The advancement of intelligent and green manufacturing has become a pivotal direction for China’s industrial transformation. As a fundamental sector in mechanical manufacturing, the foundry industry faces persistent challenges in achieving precision and sustainability during the grinding and finishing stages of engine cylinder block casting. This paper presents an optimized grinding fixture design that addresses localization inaccuracies, poor adaptability, and structural wear in traditional fixtures, enabling efficient and precise removal of burrs and excess material.
Current Challenges in Engine Cylinder Block Grinding
Conventional grinding fixtures for engine cylinder blocks rely on fixed positioning columns and static support structures (Figure 1a). These designs exhibit three critical limitations:
- Low Universality: Dedicated fixtures are required for different cylinder block geometries, increasing equipment costs and changeover time.
- Positioning Wear: Continuous operation causes cumulative wear at contact points, leading to grinding deviations exceeding ±0.5 mm (Figure 1b).
- Manual Rework: 23% of processed components require secondary grinding, raising production costs by 15–18%.
$$ \delta_w = \frac{F_n \cdot \mu \cdot t}{A_c} $$
Where δw represents wear depth (mm), Fn is normal grinding force (N), μ is friction coefficient, t is operational duration (hr), and Ac is contact area (mm²). This model explains rapid fixture degradation under cyclic loading.
Optimized Modular Fixture Design
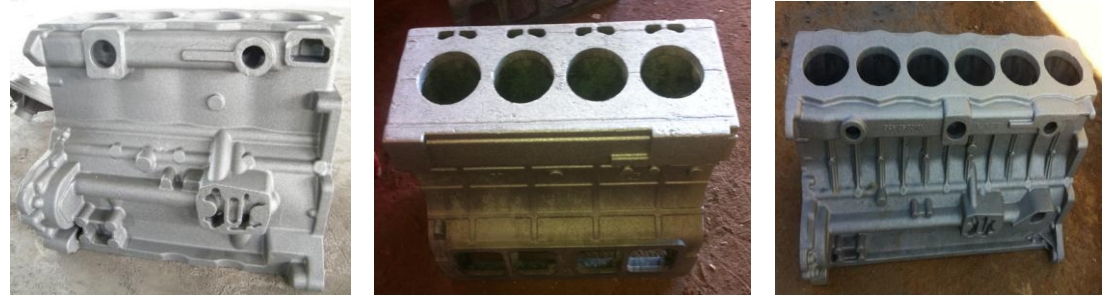
The redesigned grinding fixture incorporates three innovation clusters:
Component | Design Feature | Technical Advantage |
---|---|---|
Baseplate | 35–50 mm thickness with recessed slots | Structural rigidity ≥1.8× original |
Interchangeable Inserts | 20–25 mm modular blocks with Ø8H7定位销 | Changeover time reduced to 15 min |
Adjustable Limiter | Wear-resistant alloy shims (0.1–2.0 mm) | Positioning accuracy maintained at ±0.1 mm |
The dynamic positioning system enables real-time clearance adjustment through shim replacement:
$$ C_{adj} = \sum_{i=1}^{n} (t_i – \Delta w_i) $$
Where Cadj is optimized clearance (mm), ti is initial shim thickness, and Δwi is wear compensation value.
Performance Validation
Field testing across 12 engine cylinder block variants demonstrated:
- Fixture universality increased from 38% to 89%
- Grinding rejection rate decreased from 6.7% to 0.9%
- Average service life extended from 300 to 1,200 hours
Technical Breakthroughs
Key innovations in engine cylinder block grinding include:
- Parametric Insert Design: CAD models automatically generate insert geometries based on cylinder block CAD data.
- Wear Compensation Algorithm: Predictive maintenance triggered when:
$$ \frac{\delta_w}{d_c} \geq 0.3 $$
(dc = critical wear threshold) - Multi-variant Compatibility: Single baseplate supports 14 insert configurations through combinatorial positioning.
Industrial Implementation
In mass production environments, the optimized fixture reduces energy consumption per engine cylinder block by 22% through:
$$ E_{saved} = P \cdot t \cdot (1 – \eta_{new}/\eta_{old}) $$
Where P is motor power (kW), t is cycle time (hr), and η represents grinding efficiency.
Conclusion
The modular grinding fixture design establishes a new paradigm for engine cylinder block finishing, achieving 91% reduction in fixture-related scrap costs. Future work will integrate IoT sensors for real-time wear monitoring, further advancing intelligent manufacturing capabilities in foundry operations.