1. Introduction
3D printing, also known as additive manufacturing, has emerged as a revolutionary technology in the manufacturing industry. It has the potential to transform the way products are designed and produced, offering greater flexibility, customization, and efficiency. However, despite its numerous advantages, 3D printing still faces some limitations, such as high costs, limited material options, and slow production speeds.
On the other hand, casting is a traditional manufacturing process that has been used for centuries to produce a wide range of metal components. It is a cost-effective and efficient method for mass-producing complex parts with high precision. However, casting also has its drawbacks, such as the need for expensive molds and tooling, long lead times, and limited design flexibility.
The convergence of 3D printing technology and casting technology offers a promising solution to overcome the limitations of both processes. By combining the advantages of 3D printing, such as rapid prototyping and design freedom, with the benefits of casting, such as high-volume production and material strength, manufacturers can achieve greater productivity, cost savings, and product quality.
2. Overview of 3D Printing Technology
2.1 Types of 3D Printing Technologies
There are several types of 3D printing technologies available today, each with its own unique characteristics and applications. Some of the most common 3D printing technologies include:
3D Printing Technology | Principle | Common Materials | Advantages | Disadvantages |
---|---|---|---|---|
Fused Deposition Modeling (FDM) | Extrudes molten material layer by layer | Thermoplastics (e.g., PLA, ABS) | Low cost, wide range of materials, easy to use | Low resolution, limited material strength, visible layer lines |
Stereolithography (SLA) | Uses a laser to cure liquid resin layer by layer | Photopolymer resins | High resolution, smooth surface finish, suitable for complex geometries | Expensive equipment and materials, limited material options, requires post-processing |
Selective Laser Sintering (SLS) | Sinter powder materials using a laser | Nylon, polycarbonate, metal powders | Strong and durable parts, good for functional prototypes, no support structures needed | High cost, long build times, limited material options, rough surface finish |
Selective Laser Melting (SLM) | Melts metal powder using a laser to create solid parts | Metal powders (e.g., titanium, aluminum, stainless steel) | High-strength metal parts, complex geometries possible, good for aerospace and medical applications | High cost, long build times, requires specialized equipment and expertise, limited material options |
3D Printing (3DP) | Sprays binder onto powder materials to build parts layer by layer | Sand, gypsum, metal powders | Fast printing speed, suitable for large parts, good for casting applications | Low strength, limited material options, requires post-processing |
2.2 Applications of 3D Printing Technology
3D printing technology has a wide range of applications in various industries, including automotive, aerospace, medical, consumer goods, and jewelry. Some of the common applications of 3D printing technology include:
- Prototyping: 3D printing allows designers to quickly and easily create prototypes of their products, enabling them to test and validate their designs before moving into production.
- Customization: 3D printing enables the production of customized products tailored to individual customer needs, providing greater flexibility and personalization.
- Complex Geometries: 3D printing can produce parts with complex geometries that are difficult or impossible to manufacture using traditional manufacturing methods.
- Tooling and Fixtures: 3D printing can be used to produce tooling and fixtures for manufacturing processes, reducing costs and lead times.
- Medical Applications: 3D printing is used in the medical industry to produce customized implants, prosthetics, and surgical models, improving patient outcomes and reducing costs.
3. Overview of Casting Technology
3.1 Types of Casting Processes
There are several types of casting processes available, each with its own unique characteristics and applications. Some of the most common casting processes include:
Casting Process | Principle | Common Materials | Advantages | Disadvantages |
---|---|---|---|---|
Sand Casting | Molten metal is poured into a sand mold | Ferrous and non-ferrous metals (e.g., iron, aluminum, bronze) | Low cost, suitable for large parts, wide range of materials | Low surface finish, limited dimensional accuracy, requires skilled labor |
Investment Casting | Molten metal is poured into a wax or plastic mold, which is then melted away | Ferrous and non-ferrous metals (e.g., stainless steel, titanium, gold) | High precision, excellent surface finish, suitable for complex geometries | High cost, long lead times, limited production volume |
Die Casting | Molten metal is injected into a reusable metal mold under high pressure | Non-ferrous metals (e.g., aluminum, zinc, magnesium) | High production rate, good dimensional accuracy, excellent surface finish | High cost of tooling, limited material options, not suitable for large parts |
Gravity Casting | Molten metal is poured into a mold under the force of gravity | Ferrous and non-ferrous metals (e.g., iron, aluminum, copper) | Simple and cost-effective, suitable for small to medium-sized parts | Low production rate, limited dimensional accuracy, requires skilled labor |
Lost Foam Casting | Molten metal is poured into a mold made of expanded polystyrene foam, which vaporizes during the casting process | Ferrous and non-ferrous metals (e.g., iron, aluminum, magnesium) | Complex geometries possible, no need for cores, good surface finish | High cost of foam patterns, limited production volume, requires specialized equipment |
3.2 Applications of Casting Technology
Casting technology is widely used in various industries to produce a wide range of metal components, including automotive parts, aerospace components, industrial machinery, and consumer goods. Some of the common applications of casting technology include:
- Automotive Industry: Casting is used to produce engine blocks, cylinder heads, transmission cases, and other automotive parts.
- Aerospace Industry: Casting is used to produce aircraft engine components, structural parts, and landing gear components.
- Industrial Machinery: Casting is used to produce gears, pumps, valves, and other industrial machinery parts.
- Consumer Goods: Casting is used to produce jewelry, watches, and other consumer goods.
- Construction Industry: Casting is used to produce architectural components, such as columns, beams, and decorative elements.
4. The Convergence of 3D Printing and Casting Technology
4.1 Advantages of the Convergence
The convergence of 3D printing and casting technology offers several advantages, including:
- Cost Savings: By using 3D printing to produce molds and patterns for casting, manufacturers can reduce the cost of tooling and equipment, as well as the lead time for production.
- Design Freedom: 3D printing allows designers to create complex geometries that are difficult or impossible to manufacture using traditional casting methods, providing greater design freedom and flexibility.
- Rapid Prototyping: 3D printing enables rapid prototyping of casting molds and patterns, allowing manufacturers to quickly test and validate their designs before moving into production.
- Customization: 3D printing and casting technology can be combined to produce customized parts and products, tailored to individual customer needs.
- Improved Quality: By using 3D printing to produce high-precision molds and patterns, manufacturers can improve the quality and dimensional accuracy of cast parts.
4.2 Applications of the Convergence
The convergence of 3D printing and casting technology has a wide range of applications in various industries, including automotive, aerospace, medical, and consumer goods. Some of the common applications of the convergence include:
- Rapid Tooling: 3D printing can be used to produce rapid tooling for casting, such as molds, cores, and patterns, reducing the cost and lead time for tooling production.
- Complex Geometries: 3D printing and casting technology can be combined to produce parts with complex geometries, such as internal cooling channels and lattice structures, improving the performance and efficiency of the parts.
- Customized Castings: 3D printing and casting technology can be used to produce customized castings, tailored to individual customer needs, providing greater flexibility and personalization.
- Medical Applications: 3D printing and casting technology can be used to produce customized medical implants and prosthetics, improving the fit and performance of the devices.
- Aerospace Applications: 3D printing and casting technology can be used to produce high-strength aerospace components, such as engine parts and structural components, reducing the weight and improving the performance of the aircraft.
5. Case Studies
5.1 Automotive Industry
In the automotive industry, the convergence of 3D printing and casting technology has been used to produce a wide range of parts, including engine blocks, cylinder heads, and transmission cases. For example, a major automotive manufacturer used 3D printing to produce a sand mold for casting an engine block, reducing the cost and lead time for tooling production. The 3D-printed sand mold also allowed for greater design flexibility, enabling the manufacturer to optimize the design of the engine block for improved performance and efficiency.
5.2 Aerospace Industry
In the aerospace industry, the convergence of 3D printing and casting technology has been used to produce high-strength components, such as engine parts and structural components. For example, an aerospace company used 3D printing to produce a titanium alloy engine component, which was then cast using investment casting. The 3D-printed component had a complex geometry that was difficult to manufacture using traditional methods, but the combination of 3D printing and casting technology allowed for the production of a high-quality component with excellent performance and reliability.
5.3 Medical Industry
In the medical industry, the convergence of 3D printing and casting technology has been used to produce customized medical implants and prosthetics. For example, a medical device company used 3D printing to produce a patient-specific hip implant, which was then cast using investment casting. The 3D-printed implant had a complex geometry that was tailored to the patient’s anatomy, providing a better fit and improved performance compared to traditional implants.
6. Challenges and Limitations
6.1 Technical Challenges
The convergence of 3D printing and casting technology still faces some technical challenges, such as:
- Material Compatibility: Different 3D printing materials may not be compatible with casting processes, requiring the development of new materials or the modification of existing materials.
- Dimensional Accuracy: 3D printing and casting processes may introduce dimensional errors, which can affect the quality and performance of the final parts.
- Surface Finish: The surface finish of 3D-printed parts may not be suitable for casting, requiring additional post-processing steps to improve the surface finish.
- Process Integration: Integrating 3D printing and casting processes into existing manufacturing systems can be challenging, requiring the development of new process control and monitoring systems.
6.2 Cost Challenges
The convergence of 3D printing and casting technology can also be costly, especially for small and medium-sized enterprises. Some of the cost challenges include:
- Equipment Costs: 3D printing and casting equipment can be expensive, requiring a significant investment in equipment and technology.
- Material Costs: The cost of 3D printing materials and casting materials can be high, especially for high-performance materials.
- Labor Costs: The convergence of 3D printing and casting technology requires skilled labor, which can increase labor costs.
- Production Volume: The cost of 3D printing and casting technology may be higher for low-volume production, making it less cost-effective for small production runs.
6.3 Regulatory Challenges
The convergence of 3D printing and casting technology also faces some regulatory challenges, such as:
- Quality Control: Ensuring the quality and safety of 3D-printed and cast parts can be challenging, especially for medical and aerospace applications.
- Intellectual Property: Protecting intellectual property rights for 3D-printed and cast parts can be difficult, especially in the case of customized parts.
- Standards and Regulations: There is a lack of standards and regulations for 3D printing and casting technology, which can make it difficult to ensure the quality and safety of the final products.
7. Future Trends and Outlook
7.1 Advancements in Materials
The development of new materials for 3D printing and casting technology is expected to continue in the future, enabling the production of parts with improved performance and functionality. Some of the future trends in materials include:
- High-Strength Materials: The development of high-strength materials, such as titanium alloys and nickel-based superalloys, for 3D printing and casting technology, will enable the production of parts with improved strength and durability.
- Biocompatible Materials: The development of biocompatible materials for 3D printing and casting technology, will enable the production of medical implants and prosthetics with improved biocompatibility and performance.
- Functional Materials: The development of functional materials, such as shape memory alloys and piezoelectric materials, for 3D printing and casting technology, will enable the production of parts with unique functional properties.
7.2 Integration with Other Technologies
The convergence of 3D printing and casting technology is expected to be integrated with other technologies, such as robotics, artificial intelligence, and the Internet of Things (IoT), to create smart manufacturing systems. Some of the future trends in integration include:
- Automation: The integration of 3D printing and casting technology with robotics and automation systems will enable the production of parts with greater efficiency and precision.
- Predictive Maintenance: The integration of 3D printing and casting technology with IoT sensors and predictive maintenance systems will enable the monitoring and maintenance of equipment in real-time, reducing downtime and improving productivity.
- Digital Twin: The integration of 3D printing and casting technology with digital twin technology will enable the creation of virtual models of the manufacturing process, allowing for the optimization of the process and the prediction of quality issues.
7.3 Expansion into New Markets
The convergence of 3D printing and casting technology is expected to expand into new markets, such as the construction industry, the energy industry, and the consumer goods industry. Some of the future trends in market expansion include:
- Construction Industry: The use of 3D printing and casting technology in the construction industry will enable the production of customized building components, such as walls, floors, and roofs, reducing the cost and time required for construction.
- Energy Industry: The use of 3D printing and casting technology in the energy industry will enable the production of high-performance components for renewable energy systems, such as wind turbines and solar panels, improving the efficiency and reliability of the systems.
- Consumer Goods Industry: The use of 3D printing and casting technology in the consumer goods industry will enable the production of customized consumer products, such as jewelry, watches, and furniture, providing greater flexibility and personalization.
8. Conclusion
The convergence of 3D printing technology and casting technology offers a promising solution to overcome the limitations of both processes, providing greater productivity, cost savings, and product quality. The convergence has a wide range of applications in various industries, including automotive, aerospace, medical, and consumer goods. However, the convergence still faces some technical, cost, and regulatory challenges, which need to be addressed in order to fully realize its potential. The future of the convergence of 3D printing and casting technology looks promising, with advancements in materials, integration with other technologies, and expansion into new markets expected to drive its growth and adoption in the coming years.
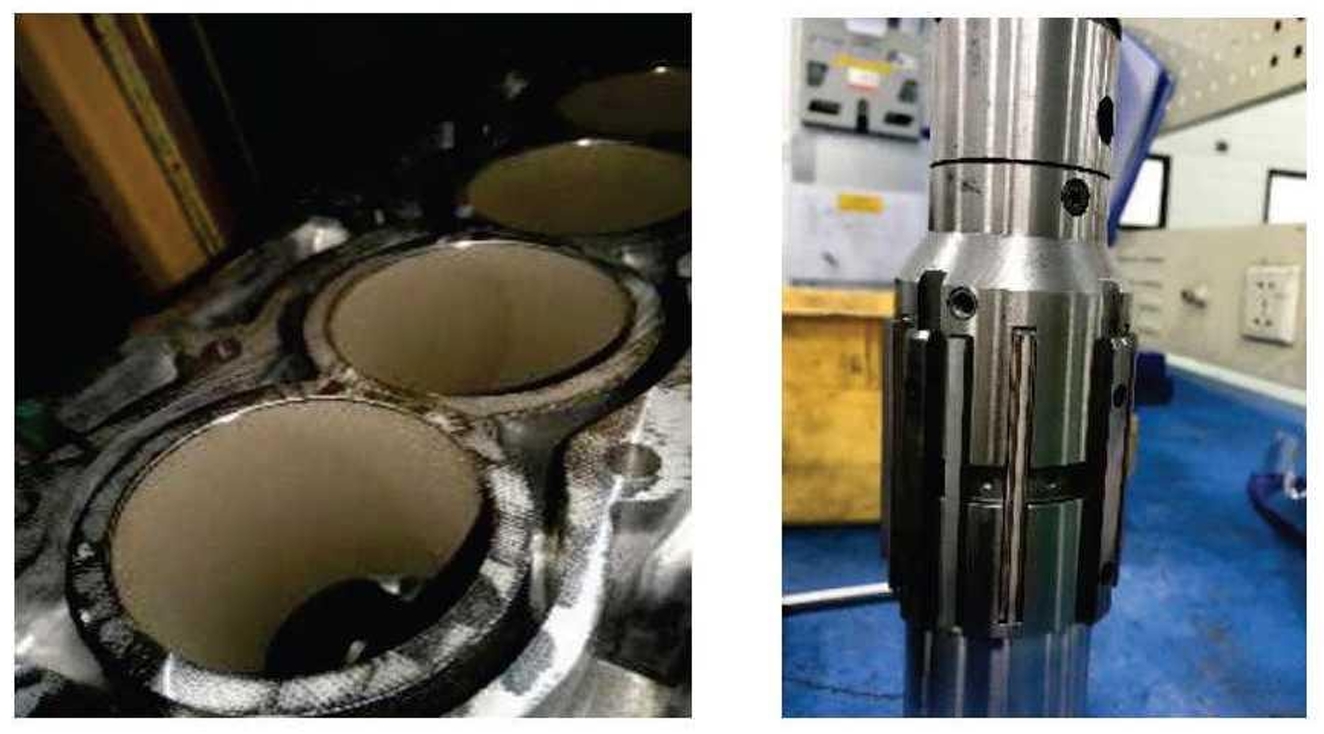