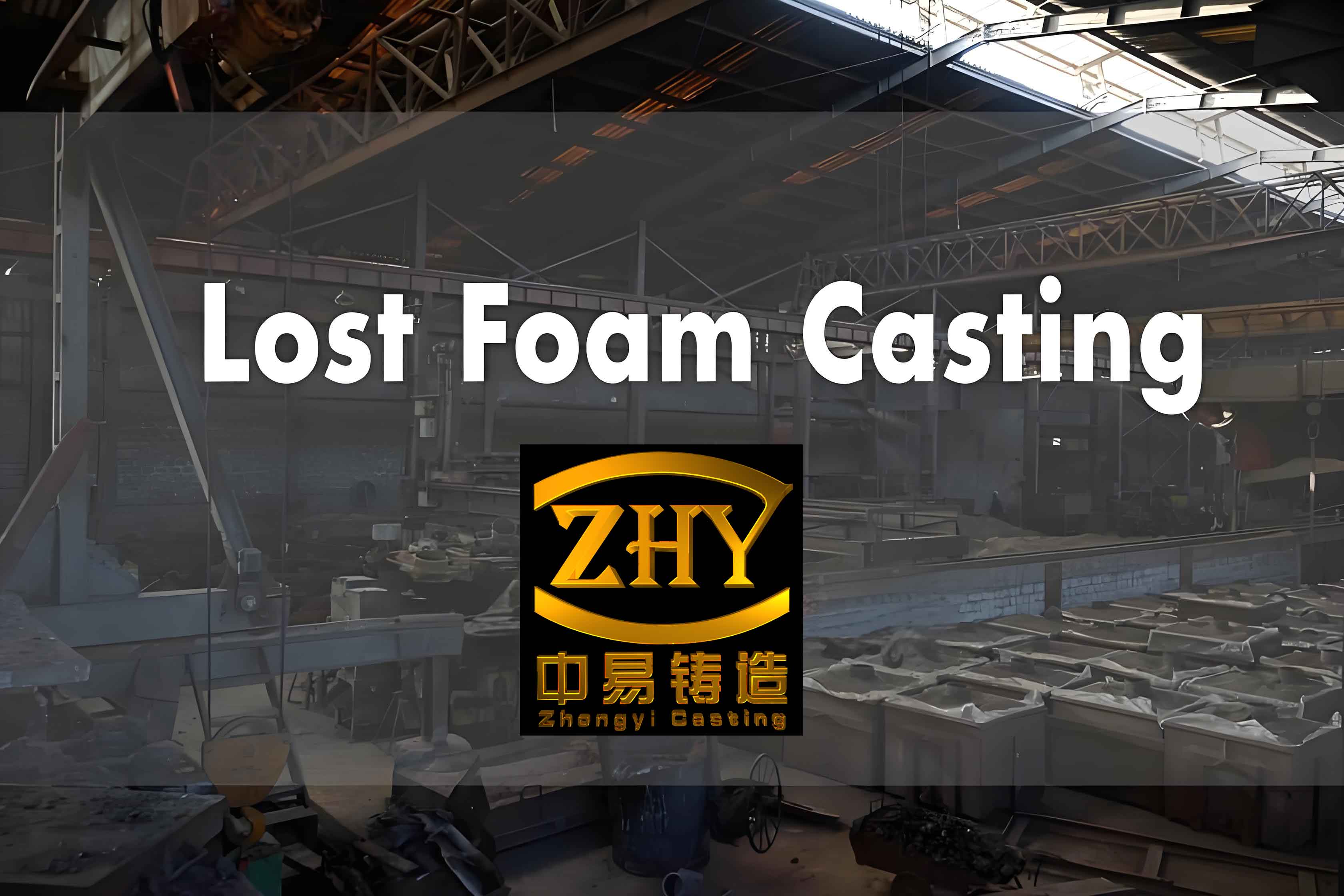
1. Introduction
Lost foam casting technology has developed rapidly in recent years due to its advantages such as low pollution, flexible processing, low labor intensity, and good repeatability. However, in the production of shell products, casting defects such as sand burning, porosity, and sand washing often occur. This article analyzes the causes of these defects and proposes corresponding improvement measures.
2. Analysis and Improvement of Sand Burning Defects in Flywheel Housing Castings
2.1 Defect Appearance and Influence
Sand burning defects are manifested as a mechanical mixture of sand grains and metal adhering to the surface of the casting, with a metallic luster on the surface during cleaning. This defect mainly affects the appearance and quality of the casting.
2.2 Cause Analysis
- Insufficient Sand Filling: The unreasonable placement of the flywheel housing casting and the unreasonable structure or process design result in the inability to compact the mold cluster in the sand box, causing sand burning defects.
- Weak Sand Strength: The small gap between the two flywheel housings leads to weak sand strength.
2.3 Improvement Measures and Results
- Adjust the Placement of the White Mold: Place the motor hole of the flywheel housing upward to facilitate sand filling and ensure sufficient sand at the top of the flywheel housing.
- Increase the Distance between the Two Flywheel Housings: Increase the distance between the two flywheel housings from 80mm to 120mm to ensure the compactness of the sand.
After implementing the above measures, the sand burning defect was completely eliminated, as shown in the following table:
Before Improvement | After Improvement |
---|---|
Sand burning defect at the top of the flywheel housing cavity, with a scrap ratio of 20% | Zero sand burning defect |
3. Analysis and Improvement of Porosity Defects in Flywheel Housing Castings
3.1 Defect Appearance and Influence
Porosity defects are manifested as smooth holes of different sizes on the surface after machining, with an oxidized color on the hole wall. This defect mainly affects the mechanical properties and airtightness of the casting.
3.2 Cause Analysis
- Insufficient Foam Combustion: When the pouring temperature is low, the foam burns incompletely, and the gas is not completely discharged, resulting in porosity under the skin.
- Thick Coating: The thick coating at the motor hole prevents the gas generated by the foam combustion from being discharged, resulting in porosity.
- Low Vacuum Degree: The small vacuum degree makes it impossible to timely extract the gas, resulting in porosity.
- Unreasonable Process Design: The lack of exhaust ports at the top of the flywheel housing causes the gas to concentrate at the top of the body and cannot be completely discharged, resulting in porosity.
3.3 Improvement Measures and Results
- Increase the Pouring Temperature: Increase the pouring temperature from 1430 – 1440°C to 1450 – 1460°C.
- Reduce the Coating Thickness: Reduce the coating thickness at the motor hole from 2.0mm to 0.5mm.
- Increase the Vacuum Degree: Increase the vacuum degree from -0.025MPa to -0.045MPa.
- Add Exhaust Pieces at the Motor Hole: Add an exhaust piece with a size of 50mm (length) x 30mm (height) x 5mm (width) at the motor hole.
The results of the process test are shown in the following table:
Improvement Measure | Number of Samples | Number of Porosity Defects | Porosity Defect Ratio at Motor Hole |
---|---|---|---|
Increase Pouring Temperature | 20 | 4 | 20% |
Reduce Coating Thickness | 20 | 5 | 25% |
Increase Vacuum Degree | 20 | 3 | 15% |
Add Exhaust Piece | 20 | 0 | 0% |
After implementing the measure of adding exhaust pieces, the porosity defect at the motor hole was completely eliminated.
4. Analysis and Improvement of Sand Washing Defects in Connecting Rod Bracket Castings
4.1 Defect Appearance and Influence
Sand washing defects are manifested as a tumor-like mixture of sand grains and metal at the bottom of the cavity and the part where the molten iron flows into the cavity at the gate, which mainly affects the internal quality and dimensional accuracy of the casting.
4.2 Cause Analysis
- Low Coating Strength: The coating at the inner gate is washed away by the molten iron, resulting in coating rupture.
- High Pressure at the Inner Gate: The high pressure at the inner gate causes the coating to rupture.
4.3 Improvement Measures and Results
- Increase the Coating Thickness at the Inner Gate: Increase the coating thickness at the inner gate from 1.5mm to 2.2mm by adding one more dipping coating process.
- Increase the Number of Inner Gates: Add one more inner gate with the same size at the bottom.
The results of the production verification are shown in the following table:
Improvement Measure | Number of Samples | Number of Sand Washing Defects | Sand Washing Defect Ratio |
---|---|---|---|
Increase Coating Thickness at Inner Gate | 50 | 6 | 12% |
Increase Number of Inner Gates | 50 | 0 | 0% |
After implementing the measure of increasing the number of inner gates, the sand washing defect was completely eliminated.
5. Conclusion
In the development of new products, casting defects can be effectively avoided by clever process design. In the process of process verification, the number of products should be gradually increased from small batches to large batches to avoid losses caused by insufficient consideration. In the process of process verification, the five aspects of understanding the current situation, analyzing the causes, formulating plans, implementing countermeasures, and confirming the effects should be promoted step by step to ultimately achieve the goal of completely solving the problem.