1. Introduction
As global industries increasingly prioritize sustainability, the cement manufacturing sector faces mounting pressure to reduce energy consumption and operational costs. At Pingyi Zhonglian Cement Co., Ltd., we recognized the urgent need to optimize our grinding systems. This article details our successful implementation of ultra-thin lining plates in a Φ4.2 m ×13 m cement mill, which significantly lowered grinding power consumption while maintaining production efficiency.
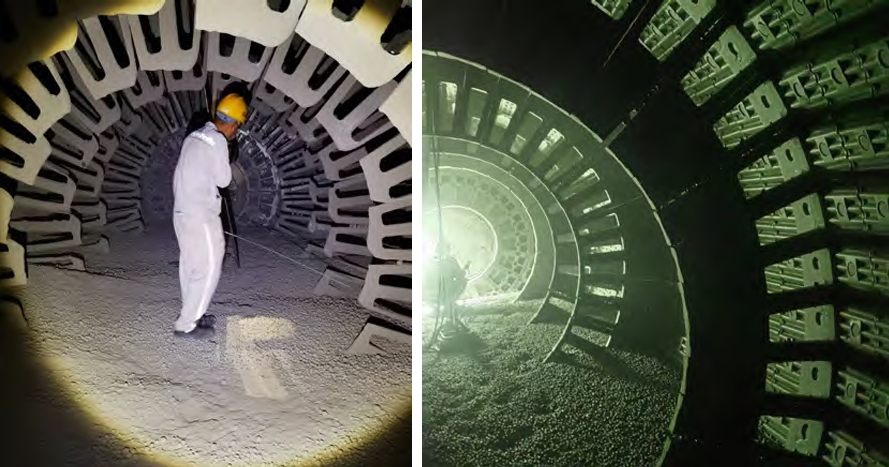
2. Background and Technical Challenges
Our cement grinding system (2# mill) employs a combined roller press and ball mill process. Key equipment includes:
- Roller Press: HFCG160-140
- Ball Mill: Φ4.2 m ×13 m (5.6 rpm, 3550 kW motor)
- Separators: DS-4000 and HFV4000
Despite robust performance, the second chamber’s original wave lining plates and activation rings suffered severe wear, leading to inefficiencies:
- High grinding power consumption: 30 kWh/t
- Frequent maintenance due to lining plate degradation
- Suboptimal material flow control
Our goal was to reduce energy use by 1.5 kWh/t while ensuring operational reliability. After evaluating multiple solutions, we partnered with Xuzhou Xinhua Wear-Resistant Materials Co., Ltd. to deploy ultra-thin wave lining plates and reconfigure activation rings.
3. Implementation of Ultra-Thin Lining Plates
3.1 Design and Material Properties
The new ultra-thin lining plates feature:
- Thickness: 30 mm (45.5% lighter than original plates)
- Material: Medium-carbon multi-alloy steel
- Hardness: 50–55 HRC
- Impact Toughness: 15–20 J/cm²
- Manufacturing Process: Lost-foam casting with specialized heat treatment
3.2 Installation and Benefits
- Reduced Mass: Total lining plate weight decreased from 27.22 t to 15.12 t (Table 1).
- Ease of Installation: Lighter plates simplified handling and reduced downtime during maintenance.
- Enhanced Grinding Efficiency: Increased mill effective volume allowed optimized grinding media distribution.
Table 1: Comparison of Lining Plate Parameters
Parameter | Original Lining Plates | Ultra-Thin Lining Plates | Change (%) |
---|---|---|---|
Thickness (mm) | 55 | 30 | -45.5% |
Weight per Unit (kg) | 22 | 12 | -45.5% |
Total Mass (t) | 27.22 | 15.12 | -44.5% |
4. Optimization of Activation Rings
To complement the lining plate upgrade, we reconfigured activation rings in the second chamber:
- Original Configuration: 6 rings (252 units, 100 kg each)
- New Configuration: 3 rings (126 units, 100 kg each) spaced 1 m apart
This adjustment slowed material flow, prolonging grinding time and improving fineness.f
5. Adjustment of Grinding Media
The increased effective volume from thinner lining plates necessitated recalibrating grinding media. Key changes included:
- First Chamber: Larger ball diameters (Φ50–Φ20 → Φ50–Φ25)
- Second Chamber: Smaller media (Φ30–Φ15 → Φ25–Φ12)
Table 2: Grinding Media Distribution Before and After Modification
Chamber | Media Size (mm) | Before (t) | After (t) |
---|---|---|---|
First | Φ50 | 2 | 5 |
Φ40 | 3 | 6 | |
Φ30 | 25 | 16 | |
Φ25 | 20 | 18 | |
Φ20 | 10 | 3 | |
Total | 60 | 48 | |
Second | Φ30 | 10 | – |
Φ25 | 25 | 5 | |
Φ20 | 35 | 20 | |
Φ17 | 50 | 55 | |
Φ15 | 30 | 45 | |
Φ12 | – | 8 | |
Total | 150 | 133 |
6. Results and Economic Benefits
6.1 Operational Performance
Post-modification data (Table 3) highlights:
- Power Consumption: Reduced from 30 kWh/t to 28.5 kWh/t
- Specific Surface Area: Increased from 335 m²/kg to 352 m²/kg
- Mill Current: Dropped by 25 A (195 A → 170 A)
Table 3: Production Performance Comparison
Metric | Before | After | Change |
---|---|---|---|
Grinding Power (kWh/t) | 30 | 28.5 | -1.5 |
Specific Surface Area | 335 | 352 | +17 |
45 μm Residue (%) | 5.5 | 7.2 | +1.7 |
Mill Current (A) | 195 | 170 | -25 |
Mill Power (kW) | 3,350 | 2,850 | -500 |
6.2 Cost Savings
- Material Costs: Saved ¥219,794 via lighter lining plates and fewer activation rings.
- Grinding Media: Reduced usage saved ¥217,500.
- Energy Savings: Annual electricity cost reduction: ¥682,500 (700,000 t/year, ¥0.65/kWh).
Total Annual Savings: ¥1.12 million
7. Long-Term Reliability and Future Plans
After six months of operation, the ultra-thin lining plates demonstrated exceptional wear resistance and stability. Key observations include:
- No significant deformation or cracking
- Consistent grinding performance
- Reduced vibration and noise
Future steps involve:
- Extending lining plate technology to other mills.
- Integrating IoT sensors for real-time wear monitoring.
- Exploring advanced materials (e.g., ceramic composites).
8. Conclusion
The adoption of ultra-thin lining plates in our Φ4.2 m ×13 m cement mill achieved dual benefits: 1.5 kWh/t energy reduction and ¥1.12 million annual savings. This case underscores the critical role of innovative material solutions in industrial sustainability. By continuously refining grinding systems, we aim to set new benchmarks for eco-efficient cement production.
Formula Example:
The energy-saving percentage can be calculated as:Energy Saving (%)=Ebefore−EafterEbefore×100=30−28.530×100=5%Energy Saving (%)=EbeforeEbefore−Eafter×100=3030−28.5×100=5%