Abstract
In the context of rapid technological advancements and increased productivity demands, the quality requirements for castings have become increasingly stringent. This paper focuses on the optimization of the casting process for diesel engine intermediates, a crucial component in the marine industry. The study analyzes the current quality issues faced by the manufacturing process and proposes a series of improvements to the casting process. By refining the molding process, melting techniques, and implementing stringent quality control measures during production, significant improvements in casting quality have been achieved. The optimized process effectively reduces defects and enhances the overall quality of the diesel engine intermediates, meeting the stringent technical requirements of modern applications.
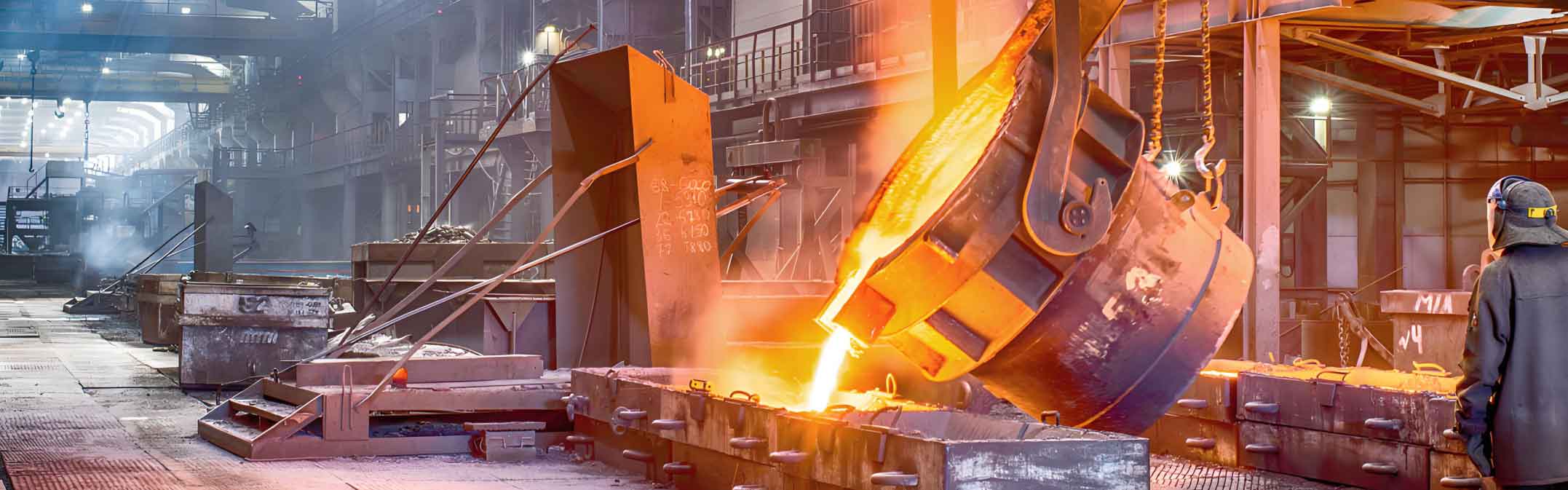
1. Introduction
With the continuous development of science and technology and the improvement of productivity levels, the quality requirements for castings have become increasingly demanding. In particular, the rapid development of the shipbuilding industry in China necessitates localized production of marine diesel engines to meet the actual needs of shipbuilding. As a result, the size of diesel engines produced by companies has increased, leading to an increase in the weight and casting difficulty of diesel engine intermediates. This, in turn, has placed higher and stricter requirements on the quality of castings and the detection of defects in intermediate castings. Traditional casting quality standards have gradually become inadequate for current and future needs.
This paper analyzes the quality issues of large diesel engine intermediates produced by the author’s company, with a particular focus on defects that occur after processing. The study investigates the causes of these defects and proposes an optimized design for the casting process of diesel engine intermediates. Through improvements to the molding process and melting process, combined with quality control during the operation, the quality of castings produced through several process optimization experiments was compared. The results demonstrate significant improvements in the quality of intermediates, validating the effectiveness of the process improvements and ensuring compliance with technical requirements.
2. Quality Issues of Intermediates
In recent years, the quality issues of large diesel engine intermediates produced by the author’s company have been severe, mainly manifested by defects that emerge after processing, necessitating frequent repairs. These defects not only cause delays in product delivery but also tarnish the company’s reputation.
After investigation and analysis, the quality issues of intermediates primarily include:
- Defects in Bearing Hole Positions: For large models (60 and above), the number of defects in the bearing hole positions after rough and finish machining is significant, while smaller models are basically defect-free. Analysis of non-conforming product records over the past two years revealed that the Flex60MC-C rear main intermediate accounts for 78.5% of non-conforming intermediates, with the primary defects occurring in the bearing hole positions. The magnetic particle inspection reveals an increasing number of magnetic indications (mainly 3-5 mm long), accompanied by casting defects such as porosity, inclusions, and slag.
- Shrinkage Defects: Shrinkage porosity and shrinkage cavities frequently occur at the intersection of the reinforcing ribs on both sides of the rear end of the intermediate and below the center riser at the rear end.
- Welding Quality Issues: Poor welding quality often leaves welding defects. The welded reinforcing ribs have significant dimensional deviations, necessitating frequent overlay welding for correction.
- Surface Quality Issues: The casting surface often exhibits defects such as sand holes, slag inclusions, steel-sand inclusions, porosity, watermarks, and shrinkage porosity/cavities at the riser root.
- Dimensional Offset of Reinforcing Ribs: After rough machining and marking, significant dimensional offsets in the reinforcing ribs of intermediate blanks are observed, all in one direction.
3. Current Status of Defects
There are numerous reasons for casting defects, with imperfections in the casting process and operational management being the primary factors. Other contributing factors include production constraints and heightened quality requirements for castings.
4. Analysis of Defect Causes
Shrinkage Defects: Shrinkage porosity and shrinkage cavities frequently occur at the rounded corners near the intersection of the reinforcing ribs on both sides of the rear end of the intermediate. This is attributed to inadequate insulation of the risers or undersized risers that fail to meet the actual feeding requirements of the casting.During riser design, to facilitate cleaning, the riser center is offset from the hot spot center, and the chill iron below the riser fails to achieve its intended chilling effect, resulting in poor feeding performance.The middle waist-shaped open riser may not provide sufficient feeding. Its center is located at the machining area of the bearing hole surface, with the area below the riser center being the most susceptible to defects.
Poor riser quality is also a significant factor. After pouring and solidification of the rear main intermediate, the used microbead insulation risers revealed that their shrinkage was comparable to that of sand-type risers. This indicates poor quality of the microbead insulation risers, with their actual modulus being much smaller than the standard modulus they should achieve. This directly affects the final solidification and contraction of the casting. Since the riser above the bearing hole is the last to solidify, inadequate riser performance can easily lead to shrinkage porosity at the bottom of the riser.
Inadequate Feeding of the Bearing Hole Area: The bearing hole area of the intermediate undergoes prolonged high-temperature conditions during the mold filling and solidification processes, making the solidification and crystallization in this area complex. It is also the area where various oxides, inclusions, and gases in the molten steel finally gather, leading to a high susceptibility to defects.