Abstract
Heat-resistant cast aluminum alloys have been extensively applied in high-temperature and high-stress environments, particularly in the cylinder heads of diesel engines. With the escalating demands for increased engine power and fuel economy, there is a pressing need for alloys with enhanced high-temperature resistance and fatigue resistance. This paper commences by reviewing the conventional strengthening phases utilized in the design of heat-resistant cast aluminum alloys. Subsequently, the criteria for heat-resistant precipitate design and newly recognized heat-resistant phase structures are summarized. Furthermore, a brief introduction to newly developed aluminum-based eutectic alloys for elevated temperature applications is provided. Finally, the future development of heat-resistant cast aluminum alloys is discussed, incorporating insights from advanced heat-resistant aluminum cast alloys that have already found applications.
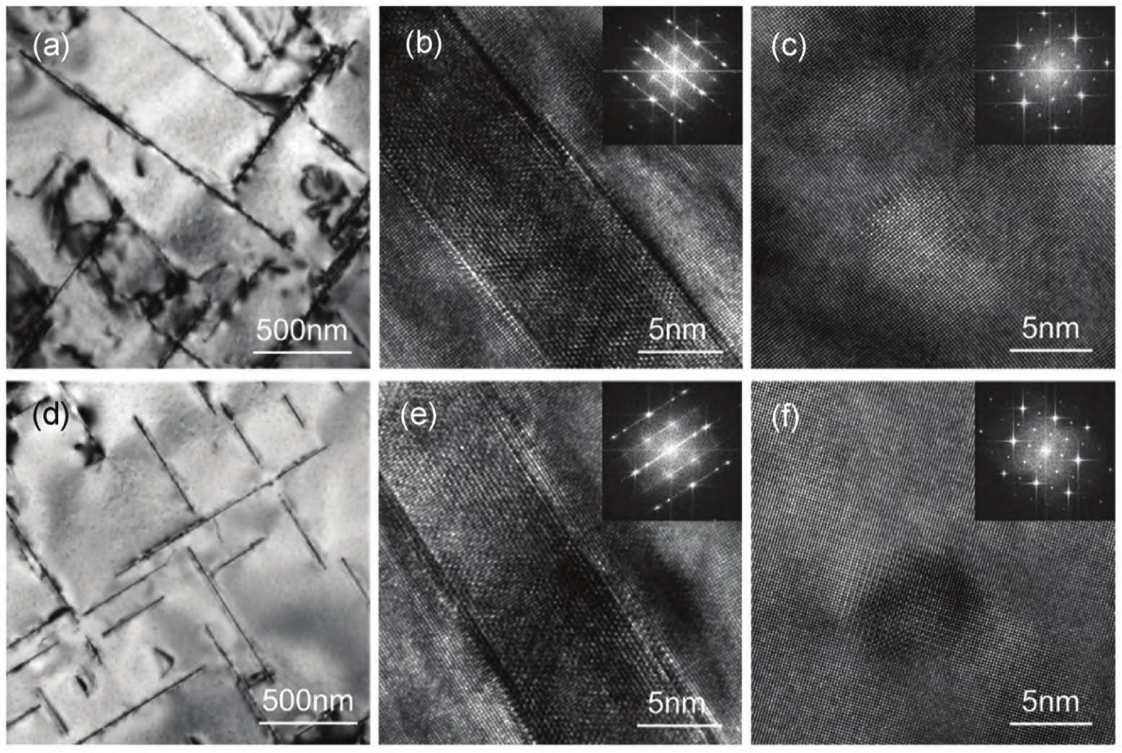
1. Introduction
Aluminum alloys have garnered significant attention in the automotive and aerospace industries due to their low density, high specific strength, and excellent corrosion resistance. Heat-resistant cast aluminum alloys, specifically, play a pivotal role in high-temperature applications, where they are subjected to extreme temperatures and mechanical stresses. This paper delves into the current status and prospects of research and applications of these alloys, highlighting recent advancements and future directions.
2. Conventional Strengthening Phases in Heat-Resistant Cast Aluminum Alloys
2.1 Al-Si and Al-Cu Based Alloys
Al-Si and Al-Cu alloys are the two primary systems utilized in the development of heat-resistant cast aluminum alloys.
2.1.1 Al-Si Alloys
Al-Si alloys exhibit excellent casting performance and are commonly reinforced with elements such as Mg and Cu to form heat-resistant phases. The addition of Mg results in the formation of Mg2Si phases, which, upon heat treatment, precipitate as fine β’ and β” phases, enhancing room-temperature strength. However, these phases have limited thermal stability, with a rapid coarsening above 185°C, limiting their applicability to temperatures below this threshold.
2.1.2 Al-Cu Alloys
Al-Cu alloys, on the other hand, form θ’ and θ” phases upon aging, which are thermally stable up to 225°C. When combined with Mg, these alloys exhibit complex strengthening phases such as Q’ (Al5Mg8Si6Cu2), enhancing their high-temperature performance. However, even these phases coarsen above 250°C, necessitating the development of alloys with higher thermal stability.
2.2 Comparison of Conventional Alloys
Table 1 provides a comparative overview of the composition, heat resistance, and typical applications of several conventional heat-resistant cast aluminum alloys.
Alloy | Composition (wt%) | Heat Resistance (°C) | Typical Application |
---|---|---|---|
A356 | Al (balance), Si 6.65, Cu 0.05, Mg 0.35 | ≤185 | Cylinder head |
AS7GU | Al (balance), Si 7.04, Cu 0.48, Mg 0.36 | ≤250 | Cylinder head |
ZL702A | Al (balance), Si 6.0-8.0, Cu 1.3-1.8, Mg 0.3-0.5 | ≤250 | Cylinder head |
W319 | Al (balance), Si 7.43, Cu 3.33, Mg 0.22 | ≤250 | Cylinder head |
ZL205A | Al (balance), Cu 1.87, Mg 0.36, Ni 0.5-1.2 | ≤250 | Cylinder block |
M142 | Al (balance), Si 0.15, Cu 4.6-5.3, Ni 2.5-4, Mg 0.3-0.5 | 250-350 | Cylinder head |
3. Advanced Heat-Resistant Phases and Alloy Design
3.1 Microalloying and High-Temperature Strengthening Phases
Recent research has focused on microalloying with elements such as Zr, Er, Sc, Mn, Mo, Cr, and V to form high-temperature strengthening phases. These elements contribute to the formation of precipitates like Al3M (M = Zr, Sc, Er, V, etc.) or α-Al(Mn, Cr, Fe)Si dispersions, enhancing the thermal stability of alloys.
3.1.1 Al3Sc and Core-Shell Nanostructures
Alloys microalloyed with Sc exhibit outstanding thermal stability due to the formation of Al3Sc precipitates. Core-shell nanostructures, with Sc at the core surrounded by slower-diffusing elements like Er and Zr, have been developed to further enhance stability, reaching temperatures exceeding 400°C [1].
3.1.2 θ’ Phase Stabilization
The θ’ phase in Al-Cu alloys has been stabilized through microalloying with Mn and Zr, which segregate at θ’/α-Al interfaces, inhibiting phase coarsening [2]. This strategy has enabled the application of Al-Cu alloys in environments exceeding 300°C.
3.2 Novel Alloy Systems
To overcome the limitations of conventional alloys, novel alloy systems have been developed, including Al-Ni, Al-Ce, and their transition metal (TM) modified variants.
3.2.1 Al-Ni and Al-Ni-TM Alloys
Al-Ni alloys exhibit exceptional casting performance and high thermal stability due to the formation of the Al3Ni eutectic phase. The addition of Zr and Cr further enhances their high-temperature strength and creep resistance [3].
3.2.2 Al-Ce and Al-Ce-TM Alloys
Al-Ce alloys, particularly those near the eutectic composition, form a high volume fraction of fine Al11Ce3 precipitates, imparting high strength without the need for heat treatment. The addition of Mg, Cu, and Fe further improves the mechanical properties of these alloys [4].
4. Advanced Heat Treatment Techniques
Heat treatment plays a crucial role in precipitate formation and stabilization in heat-resistant cast aluminum alloys. Recent advancements include regression and re-aging (RRA) processes, which significantly enhance the thermal stability and creep resistance of Al-Cu-Sc alloys [5].
4.1 Regression and Re-Aging (RRA)
The RRA process involves an initial aging step, followed by a regression treatment at a higher temperature to dissolve metastable precipitates, and a final re-aging step to reprecipitate finer, more thermally stable phases. This process has been successful in co-stabilizing θ’ and Al3Sc precipitates, enabling alloys to perform at temperatures exceeding 300°C [6].
5. Applications and Commercial Alloys
Several commercial alloys have been developed based on the advancements discussed above. One such example is the ACMZ (Al-Cu-Mn-Zr) alloy developed by Nemak and applied in the Hyper200 engine cylinder head by AVL. This alloy, marketed as NemAlloy HT200, exhibits significantly enhanced high-temperature strength compared to conventional Al-Si-Cu alloys [7].
6. Future Directions and Prospects
The development of heat-resistant cast aluminum alloys continues to evolve, driven by advancements in alloy design, microalloying strategies, and heat treatment techniques. Future research should focus on:
- Microstructural Engineering: Utilizing advanced characterization techniques like atom probe tomography (APT) and transmission electron microscopy (TEM) to gain a deeper understanding of precipitate formation and evolution.
- Computational Materials Science: Employing first-principles calculations, CALPHAD (Calculation of Phase Diagrams), and machine learning to accelerate alloy development and optimize microstructural features.
- Multiscale Modeling: Integrating atomistic, mesoscale, and continuum-scale models to better predict alloy behavior under complex service conditions.
- Sustainability and Cost-Effectiveness: Developing alloys with reduced environmental impact and lower production costs, ensuring their widespread adoption.
- In-Service Performance: Assessing the long-term performance of advanced alloys under actual service conditions, including creep, fatigue, and corrosion resistance.
7. Conclusion
Heat-resistant cast aluminum alloys have witnessed significant advancements in recent years, with the development of novel strengthening phases, alloy systems, and heat treatment techniques. These advancements have paved the way for their application in increasingly demanding high-temperature environments. As research continues to progress, the potential for heat-resistant cast aluminum alloys to replace heavier materials like titanium and steel in critical components remains immense.