1. Introduction
Casting conveyor equipment plays a crucial role in the foundry industry, facilitating the efficient movement of materials. However, its operation often generates significant vibrations, which can have detrimental effects on the surrounding environment, including adjacent equipment and buildings. This not only affects the precision of manufacturing processes but may also pose potential safety risks. For instance, in some projects, the vibration from a boiling cooling bed has led to a decrease in the machining accuracy of nearby equipment, resulting in product defects. In other cases, vibrating equipment has caused vibrations in factory buildings, especially in doors and windows, which may undermine the structural integrity of the building over time.
To address these issues, vibration control design is essential. Among various vibration control methods such as active isolation, passive isolation, and path isolation, this article focuses on the dual – mass vibration isolation design for casting conveyor equipment. This design involves adding an additional isolation unit between the equipment and its foundation, aiming to reduce the vibration transmitted to the surroundings while maintaining the equipment’s operational efficiency.
2. Understanding Vibration in Casting Conveyor Equipment
2.1 Characteristics of Vibration in Casting Conveyor Equipment
Vibration conveyor equipment, which operates based on the principles of vibration utilization engineering, has unique vibration characteristics. It is designed to operate near resonance to achieve efficient material conveyance, which results in high – energy vibrations. These vibrations have a wide – reaching impact area, potentially affecting a large portion of the factory environment.
The vibration energy generated during operation is a key concern. A significant amount of energy is transferred from the moving parts of the equipment to the surrounding structures. This energy transfer can cause unwanted vibrations in adjacent machinery, leading to issues such as misalignment, increased wear and tear, and reduced lifespan of the affected equipment.
2.2 Impact on the Surrounding Environment
The impact of casting conveyor equipment vibration on the surrounding environment is multi – faceted. In industrial settings, it can disrupt the normal operation of nearby precision – based equipment. For example, in a machining area close to a vibrating casting conveyor, the precision of machining operations may be compromised, leading to products with inaccurate dimensions and poor quality.
From a building – structural perspective, continuous vibrations can cause fatigue in building components. Over time, this may lead to cracks in walls, weakened support structures, and increased maintenance costs. In extreme cases, it can even pose a threat to the safety of workers in the building.
3. Dual – Mass Vibration Isolation Design: An Overview
3.1 Principle of Dual – Mass Vibration Isolation
The dual – mass vibration isolation design is a practical and cost – effective solution for reducing vibration transmission. As shown in Figure 1, this design adds a set of isolation units between the equipment and its foundation. The upper part represents the equipment itself, the lower U – shaped structure is the equipment foundation, and the middle “fish – belly – type” structure along with the metal spiral springs below it form the newly added isolation unit.
The principle behind this design is to create an additional layer of vibration attenuation. The isolation unit’s parameters, such as the mass of the added mass block, the stiffness of the isolation device, and the damping ratio, can be adjusted to optimize the vibration isolation performance. This design allows for greater flexibility compared to traditional isolation methods, as the parameters of the isolation unit are not solely dependent on the equipment’s operating parameters.
Component | Function |
---|---|
Equipment | The source of vibration during operation |
Added Isolation Unit | Reduces the vibration transmitted from the equipment to the foundation |
Foundation | Supports the equipment and isolation unit, and should transmit minimal vibration to the surrounding ground |
3.2 Advantages of Dual – Mass Vibration Isolation Design
This design offers several advantages. Firstly, the parameters of the newly added isolation unit are relatively independent of the equipment’s operating conditions. This means that it can be customized and adjusted according to the specific requirements of the installation environment, providing greater flexibility in vibration control.
Secondly, the dual – mass vibration isolation design does not affect the original technological conditions of the equipment. It is equally applicable to both newly designed projects and retrofit projects. This makes it a versatile solution for different types of industrial setups.
Finally, this design effectively meets the equipment’s technological needs while minimizing the vibration impact on the surrounding environment. By reducing the vibration transmitted to the foundation, it helps to maintain a more stable working environment for adjacent equipment and buildings.
4. Optimization of Isolation Parameters
4.1 Parameters Considered in the Optimization Process
In the optimization of the dual – mass vibration isolation system, several key parameters need to be considered. These include the mass of the added mass block (), the stiffness of the added isolation device (), and the damping ratio () of the isolation system.
The mass of the added mass block () is an important factor. It was varied in multiples of the equipment’s moving part mass (), specifically 1 to 10 times , resulting in 10 different calculation and analysis cases. This was done to study how different mass ratios affect the vibration isolation performance.
The stiffness of the added isolation device () was determined based on the natural frequency of the isolation system. The natural frequency of metal spiral springs typically ranges from 2.0 Hz to 5.0 Hz, with a sampling interval of 0.1 Hz, resulting in 31 different cases. The relationship was used to calculate the stiffness, where is the natural frequency of the isolation device.
The damping ratio () of the isolation system was another crucial parameter. It was varied from 0.05 to 0.15 with a sampling interval of 0.01, giving 11 different cases. These values were selected based on the typical damping ratio range of metal spiral springs.
Parameter | Range | Sampling Interval | Number of Cases |
---|---|---|---|
(multiple of ) | 1 – 10 | 1 | 10 |
(based on ) | Hz | 0.1 Hz | 31 |
0.05 – 0.15 | 0.01 | 11 |
4.2 Calculation and Analysis of Working Conditions
In total, 3410 different working conditions were calculated and analyzed. To ensure the calculations were representative of real – world scenarios, the parameters of the foundation (, , ) were determined according to specific design principles. The mass of the foundation () was set to 2.5 times the sum of the equipment’s weight and the mass of the added isolation unit. The thickness of the foundation was fixed at 1.0 m (without soil covering), and the soil beneath the foundation was assumed to be cohesive soil with a bearing capacity characteristic value of 180 kPa. Based on the national standard “Design Standard for Dynamic Machine Foundations” GB50040 – 2020, the compressive stiffness coefficient of the foundation soil was 41000 kN/m³.
The dynamic system was simplified into a three – degree – of – freedom mechanical system for calculation purposes. The dynamic equation of this system can be expressed as . Although the detailed solution process of this equation is not elaborated here, a relatively simple method can be found in the reference literature [4], which uses the characteristics of the dynamic equation solution to quickly obtain the response amplitudes of each degree of freedom.
4.3 Results and Conclusions of Parameter Optimization
Through the calculations and analysis of these 3410 cases, several important conclusions were drawn.
Firstly, as shown in Figure 2 and Figure 3, the larger the mass of the added mass block (), the smaller the vibration response of the foundation. However, considering both the vibration isolation efficiency and economic factors, it was found that the mass of the newly added isolation body is most suitable when it is 3 – 6 times the weight of the equipment. In this range, the vibration response of the foundation can meet the requirements of relevant national standards and the allowable vibration level of the workshop environment, while achieving a good balance between isolation efficiency and cost.
Secondly, the isolation frequency of the newly added isolation unit should not be too low. It is recommended to be at least 1.25 times the isolation frequency of the equipment’s built – in isolation device. A lower isolation frequency may lead to insufficient vibration isolation and increased vibration transmission to the foundation.
Thirdly, the damping ratio should not be too small. A damping ratio of 0.10 or higher is advisable. This can prevent excessive vibration displacement of the added mass block and also help to reduce the large – displacement vibration phenomenon during the equipment startup phase.
Finally, compared with the rigid installation method (where the equipment is directly placed on a large – volume concrete block), the dual – mass vibration isolation design can reduce the vibration response of the equipment foundation by more than half. This clearly demonstrates the high – efficiency vibration isolation performance of the dual – mass system.
5. Engineering Example
5.1 Project Background and Challenges
In a certain factory’s casting workshop, a boiling cooling bed equipment was causing problems. According to the owner’s feedback, the operation of the boiling cooling bed was making the products processed by nearby machining equipment unqualified. The boiling cooling bed was located approximately 50 m away from the machining equipment.
The main challenges in this project were to reduce the vibration transmitted from the boiling cooling bed to the machining area. To address this, a series of modification measures were taken. The connection between the boiling cooling bed equipment and the adjacent sand – processing line equipment was removed, and the entire equipment was lifted to a certain height. The original equipment foundation legs were chiseled off, and a set of isolation units (concrete counterweights and metal spiral springs) was added between the equipment and the foundation.
5.2 Equipment Parameters and Isolation Unit Design
The parameters of the boiling cooling bed equipment and the added isolation unit were carefully selected. The weight of the equipment’s moving parts was 16 t, and the isolation frequency of the equipment’s self – contained metal spiral spring was 2.8868 Hz with a damping ratio of 0.10. The excitation force of the equipment was 280 kN.
The mass of the newly added isolation unit was 62.244 t. Each individual metal spiral spring had a stiffness of 4800 kN/m (with a total of 8 springs). The damping ratios of the metal spiral springs were 0.05 and 0.15 (4 springs for each value, with the high – damping springs placed at the four corners). The mass of the foundation was approximately 194.74 t, and the compressive stiffness of the foundation soil was considered to be 1367286 kN/m with a damping ratio of 0.22.
Equipment/Isolation Unit | Parameter | Value |
---|---|---|
Boiling Cooling Bed | Moving Part Weight | 16 t |
Self – contained Spring Isolation Frequency | 2.8868 Hz | |
Damping Ratio | 0.10 | |
Excitation Force | 280 kN | |
Added Isolation Unit | Mass | 62.244 t |
Spring Stiffness (each) | 4800 kN/m | |
Spring Damping Ratio | 0.05 (4 springs), 0.15 (4 springs) | |
Foundation | Mass | 194.74 t |
Soil Compressive Stiffness | 1367286 kN/m | |
Damping Ratio | 0.22 |
5.3 Vibration Test Results
Vibration tests were conducted before and after the implementation of the dual – mass vibration isolation design. The results showed that after the modification, the vibration acceleration at the upper part of the boiling cooling bed isolation device remained basically unchanged. However, the vibration acceleration at the equipment foundation was reduced to 25% of its original value. In the machining area, multiple measurement points showed a vibration isolation efficiency of over 50%. These results clearly demonstrate the effectiveness of the dual – mass vibration isolation design in reducing vibration transmission and improving the working environment.
6. Conclusion
In conclusion, the dual – mass vibration isolation design is an effective solution for reducing the vibration impact of casting conveyor equipment on the surrounding environment. By adding an isolation unit between the equipment and its foundation and optimizing the parameters of this unit, such as the mass of the added mass block, the isolation frequency, and the damping ratio, it is possible to achieve a high – efficiency vibration isolation effect.
When the mass of the newly added isolation body is 3 – 6 times the weight of the equipment, the isolation frequency is 1.25 times the isolation frequency of the equipment’s built – in isolation device, and the damping ratio is not less than 0.10, the vibration response of the foundation can meet the requirements of relevant national standards and the allowable vibration level of the environment. This design not only ensures the normal operation of the equipment but also protects the surrounding equipment and buildings from the negative effects of vibration.
Future research can further explore the application of this design in different types of casting conveyor equipment and under more complex working conditions. Additionally, efforts can be made to develop more advanced isolation materials and techniques to further improve the vibration isolation performance and cost – effectiveness of the dual – mass system.
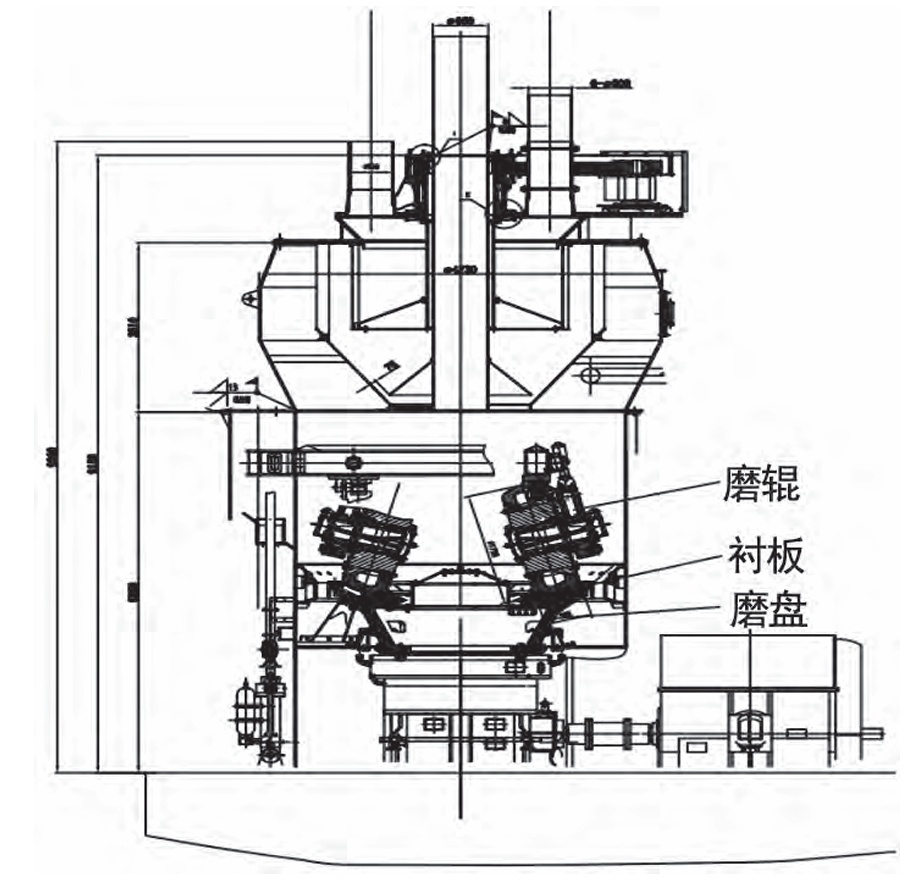