1. Introduction
In the aluminum electrolysis industry, the anode steel claw plays a crucial role. It is a key component in the advanced pre – baked anode electrolytic cell, responsible for clamping the anode carbon block and transmitting a large – scale direct – current. The quality of the anode steel claw, especially its density and conductivity, significantly impacts the production efficiency and economic benefits of aluminum electrolysis.
The production of aluminum by the electrolysis method is an energy – intensive process. In China, the power consumption accounts for 30% – 40% of the original aluminum production cost. Therefore, improving the performance of anode steel claws to reduce energy consumption has become an urgent task. Currently, many anode steel claws in China have quality problems. The use of low – quality raw materials such as scrap steel, miscellaneous steel, and discarded steel claws leads to large fluctuations in the alloy element content. High levels of impurity elements like \(C\geq0.5\%\), \(S\geq0.05\%\), and \(P\geq0.05\%\) increase the resistance of the steel claws. Moreover, the improper casting process causes internal defects such as shrinkage cavities, porosity, and inclusions, further reducing the effective conductive area and increasing the resistivity.
The lost – foam casting process is widely used in the production of various castings due to its advantages such as high – precision casting and less complex mold design. Optimizing the lost – foam casting process for anode steel claws can potentially improve their quality and performance, which is the focus of this research.
2. Chemical Composition and Mechanical Properties Requirements of Anode Steel Claw
2.1 Influence of Chemical Composition on Resistivity
The chemical composition of anode steel claws has a significant impact on their resistivity. As shown in Table 1, different raw materials result in different resistivity values. Anode steel claws produced from high – quality scrap steel have a resistivity in the range of 0.2 – 0.5 μΩ•m. When the raw materials include scrap steel mixed with pig iron, the resistivity can be as high as 0.8 μΩ•m or more. Pure iron has a low resistivity of approximately 0.1 μΩ•m, but its strength is only about 150 MPa, which is too low for practical applications in anode steel claws.
Raw Material | Resistivity (μΩ•m) | Strength (MPa) |
---|---|---|
High – quality scrap steel | 0.2 – 0.5 | – |
Scrap steel + pig iron | ≥ 0.8 | – |
Pure iron | ≈ 0.1 | ≈ 150 |
Table 1: Influence of Different Raw Materials on Resistivity and Strength |
2.2 Optimized Chemical Composition Design
To balance the requirements of resistivity and strength, the anode steel claw is designed as a low – carbon alloy steel. The specific chemical composition range is shown in Table 2.
Element | C | Si | Mn | S | P | Ni |
---|---|---|---|---|---|---|
Composition Range | 0.17 – 0.23 | ≤ 0.6 | 1.00 – 1.16 | ≤ 0.02 | ≤ 0.02 | ≤ 0.8 |
Table 2: Chemical Composition of Anode Steel Claw (Mass Fraction, %) |
2.3 Mechanical Properties Requirements
In addition to chemical composition, the anode steel claw also has specific mechanical properties requirements. After being heat – treated by normalizing, the mechanical properties should meet the standards in Table 3.
Product Name | Material | Heat Treatment | Tensile Strength /MPa | Yield Strength /MPa | Elongation (%) | Notch Impact Absorption Energy /J |
---|---|---|---|---|---|---|
Anode Steel Claw | Low – carbon alloy steel | Normalizing | 500 – 650 | ≥ 300 | ≥ 22 | ≥ 55 |
Table 3: Mechanical Properties of Anode Steel Claw |
3. Test Piece Dimensions and Mold Design
3.1 Selection of Test Piece and Dimensions
The three – claw anode steel claw is selected as the test piece. Its main dimensions are shown in Figure 1 and Table 4. These dimensions are critical for the proper functioning of the anode steel claw in the electrolytic cell.
Dimension | Value |
---|---|
Length | 980 mm |
Height | 400 mm |
Cylinder Diameter | 180 mm |
Cylinder Height | 250 mm |
Crossbeam Width | 100 mm |
Crossbeam Height | 150 mm |
Adjacent Cylinder Center Distance | 400 mm ± 1 mm |
Three – Cylinder Straightness Deviation | < 1 mm |
Table 4: Main Dimensions of Anode Steel Claw |
3.2 Mold Design
The mold is designed with a mechanism – made white model. The white model is divided into two parts from the middle, and the two parts form an anode steel claw. The white model is hollow inside to reduce the gas evolution during the casting process and carbon defects in the casting. Reinforcing ribs are designed inside to control the deformation of the cylindrical white model. A pulling rib is designed between the middle claw – head cylinder and the two – side claw – head cylinders as an inner runner, which also helps prevent the shrinkage deformation of the casting.
4. Process Design and Trial – Production Results
4.1 First – time Process Design and Results
4.1.1 Process Design
The anode steel claw generally prefers the top – pouring casting process. In this design, the claw head is facing down, and the crossbeam is on top. A DN225 mm straight – cylinder exothermic riser is opened on the crossbeam as the pouring and riser port.
4.1.2 Simulation Results
The solidification simulation results using PorCast software are shown in Figure 2. Due to the relatively thin crossbeam of the anode steel claw and the long distance between the riser and the two – end claw heads, the riser cannot effectively perform the feeding function. As a result, there are shrinkage cavities inside the two – end claw heads, which do not meet the flaw – detection requirements.
4.2 Second – time Process Design and Results
4.2.1 Process Design
Based on the first – time simulation results, the process is improved. The anode steel claw is placed with the claw head facing up and the crossbeam down. A cylindrical foam riser with a diameter of 230 mm and a height of 300 mm is placed on each claw head. The inner runner is opened on the claw head, and the cross – runner is placed on the upper part of the pulling rib. Two pieces are cast in one group. The vacuum negative pressure is – 0.06 – – 0.04 MPa, and the pouring temperature is 1580 – 1600 °C. The pouring system is shown in Figure 3.
4.2.2 Casting Results
The ultrasonic flaw – detection results show that for the No. 1 casting, shrinkage cavity defects are found during the processing of the two – side risers. There is no bottom wave in the area with a diameter of about 40 mm on both sides of the cylinder, and obvious defects exist in the 50 – 100 mm depth area of the middle cylinder. For the No. 2 casting, a shrinkage cavity appears after the processing of one – side riser. There is no bottom wave in the area with a diameter of 70 mm on one side, no bottom wave in the area with a diameter of 30 – 35 mm on the other side, and defects exist in the 50 – 100 mm depth area of the middle cylinder. The casting defects are shown in Figure 4.
4.2.3 Cause Analysis
Since the foam white model loses its shape under negative pressure during the casting process, the molten metal is affected by the supercooling caused by air extraction during the filling process. Although feeding risers are installed, they cannot play their proper feeding role. Only when the molten steel in the riser solidifies last can the feeding function of the riser be fully exerted.
4.3 Third – time Process Design and Results
4.3.1 Process Design
According to the test results, the process is further improved. The anode steel claw still has the claw head facing up and the crossbeam down. The original risers on each claw head are changed to exothermic risers. The middle column uses a DN225 mm exothermic riser, and the two – side columns use DN200 mm exothermic risers. The inner runner is opened on the claw – head cylinder, and the cross – runner is placed on the upper part of the pulling rib. Two pieces are cast in one group, as shown in Figure 5.
4.3.2 Casting Results
After cutting the riser, about 10% of the castings have gas – shrinkage cavities at the root of the cylinder riser far from the pouring cup. The number of gas – shrinkage cavity defects is significantly higher in rainy weather.
4.3.3 Cause Analysis of Gas – shrinkage Cavities
The reasons for the generation of gas – shrinkage cavities are as follows:
(1) The white model or the yellow model after painting the coating is not completely dried. During the casting process, water vapor forms pores at high temperatures.
(2) Poor deoxidation during casting leads to the generation of pores.
(3) The design of the casting system is unreasonable, and the gas entrained by the molten steel cannot be discharged in time, forming pores.
(4) The pouring speed is too slow. When the molten steel reaches the riser, it is in a semi – solid state, and the gas cannot float and be discharged outside the casting.
4.4 Fourth – time Process Design and Results
4.4.1 Process Design
Based on the third – time test results, the following improvements are made to the process:
(1) Prolong the drying time of the white model and the yellow model.
(2) When it is rainy, add 0.15% zirconium – iron for enhanced deoxidation when the molten steel is poured from the ladle to 1/3 – 1/2 of the ladle.
(3) Keep the other parts of the casting system unchanged, adjust the cross – runner to the lower part of the pulling rib, increase the pouring cup size, and increase the pouring speed to ensure that the cross – runner is full during the casting process and prevent gas entrainment.
(4) Increase the pouring temperature to 1600 – 1620 °C for casting. The casting system and the casting are shown in Figure 6.
4.4.2 Casting Results
Among the subsequent 500 cast anode steel claws, the scrap rate caused by pores is less than 2%, which indicates that this is a relatively stable process. After cutting the riser, the surface of the casting has no defects, the flaw – detection shows no shrinkage cavities, and the cut – open internal structure is dense without defects.
4.5 Fifth – time Process Design and Results
4.5.1 Process Design
To improve the process yield, an attempt is made to abandon the complex cross – runner and directly pour from the middle exothermic riser. The process changes from casting two pieces in one pour to casting one piece in one pour. The burying – box process and the test results are shown in Figure 7.
4.5.2 Test Results and Analysis
After cutting the riser, there are no shrinkage cavities or pores at the root of the middle riser, but obvious pores are generated at the roots of the two – side risers. The reason is that the molten steel in the two – side risers mainly comes from the bottom of the middle cylinder. The hot molten steel does not flow through the middle pulling rib, so the temperature of the molten steel in the two – side risers is relatively low, and the gas in the molten steel cannot effectively float up, resulting in pores.
5. Conclusion
Through continuous experimentation and improvement, the fourth – improved process design plan is adopted for the mass production of anode steel claws. In this process, the two – side cylinders use DN200 mm exothermic risers, the middle cylinder uses a DN225 mm exothermic riser, and the cross – runner is placed at the bottom of the inner runner in the casting system. This process can produce high – density and defect – free anode steel claw castings.
Compared with the currently used steel claw materials, the resistivity of the anode steel claws produced by this process can be reduced by about 30% in the working temperature range of the anode steel claw. This significant reduction in resistivity can lead to a large – scale power – saving effect, which has been recognized by users. It also generates substantial economic and social benefits and will surely promote the technological progress of the aluminum electrolysis industry in China.
The optimization of the lost – foam casting process for anode steel claws is not only a technical innovation in the casting field but also an important measure to meet the requirements of energy – saving and high – efficiency in the aluminum electrolysis industry. In the future, with the continuous development of technology, further research can be carried out on the casting process and material improvement of anode steel claws to continuously improve their performance and quality.
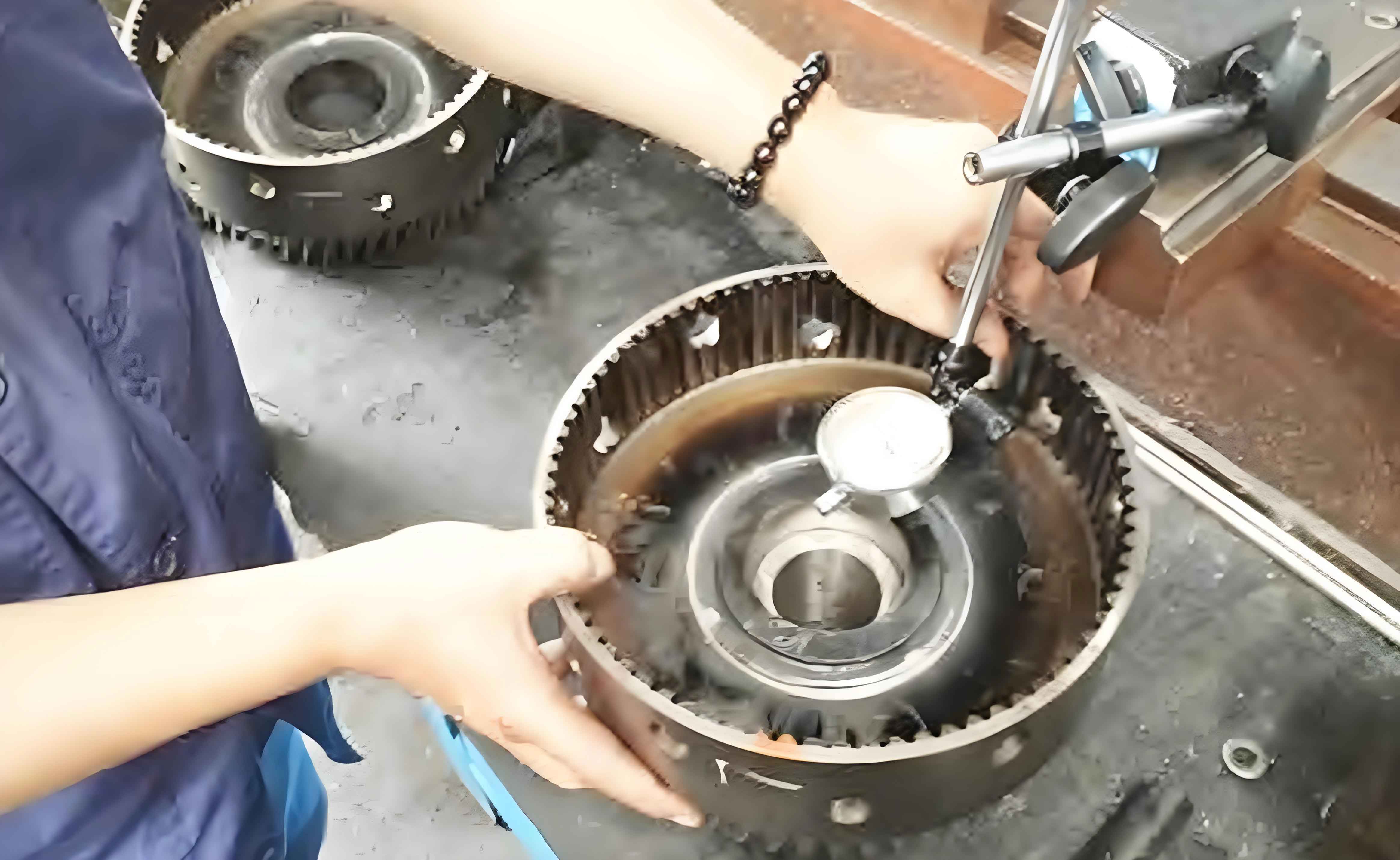