Our company developed 500mm ductile iron valve body castings for Kubota Corporation, Japan. The valve body (770mm × 699mm × 203mm) weighed 360kg with 50mm maximum wall thickness. Material requirements included FCD45 (QT450-10 equivalent) with tensile strength σb > 450MPa, yield strength σ0.2 > 310MPa, elongation δ > 10%, hardness 143-217HB, ferritic matrix with <10% pearlite, and graphite spheroidization > Grade 3 per JIS standards. Surface finish required 140S roughness, strict dimensional tolerances, and internal soundness verified by ultrasonic testing.
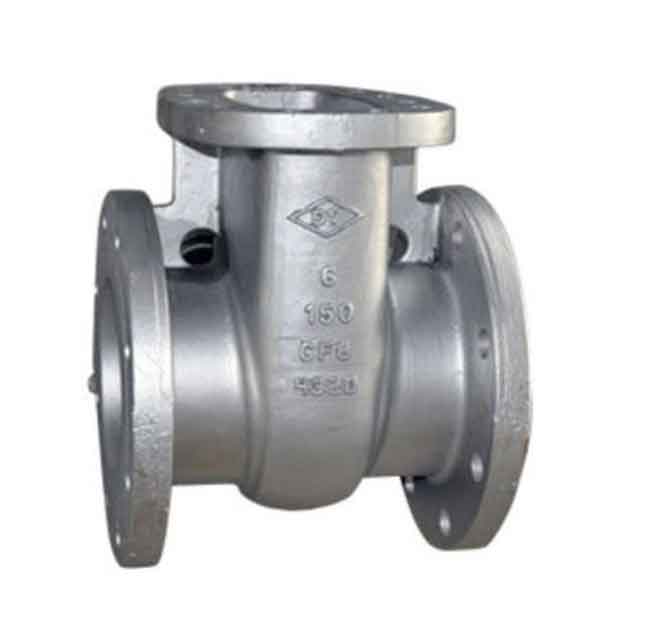
Casting Process Design
The valve body casting used resin sand molding with vertical pouring and middle parting. Risers were eliminated through controlled cooling, with 75mm holes reinforced using steel rods to accelerate solidification and prevent shrinkage defects. Overflow risers minimized slag inclusions near 130mm holes.
The gating system was calculated based on total metal weight (G) including 18% allowance for gating/risers:
$$ G = 300 \text{kg} \times 1.18 = 354 \text{kg} \approx 360 \text{kg} $$
Pouring time (t) was determined using empirical coefficient S1=0.85 and average wall thickness δ=21mm:
$$ t = S_1 \sqrt[3]{\delta G} = 0.85 \times \sqrt[3]{21 \times 360} = 16.68\text{s} \approx 16\text{s} $$
Effective sprue height (Hp) calculation:
$$ H_p = H_0 – \frac{P^2}{2C} = 72 – \frac{63^2}{2 \times 69.9} = 43.61\text{cm} $$
Minimum choke area (∑A直) with flow coefficient μ=0.48:
$$ \sum A_{\text{直}} = \frac{G}{0.31 t \mu \sqrt{H_p}} = \frac{360}{0.31 \times 16 \times 0.48 \times \sqrt{43.61}} = 22.9\text{cm}^2 $$
Gating ratio optimization:
$$ \sum A_{\text{内}} : \sum A_{\text{横}} : \sum A_{\text{直}} = 1 : 1.65 : 1.2 $$
Chemical Composition Control
Target chemistry ensured mechanical properties while minimizing segregation risks:
Element | Target (wt%) | Control Function |
---|---|---|
C | 3.5–3.7 | Graphitization, fluidity |
Si | 2.4–2.8 | Ferrite promotion |
Mn | <0.4 | Pearlite suppression |
P | <0.06 | Reduced brittleness |
S | <0.02 | Nodularity assurance |
Mg | 0.03–0.06 | Nodularization |
RE | <0.05 | Oxide control |
Metallurgical Processing
Melting occurred in 1.5-ton medium-frequency induction furnaces using Benxi pig iron (80%) and low-carbon steel scrap (20%). Key processes included:
Refining: Superheating to 1500–1510°C for impurity removal.
Desulfurization: Two-stage Na2CO3 treatment:
$$ \text{Stage 1: } 0.5\% \text{ at } 1440-1460^\circ\text{C (ladle pre-treatment)} $$
$$ \text{Stage 2: } 0.5\% \text{ during Mg-treatment} $$
Nodularization: T-1 alloy (8.2%Mg, 5%RE, 40.1%Si) addition at 1.6–1.8%.
Inoculation: Multi-stage 75%FeSi treatment:
Stage | Addition (%) | Method |
---|---|---|
Primary | 0.3 | Ladle bottom |
Stream | 0.5 | During pouring |
Floating | 0.2 | Post-treatment |
Instant | 0.1 | Gating system |
Alloying: Bismuth additions countered fading in heavy sections.
Processing temperatures:
$$ \text{Treatment: } 1410-1430^\circ\text{C} \quad \text{Pouring: } 1320-1340^\circ\text{C} $$
Production Results
Over 1,000 valve body castings met JIS specifications:
Sample | Chemistry (wt%) | Mechanical Properties | Microstructure | ||||||||||
---|---|---|---|---|---|---|---|---|---|---|---|---|---|
C | Si | Mn | P | S | ΣRE | Mg | σb (MPa) | δ (%) | HB | Graphite | Pearlite (%) | Nodularity | |
1 | 3.65 | 2.56 | 0.39 | 0.035 | 0.011 | 0.035 | 0.045 | 466 | 19 | 191 | 6 | 10-15 | 3 |
2 | 3.67 | 2.68 | 0.41 | 0.034 | 0.018 | 0.043 | 0.045 | 472 | 18 | 164 | 6 | 10 | 2-3 |
3 | 3.53 | 2.64 | 0.37 | 0.037 | 0.016 | 0.034 | 0.054 | 465 | 20 | 161 | 6 | 5 | 3 |
4 | 3.62 | 2.67 | 0.38 | 0.040 | 0.013 | 0.029 | 0.039 | 459 | 18.5 | 168 | 6 | 5 | 2-3 |
5 | 3.64 | 2.61 | 0.39 | 0.040 | 0.009 | 0.031 | 0.042 | 461 | 17 | 173 | 6 | 8 | 3 |
Technical Challenges and Solutions
Initial trials showed nodularity degradation in casting bodies (Grade 5) despite acceptable test coupons (Grade 2-3). Analysis identified:
Causes:
$$ \text{Fading} \propto \frac{\text{CE} \times T_{\text{pour}}}{\text{Cooling rate}} $$
Where high carbon equivalent (CE=4.6), elevated pouring temperatures (1370°C), and slow solidification in thick sections accelerated fading. Excessive RE/Mg increased surface slag (2-5mm).
Corrective Actions:
- Reduced CE from 4.6 to 4.2–4.4 via increased steel scrap (20%→30%)
- Lowered pouring temperature: 1370°C → 1320–1340°C
- Enhanced desulfurization: Ladle pre-heating optimization
- Implemented gating inoculation: Reduced graphite degeneration
These adjustments achieved consistent Grade 2-3 nodularity throughout valve body castings, meeting all Kubota specifications. The success demonstrates that rigorous process control enables production of heavy-section ductile iron valve body castings with high reliability.