1. Introduction
Steel casting plays a crucial role in various industrial fields due to its excellent mechanical properties. However, the issue of pore defects is prevalent, posing a significant threat to the overall quality and subsequent application safety of steel castings. This article focuses on analyzing the formation mechanism of pore defects in steel casting, conducting case studies on defect inspection, researching control technologies, and proposing process improvement schemes to enhance casting quality.

2. Formation Mechanism of Pore Defects in Steel Casting
2.1 Dissolution and Precipitation of Gas in Steel
During the steel casting process, the formation of pores is closely related to the solubility and precipitation behavior of gases in the molten steel. In the melting process, the molten steel absorbs gases such as hydrogen and nitrogen. As the steel cools, the solubility of these gases decreases, potentially leading to gas precipitation. If the absorbed gases cannot be effectively expelled during cooling, pores will form inside the casting.
2.2 Nucleation and Growth Mechanism of Pores
Pore formation in steel casting involves two key stages: nucleation and growth. Nucleation typically occurs in the solid-liquid two-phase coexistence region, such as between dendrites or at columnar grain boundaries. Gas atoms aggregate in these regions to form stable bubble nuclei. Once the nuclei are formed, they gradually absorb more gas atoms in the molten steel and grow larger. The final size and distribution of pores depend on factors such as the nucleation position, number, cooling rate, and gas content in the molten steel.
3. Case Analysis of Pore Defect Inspection in Steel Casting
3.1 Production Environment and Sample Preparation of Steel Castings
Taking a certain instrument company’s steel casting production as an example, they adopt a medium-temperature wax-silica sol casting process, using zircon sand/powder and mullite sand/powder as transition and reinforcement layer materials, and silica sol as the binder. During shell baking, the melting temperature reaches 1150 °C, and medium-frequency furnace melting is used. Field investigations of 720 defective products reveal that most are caused by pores, indicating that pore defects are the main quality issue. Samples are prepared by transverse sectioning with a grinding wheel cutter, grinding with 180 and 320 grit water sandpaper, mechanical polishing with aluminum oxide suspension, erosion in hydrochloric acid aqueous solution, rinsing, wiping, drying, and then subjected to dye penetrant testing.
3.2 Defect Results and Analysis of Steel Castings
After testing 90 samples, it is found that 68 have invasive pore defects (75.6%), 13 have entrained pore defects (14.4%), and 9 have precipitated pore defects (10%). Statistics of 720 defective products on-site show that invasive pore defects account for 86.8% of the total number of defective products, while entrained pores and slag pores account for 9.3% and 3.9% respectively. Invasive pores mainly result from the precipitation of gases in the molten steel during solidification. When the hydrogen content in the molten steel exceeds a certain critical value, hydrogen pores will form during solidification. Additionally, if the nitrogen content in the steel is below 0.02% and exists in a stable nitride form, it can reduce the formation of nitrogen pores. Although entrained and precipitated pores exist, their proportions in investment cast steel parts are relatively small. However, their impacts cannot be ignored. Entrained pores are mainly caused by turbulence during pouring, while precipitated pores are related to alloy composition and cooling rate. Therefore, the focus should be on understanding the formation mechanism and prevention measures of invasive pores.
4. Research on Pore Defect Control Technologies in Steel Casting
4.1 Metal Liquid Treatment Technology
4.1.1 Vacuum Degassing Method
The vacuum degassing method reduces the gas content in the metal liquid by creating a vacuum environment. According to Henry’s law, the solubility of gases is proportional to pressure. In a vacuum, the solubility of gases significantly decreases, facilitating gas precipitation. Setting the vacuum degree to 50 Pa and maintaining it for 15 minutes can effectively remove most of the gases in the metal, minimizing pore formation.
4.1.2 Alkaline Melting Technology
Adding an appropriate amount of alkaline substances, such as limestone and fluorite, during steel casting can neutralize acidic oxides in the metal liquid, reducing gas generation. Alkaline melting also alters the viscosity and surface tension of the metal liquid, facilitating gas removal. Generally, adding 5% limestone can reduce the sulfur content in the steel casting metal liquid by nearly 40%, thereby reducing the number of pores.
4.1.3 Ultrasonic Treatment Technology
Ultrasonic treatment generates tiny bubbles in the metal liquid, which serve as nucleation sites for gas aggregation and expulsion. In practical applications, adjusting the ultrasonic frequency and power can control the size and number of bubbles. For example, using an ultrasonic frequency of 20 kHz and a power of 500 W can reduce the number of pores in the metal liquid by 50%.
4.2 Control of Casting Temperature and Speed
4.2.1 Casting Temperature Selection
The casting temperature is calculated using the formula T=Tliquidus-ΔT, where T is the casting temperature, Tliquidus is the liquidus temperature of the metal liquid, and ΔT is the temperature drop determined by the size and complexity of the casting. For large castings, ΔT is typically set between 30 and 50 °C.
4.2.2 Casting Speed Control
The casting speed is calculated using the formula v=A•ρ•g/μ, where A is the gate cross-sectional area, ρ is the density of the metal liquid, g is the acceleration due to gravity, and μ is the viscosity of the metal liquid. Adjusting the gate size and controlling the casting process can effectively control the casting speed. However, it is necessary to make fine adjustments according to the specific characteristics of the casting.
4.3 Mold Design and Manufacturing Technology
4.3.1 Mold Material Selection
Selecting high-strength, high-thermal conductivity alloy steel materials for molds can enhance their thermal fatigue resistance and stability at high temperatures, reducing the probability of pore formation due to mold deformation.
4.3.2 Mold Structure Design
Utilizing computer-aided design technology to precisely calculate and simulate the internal structure of the mold, adjusting the layout and size of the internal cooling channels can accurately control the temperature field during casting solidification. Additionally, introducing a gas-assisted exhaust system with micro-exhaust holes in the mold can effectively expel internal gases and reduce pore defects.
4.3.3 High-Precision CNC Machining Technology
Adopting high-precision CNC machining technology optimizes the cutting parameters during mold processing, enabling precise control of the mold surface roughness. When the mold surface roughness is below 0.8 μm, the internal pore defects of the casting can be significantly reduced.
4.3.4 Mold Maintenance and Exhaust and Cooling System Design
Implementing a strict maintenance regime for molds, including regular cleaning, inspection, and repair, ensures their good working condition. The design of the mold exhaust system, considering factors such as casting shape, size, and gas generation amount, calculates the exhaust groove size using the formula A1=V•n/v1. The design of the cooling system, with the cooling channel diameter calculated using the formula ,
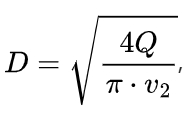
can control the solidification rate of the metal liquid and reduce pore formation. Selecting mold materials with high thermal conductivity and low thermal expansion coefficients, such as aluminum alloy, can also help reduce pore formation.
4.4 Mold Spraying Technology
4.4.1 Selection of Spraying Materials
Choosing spraying materials with good thermal insulation and moderate permeability, such as zircon powder with low thermal conductivity, can significantly reduce heat exchange between the metal liquid and the mold, decreasing gas solubility.
4.4.2 Precise Control of Spraying Thickness
The spraying thickness δ is calculated using the formula δ=Q1/A1•ρ1. Setting the spraying machine parameters based on the calculation results ensures the spraying thickness meets the requirements, preventing direct contact between the metal liquid and the mold.
4.4.3 Optimization of Spraying Process
Adopting a uniform spraying technique to ensure consistent coating thickness avoids problems caused by local thickness variations.
5. Research on Process Improvement Schemes for Pore Defects in Steel Casting
5.1 Application of Advanced Melting Technologies
5.1.1 Vacuum Melting Technology
Melting metal in a vacuum environment can minimize the solubility of gases such as oxygen and nitrogen. Controlling the vacuum degree below 10 Pa and maintaining it for a certain period effectively removes most gases from the metal liquid.
5.1.2 Electromagnetic Stirring Technology
During the melting process, electromagnetic stirring promotes the uniform distribution and removal of gases in the metal liquid, preventing the formation of pores due to high local gas concentrations. Adjusting the magnetic field strength and frequency precisely controls the metal flow state.
5.2 Optimization of Pouring and Solidification Processes
5.2.1 Low-Pressure Pouring Method
Adopting the low-pressure pouring method controls the flow rate of the metal liquid and selects an appropriate filling pattern. Precise control of the pouring pressure and speed, within the range of 0.3 – 0.5 standard atmospheres and 50 – 100 mm/s respectively, prevents turbulence and splashing, reducing gas entrainment.
5.2.2 Optimization of Pouring System Design
Introducing computer simulation technology, such as fluid dynamics analysis of the pouring process using simulation software, optimizes the positions and sizes of the gate and riser, predicting and improving the flow path of the metal liquid in the cavity to avoid gas retention caused by dead ends or unreasonable flow.
6. Conclusion
The control and process improvement of pore defects in steel casting are essential for enhancing casting quality. Through theoretical analysis and case studies, a comprehensive treatment plan is proposed, including metal liquid treatment, control of casting temperature and speed, combined with advanced melting technologies and new casting processes, which can effectively reduce the occurrence of pore defects.