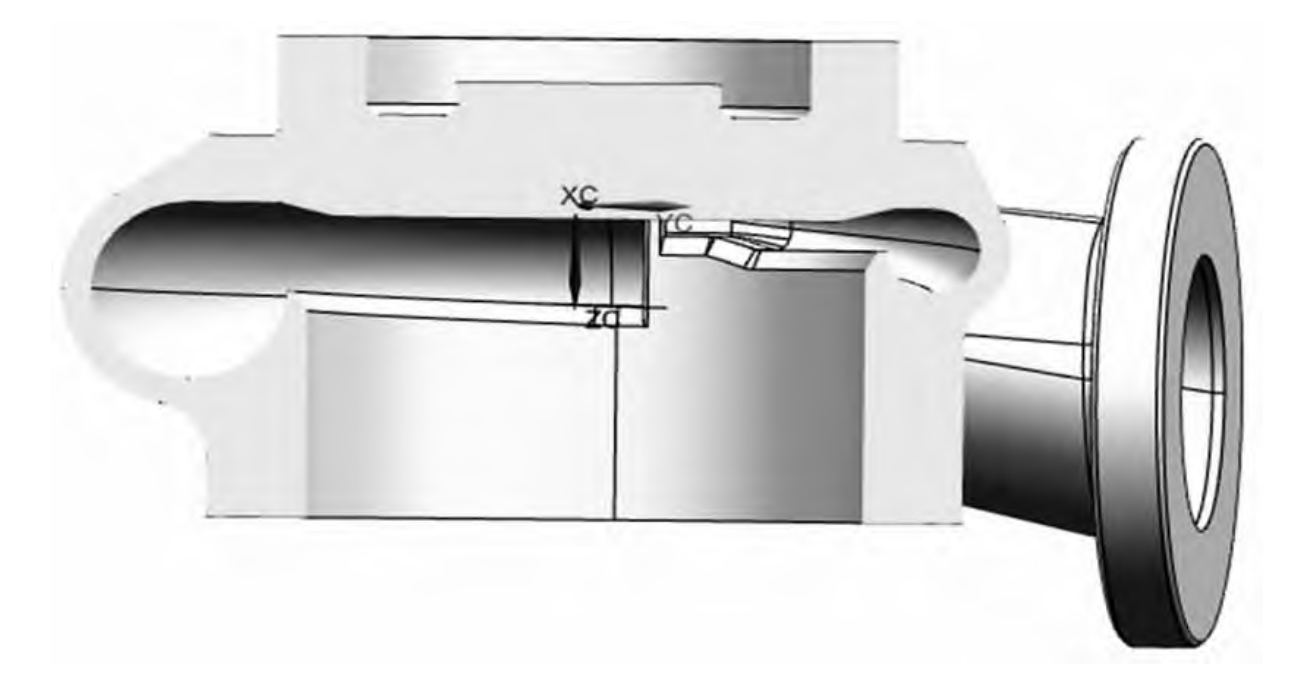
Introduction:
Spiral series products are a kind of small-batch and multi-model series products, with various types and weights ranging from 500 to 2000 kg. They are thick and large ductile iron castings, with the main wall thickness of 20 mm and the maximum wall thickness of 100 mm. The uneven distribution of the wall thickness and the complex distribution of the hot spots make the casting process quite challenging. The castings are required to have no visible casting defects after processing, which further adds to the difficulty of the casting process.
Experimental Scheme:
The outline dimensions of the spiral series products are 1450 mm × 850 mm × 380 mm, and the weight is 200 – 1500 kg. The material is QT400 – 18 – LT, and the castings are required to undergo UT (according to DIN EN 12680 – 1 Grade 1) and MT (according to DIN EN 1369 Grade SM 3) flaw detections. There should be no visible appearance defects after processing. To solve the shrinkage porosity and slag defects of the spiral, a bottom pouring process scheme using cold iron and riser is adopted.
Results and Analysis:
- Optimization of Process Design to Simplify Molding and Reduce Cost:
- A unified gating system is used for different models of spirals within the weight range of 200 – 1500 kg, which not only reduces the number of molds and the cost of mold making but also simplifies the molding operation and avoids frequent switching of the gating system.
- To reduce the cost of molding, the gating system and the outer mold are designed as movable structures, so that a smaller sand box can be selected by adjusting the positions of the gating system and the outer mold, reducing the amount of sand consumed.
- Optimization of Mold Structure to Reduce Mold Cost:
- The mold structure includes metal mold structure, steel – wood structure, and wood mold structure. The wood mold structure with the lowest cost is adopted for this series of products.
- A non – plate outer mold is used, which is expected to save 50% of the mold cost compared to the outer mold with a plate. The molding steps of the non – plate outer mold are as follows: place the solid pattern and the expansion movable block on the tire mold – place the solid pattern, the expansion movable block, and the tire mold as a whole on the molding plate – place the sand box and fill it with sand to make the lower mold – after the lower mold solidifies, turn it over – take out the tire mold – sprinkle the parting dry sand with a particle size of 100 – 140 mesh on the parting surface – place the sand box and fill it with sand to make the upper mold – after the upper mold solidifies, demold to obtain the cover box – take out the solid pattern and the expansion movable block – demold to obtain the bottom box.
- The mold is divided into a basic mold pattern and an expansion mold movable block. When borrowing the mold, only the expansion mold movable block needs to be replaced without making a new basic mold, which greatly reduces the cost of mold making.
- Optimization of Casting Process to Solve the Inclusion Problem of the Spiral:
- To control the source of inclusions and improve the purity of the molten iron, the following measures are taken: control the time from tapping to pouring within 10 minutes to prevent inoculation decay and reduce the generation of oxidized slag; place a piece of asbestos on the surface of the molten iron in the pouring ladle before pouring to absorb the oxidized slag on the surface of the molten iron and reduce the slag in the pouring ladle entering the pouring basin; place a filter sheet in front of the inner gate to filter and block the slag of the molten iron entering the cavity. The specification of the filter sheet is 150 × 150 × 20, and the number is 2 pieces.
- To reduce the impact of inclusions, the following measures are taken: clean and polish the local loose sand or sharp – cornered sand in the cavity before closing the box to avoid being brought into the molten iron during pouring; use a ceramic tube for the inner gate to reduce the risk of the sand in the gate being brought into the cavity during pouring; adopt a bottom pouring gating system, so that the molten iron flushes smoothly from bottom to top, and even if there is oxidized slag in the molten iron or loose sand in the cavity, it is easy to float up and be discharged through the overflow of the riser vent.
- Optimization of Casting Process to Solve the Dispersed Shrinkage Porosity Problem at Local Positions of the Spiral:
- To reduce or eliminate the shrinkage porosity defect of the casting, risers and cold irons are placed at the hot spots of the casting. Specifically, insulation risers are added to the thick parts on the cover box surface of the casting to supplement the shrinkage of the thick parts. There are 4 insulation risers on the top circular platform, with the size of ø200 mm × 200 mm and the riser neck size of ø100 mm × 50 mm. There is 1 insulation riser on the top surface of the flange, with the size of ø100 mm × 100 mm and the riser neck size of ø50 mm × 20 mm.
- Cold irons are placed at the hot spots and important processing positions of the casting to quench the casting and reduce the tendency of shrinkage porosity.
- A low – temperature open pouring scheme is adopted. The cross – section of the inner gate is 4 × ø40 mm, the cross – section of the horizontal runner is 2 × (40 / 50) mm × 40 mm, the cross – section of the vertical runner is 660 mm, and the pouring temperature is 1330 ± 10 °C.
- Verification of the Spiral Process:
- The bottom pouring casting process optimized with cold iron and riser effectively reduces the porosity tendency of the casting. Through the solidification simulation of the shrinkage porosity distribution, it is found that the hot spots of the casting are widely and dispersedly distributed, and the shrinkage porosity rate of the casting is controlled at about 1%.
- A total of three batches of experiments, namely “1 + 2 + 4”, are conducted, and the MT and UT flaw detections of the experimental pieces meet the technical requirements of the customers. There are no visible casting defects on the appearance of the experimental pieces after processing.
- In actual production, this process has been solidified and mass production has been realized. Using this casting process scheme, more than 150 similar – structured castings of 35 types have been produced, and the quality of the castings is stable and has been delivered as finished products.
Conclusion:
- The optimized bottom pouring process scheme with cold iron and riser can largely solve the problems of shrinkage porosity and slag defects in the spiral.
- The combination process scheme of riser and cold iron is beneficial to reducing the shrinkage porosity tendency of the casting.
- Controlling the purity of the molten iron and the cleanliness of the cavity can largely solve the problem of slag defects in the casting.
In order to further illustrate the experimental results, a table is provided below:
Experimental Parameter | Value |
---|---|
Weight Range of Spiral | 200 – 1500 kg |
Material | QT400 – 18 – LT |
Flaw Detection Requirements | UT (according to DIN EN 12680 – 1 Grade 1) and MT (according to DIN EN 1369 Grade SM 3) |
Gating System | Unified for different models within the weight range |
Mold Structure | Wood mold structure, non – plate outer mold, divided into basic mold pattern and expansion mold movable block |
Measures to Control Inclusions | Control the time from tapping to pouring within 10 minutes, place asbestos on the surface of the molten iron in the pouring ladle, place a filter sheet in front of the inner gate, clean and polish the local loose sand in the cavity, use a ceramic tube for the inner gate, adopt a bottom pouring gating system |
Measures to Reduce Shrinkage Porosity | Add insulation risers to the thick parts, place cold irons at the hot spots and important processing positions, adopt a low – temperature open pouring scheme |
Shrinkage Porosity Rate | About 1% |
This research provides valuable insights into the casting process of spiral series thick and large ductile iron castings, and the optimized process scheme can be applied to improve the quality and reliability of similar castings. Further studies can be conducted to explore the optimization of the process parameters and the application of new technologies to meet the increasing demands of the industry.