Casting cranes play a crucial role in steel mills as they are essential equipment for extracting and tilting molten iron ladles. However, with the advancement of metallurgical technology, the usage frequency of these cranes has been on the rise, and the issue of fatigue life calculation has become an urgent problem to be solved. Additionally, in the context of increasingly fierce market competition, cost control is also a significant factor to ensure the success of a project. Against this backdrop, designers are required not to rely solely on experience or design without considering costs. Instead, they must adopt modern design methods for analysis and comparison, and then combine their own design experience for optimization, so as to create products that are both cost-effective and highly competitive in the market.
This article focuses on the cracking problem that occurred at the web gate opening of the main beam of a casting crane in a certain steel mill. By referring to relevant design materials, detailed analysis and research were conducted on the loads that the main beam endured during the ladle turning operation of the crane. The S-N curve of the material was determined, and static strength and fatigue strength analyses and calculations were carried out to identify the reason why the fatigue life at the web gate opening was significantly lower than the design life of the main beam. Through the optimization design of the original opening structure, the fatigue life was made to be consistent with the design life of the main beam. Years of practical verification have shown that cracking problems have been essentially eliminated, providing valuable experience for the design of the metal structure of future casting cranes.
1. Introduction
The casting crane is a vital device for extracting and dumping molten iron ladles in steel mills. Due to its operation in high-temperature and dusty environments, electrical control equipment and drive devices are placed inside the bridge main beam and sealed, and inspection holes are opened on the web of the main beam to facilitate the entry and exit of operators for equipment maintenance. In the 20th century, the opening generally adopted a rectangular structure as shown in Figure 1, with R150 mm fillet arcs at the four corners to reduce stress concentration, and reinforcement rings were added. At that time, due to the fact that most steel mills in our country adopted the open-hearth steelmaking technology, which had relatively low efficiency, the usage frequency of the crane was not high, so there were few fatigue cracks in actual use. However, in the 21st century, all the steelmaking industries in our country have adopted the converter steelmaking technology, which has greatly improved the production efficiency, and the usage frequency of the crane has also been increasing. Especially during the prosperous period of the vigorous development of the steel industry in our country from 2003 to 2009, there were more and more feedbacks on cracking at the web gate opening of the main beam, which has become the main factor restricting the design life of the main beam. Therefore, it is extremely urgent to conduct fatigue calculation and structural improvement for this area.
2. Engineering Calculation Loads
The loads endured by the main beam mainly include the concentrated load generated by the wheels of the trolley, the uniformly distributed load caused by the self-weight of the main beam, the electrical control equipment, and the main beam platform, as well as the horizontal inertial load produced when the crane starts and brakes.
2.1 Concentrated Load
The concentrated load refers to the force exerted on the wheels of the trolley when the crane is fully loaded, which is the force resulting from the rated load and the self-weight of the trolley acting on the wheels. Since the trolley will be subject to impact during hoisting and running, the engineering practice usually adds the hoisting dynamic load coefficient and the running impact coefficient for calculation. Given that the rated lifting capacity of the crane is 210 tons, the self-weight of the trolley is 90 tons, and the number of wheels is 8, with and taken as 1.17 and 1 respectively, then the dynamic wheel pressure of the trolley is approximately tons, calculated as .
2.2 Uniformly Distributed Load
The uniformly distributed load refers to the force acting on the entire span of the main beam, generally referring to the force generated by the self-weight of the main beam and the platform and electrical control equipment attached to it. Due to the fact that the self-weight of the main beam will generate a pulsed dynamic response due to vibration when the crane is loading, unloading, or braking under load, the engineering practice usually adds the hoisting impact coefficient for calculation. It is known that the span of the main beam is 22 meters, the self-weight is 36 tons, the platform weighs 2.3 tons, and the electrical control equipment weighs 0.5 tons, with taken as 1.1, then the uniformly distributed load is approximately tons per meter, calculated as .
2.3 Horizontal Inertial Load
The horizontal inertial load refers to the horizontal force exerted on the main beam due to the inertia of the lifting load and the self-weight when the crane brakes. In engineering, it is calculated as 1.5 times the product of the mass and the running acceleration. It is known that the running speed of the large vehicle is 80 meters per minute, and a 1/4 drive is adopted, then the horizontal inertial forces generated by the concentrated load and the uniformly distributed load are respectively tons, calculated as , and tons per meter, calculated as .
3. Main Beam Strength Analysis
3.1 Establishment of the Finite Element Model
SolidWorks 3D software was used to conduct 3D solid modeling of the main beam, with the material being Q355B. Due to the relatively complex structure of the main beam, in order to improve the running speed, the detail features that have little influence on the analysis results were simplified, such as removing the process fillets and grooves on the parts. The main beam was fabricated by welding multiple steel plates, and the welded joints were treated by fusion. When conducting the finite element modeling, it was regarded as an equal-strength contact connection. According to the structural characteristics of the main beam, shell elements were used for mesh division, with a total of 73,485 elements and 139,692 nodes.
3.2 Static Strength Analysis
The trolley is a moving load on the main beam. When the trolley is located at 1/4 of the span, this position is generally also the web gate opening position and the full-load ladle turning operation position of the crane, and the normal stress and shear stress at this section are considerable, posing a certain degree of danger. Finite element analysis was carried out using SolidWorks Simulation, and the stress results are shown in Figure 3. It can be seen from Figure 3 that the stress suddenly increases at the web gate opening position, reaching a maximum of 152.24 MPa, while the stress around is below 115 MPa.
3.3 Fatigue Strength Analysis
The main beam is subjected to alternating loads. Even if the stress does not reach the strength failure limit, with the cycling of alternating loads to a certain number of times, cracks will still occur, fatigue damage will take place, resulting in its inability to bear the original load until fatigue failure occurs. This kind of failure is more concealed and dangerous. In the GB/T 3811-2008 “Crane Design Specifications”, the stress ratio method has been used for fatigue calculation. With the development of fatigue calculation theories, it is pointed out in the design specifications of American highway bridges that the nominal stress is the main variable to determine the fatigue strength of each rib plate construction detail, which has changed the traditional view in the academic circle, and this conclusion has been adopted by many steel structure design departments. The nominal stress method reflects the relationship between the nominal stress S of the material and the fatigue life N by the S-N curve, which is expressed by the formula .
3.3.1 Determination of the S-N Curve
Casting cranes generally have a relatively high working level, usually A7 or A8. During the design and manufacturing process, it is required to polish the welds of key parts, and the stress concentration level is controlled at K2. When extracting and dumping the ladle, it is generally a full-load operation, so the stress state level of the main beam is generally taken as P4. According to the provisions on fatigue calculation in the GB/T 3811-2008 “Crane Design Specifications”, the S-N curve was established by using the basic fatigue allowable stress values corresponding to the stress concentration level K2 of the welded component connection for the working levels E1-E8 and the corresponding number of cycles for the structural member stress level state P4, and the curve data are shown in Table 1.
3.3.2 Load Spectrum at the web gate
Taking the transportation of the ladle by the casting crane to the next transportation of the ladle as a working cycle, the load spectrum of the horizontal and vertical loads at the web gate opening within a working cycle time domain was established, as shown in Figure 4. In Figure 4, A-B-C-D represents the crane transporting the full ladle to the front of the converter; D-E represents the crane conducting the ladle tilting operation for the converter iron water; E-F-G-H represents the crane completing the ladle tilting and transporting the empty ladle to the pouring pit.
3.3.3 Analysis Results
As shown in the fatigue life analysis results of the main beam in Figure 5, fatigue failure will occur at the web gate opening after cycling to times. For casting cranes, a three-shift system is generally adopted, with 17 working cycles per shift. Excluding the regular maintenance time, it works approximately 350 days a year, that is, there are about working cycles in a year. According to this calculation, fatigue cracks will appear at the web gate opening of the main beam after about 6 years, which is far lower than the design life of about 15-17 years for the casting crane.
4. Stress Concentration Analysis at the Web Gate Opening
From the analysis results of static strength and fatigue strength, it can be seen that a sudden change in stress occurs at the fillet of the web gate opening. According to the stress concentration theory, when a rectangular hole is opened on the center line of a plate strip that bears in-plane bending moments, a very high concentrated stress will be generated at point A as shown in Figure 6, and its value is:
.
In the formula: represents the concentrated stress at point A, represents the reference stress of the web, H represents the height of the main beam web, h represents the height of the opening, a represents the width of the opening, and r represents the fillet radius of the opening.
5. Analysis of the Influence Degree of the Opening on the Stress Concentration of the Main Beam
It can be seen from Equation (1) that under the condition of a constant height of the main beam web, the concentrated stress at point A is related to the height, width, and fillet radius of the opening. In engineering design, in order to reduce the concentrated stress, reinforcement rings are generally added; in addition, openings are made to facilitate the entry and exit of operators, and usually, the width of the hole is set to 650 mm, and the height is 1600-1800 mm. In order to study the influence of the opening on the stress concentration of the main beam, taking the hole height and fillet radius as parameters, through finite element calculation, the variation law of the concentrated stress under different combinations was analyzed. The stress situation at point A under each set of parameters is shown in Table 2.
It can be seen from Table 2 that the concentrated stress at point A increases with the increase in the opening height and decreases with the increase in the fillet radius. When the fillet radius is 325 mm, that is, when the hole type is a long elliptical hole, the concentrated stress is the smallest.
6. Optimization of the Opening Structure
In order to improve the service life of the crane bridge, it is necessary to make improvements to the web gate opening to make it tend to be consistent with the overall life of the crane main beam.
6.1 Reduce Stress Concentration
In engineering design, to reduce the stress concentration phenomenon, the fillet should be as large as possible, and the opening height should be as small as possible. However, at the same time, in order to meet the structural design requirements, the minimum height is 1600 mm, and the maximum height does not exceed 0.67H according to the equal-inertia moment reinforcement theory of the reinforcement ring. As shown in Figure 7, the web gate opening structure was changed to a long elliptical shape, and in order to reduce the concentrated stress at the opening, reinforcement ribs were also arranged on the inner side of the web. After reloading and conducting static strength and fatigue strength analyses again, the stress at the web gate opening dropped to 115.66 MPa, and the fatigue life increased to times, approximately 15.5 years, which is consistent with the design life of the main beam.
6.2 Welding Method of the Reinforcement Ring
Furthermore, due to the manufacturing errors of the web opening and the reinforcement ring, it cannot be guaranteed that the opening and the reinforcement ring will be completely fitted. The welding method as shown in Figure 8-2 should be adopted to avoid the internal stress caused by the weld filling in the gap between the web and the reinforcement ring, and it is required to polish the weld to eliminate the residual stress generated during the manufacturing process.
7. Conclusion
As the load-bearing foundation of the crane, the bridge determines the service life of the crane. With the continuous improvement of metallurgical technology, the usage frequency of casting cranes is getting higher and higher, and the calculation of fatigue life has become an urgent problem to be solved. Additionally, due to the increasingly fierce market competition, cost control is also an important factor to ensure the successful bidding of the project. In this context, designers are required not to rely solely on experience or design without considering costs. They must adopt modern design methods for analysis and comparison, and then combine their own design experience for optimization. Only in this way can the designed products be both high-quality and cost-effective, and more competitive in the market.
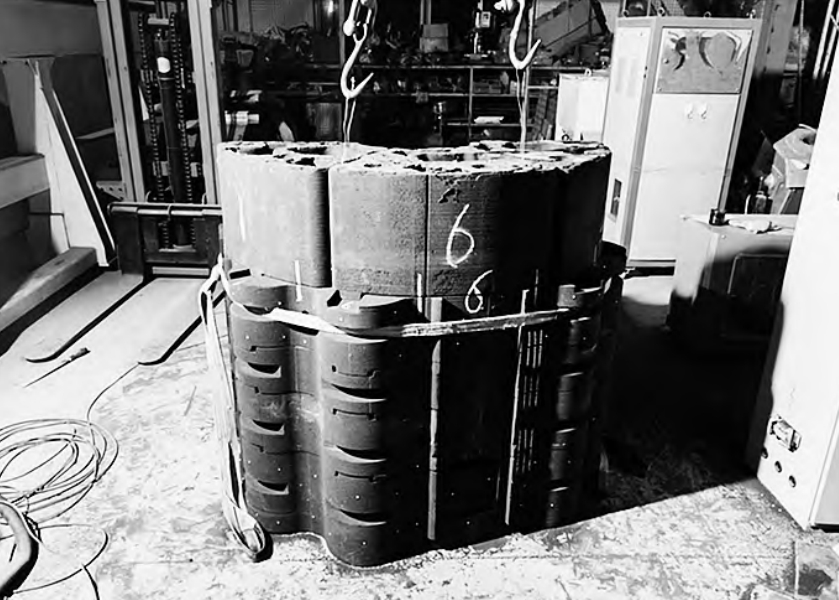