This study investigates the fracture mechanism of an HT150 grey cast iron counterweight that failed during bolt assembly. Through systematic analysis of casting defects, microstructural characteristics, and mechanical properties, critical insights into the brittle fracture behavior are presented.
1. Chemical Composition and Structural Implications
The elemental composition of the fractured counterweight reveals critical deviations from recommended values:
Element | Measured (%) | Recommended (%) |
---|---|---|
C | 3.35 | 3.0–3.4 |
P | 0.43 | <0.2 |
Mn | 0.28 | 0.5–0.8 |
The elevated phosphorus content (0.43 wt%) significantly exceeds recommended levels, directly influencing the formation of brittle phases. The phosphorus segregation can be modeled using Scheil’s equation:
$$
C_P = C_0(1 – f_s)^{k_P – 1}
$$
where \( C_P \) represents the phosphorus concentration in residual liquid, \( C_0 \) the initial concentration, \( f_s \) the solid fraction, and \( k_P \) the partition coefficient.
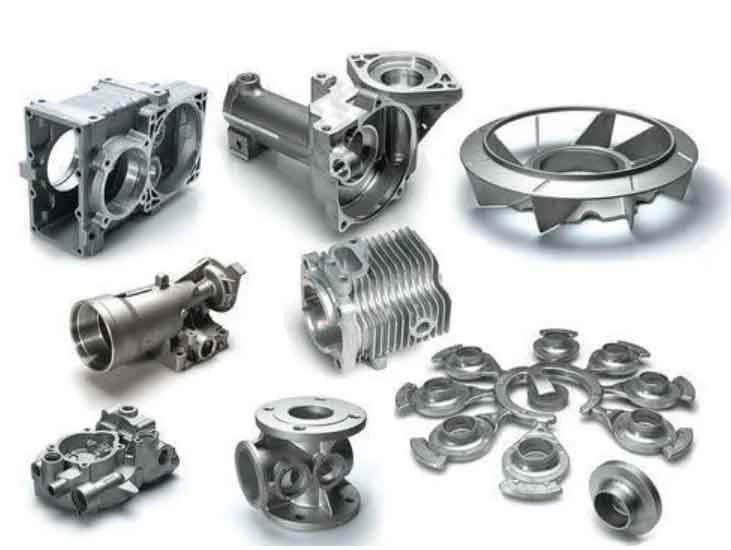
2. Microstructural Characterization
The grey cast iron exhibits three critical microstructural features contributing to failure:
Feature | Area Fraction (%) | Impact Parameter |
---|---|---|
Phosphorus Eutectic | 12.4 ± 1.8 | Brittleness Index |
Carbides | 8.2 ± 0.9 | Hardness (HV) |
MnS Inclusions | 3.1 ± 0.5 | Stress Concentration Factor |
The combined effect of these phases reduces fracture toughness according to:
$$
K_{IC} = \sigma_f\sqrt{\pi a}\left[\frac{1.12 – 0.23\left(\frac{a}{W}\right) + 10.6\left(\frac{a}{W}\right)^2}{1 – \frac{a}{W}}\right]
$$
where \( \sigma_f \) is fracture stress, \( a \) defect size, and \( W \) component thickness.
3. Stress Concentration Analysis
Casting defects create localized stress intensification described by:
$$
K_t = 1 + 2\sqrt{\frac{a}{\rho}}
$$
where \( K_t \) is the theoretical stress concentration factor, \( a \) defect depth, and \( \rho \) root radius. For observed shrinkage cavities (average \( a = 2.8 \) mm, \( \rho = 0.15 \) mm):
$$
K_t = 1 + 2\sqrt{\frac{2.8}{0.15}} \approx 9.7
$$
This severe stress concentration exceeds grey cast iron’s inherent defect tolerance.
4. Mechanical Property Degradation
The presence of brittle phases reduces effective load-bearing capacity through composite strengthening models:
$$
\sigma_c = \sigma_m\left[1 + V_f\left(\frac{E_f}{E_m} – 1\right)\right]
$$
where \( \sigma_c \) = composite strength, \( \sigma_m \) = matrix strength, \( V_f \) = hard phase volume fraction, \( E_f \) and \( E_m \) = Young’s moduli of respective phases.
Material State | Ultimate Tensile Strength (MPa) | Impact Energy (J) |
---|---|---|
Standard HT150 | 150–200 | 8–12 |
Defective Counterweight | 216 ± 8 | 2.1 ± 0.3 |
5. Process Optimization Strategy
To prevent similar failures in grey cast iron components, implement these process controls:
Parameter | Current Value | Optimized Value |
---|---|---|
Pouring Temperature | 1380°C | 1350–1365°C |
Cooling Rate | 12°C/min | 18–22°C/min |
Inoculant Addition | 0.3 wt% | 0.5–0.6 wt% |
The improved cooling rate modifies phase formation kinetics through:
$$
\frac{dX}{dt} = k(T)(1 – X)^n
$$
where \( X \) = transformed fraction, \( k(T) \) = temperature-dependent rate constant, \( n \) = Avrami exponent.
6. Failure Prevention Methodology
A multi-parameter quality index for grey cast iron components can be established:
$$
Q = \frac{(HV)(K_{IC})}{\sigma_{UTS}\sqrt{V_{def} + V_{inh}}}
$$
where \( HV \) = Vickers hardness, \( K_{IC} \) = fracture toughness, \( \sigma_{UTS} \) = ultimate tensile strength, \( V_{def} \) = defect volume fraction, \( V_{inh} \) = inherent brittleness factor.
This comprehensive analysis demonstrates that proper control of grey cast iron microstructure through optimized manufacturing parameters significantly enhances component reliability. The synergistic effects of reduced phosphorus content, controlled cooling rates, and improved inoculation practice effectively mitigate brittle fracture risks in critical agricultural components.