Manufacturing complex turbocharger shells presents significant challenges due to intricate thin-walled structures, multi-layer geometries, low-volume production, and diverse product specifications. Traditional casting methods struggle with dimensional inaccuracies, surface defects, and consistently high rejection rates. To overcome these limitations, our foundry implemented Three-Dimensional Printing and Gluing (3DP) technology in 2017, fundamentally transforming our approach to shell casting production.
3DP Technical Fundamentals
3DP, alternatively termed Binder Jetting or Inkjet Powder Printing, constructs components through selective adhesive bonding rather than thermal fusion. The sequential operation involves:
- A recoater deposits uniform sand layers (thickness: 300-500 μm)
- Precision printheads deposit binder resin following digital patterns
- The build platform lowers incrementally after each layer
- Unbound powder supports complex geometries during printing
- Post-processing removes excess powder mechanically
The binder-powder interaction follows the adhesion model:
$$F_{adhesion} = \frac{\gamma_{binder} \cdot \cos\theta \cdot A}{\delta}$$
Where \(\gamma_{binder}\) is binder surface tension, \(\theta\) the contact angle, \(A\) the contact area, and \(\delta\) the intermolecular distance. This mechanism enables:
- 60-80% faster build rates than laser-based systems
- Zero support structure requirements
- Cost-efficient material utilization
- Internal complexity accommodation
Implementation in Shell Casting Production
Our production workflow integrates computational design with additive manufacturing:
- Digital mold design optimized for thermal dynamics
- Solidification simulation minimizing shrinkage defects
- Virtual assembly validation
- 3DP sand mold fabrication
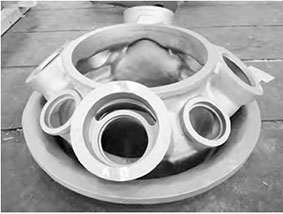
- Automated mold handling and assembly
- Controlled pouring process
- Precision shell casting extraction
Thermal simulation accuracy exceeds 92% when validated against actual castings, governed by Fourier’s heat equation:
$$\frac{\partial T}{\partial t} = \alpha \left( \frac{\partial^2 T}{\partial x^2} + \frac{\partial^2 T}{\partial y^2} + \frac{\partial^2 T}{\partial z^2} \right)$$
Where \(T\) is temperature distribution, \(t\) time, and \(\alpha\) thermal diffusivity.
Comparative Analysis: 3DP vs Traditional Shell Casting
Production efficiency transformation:
Parameter | Traditional Casting | 3DP Shell Casting | Improvement |
---|---|---|---|
Development Cycle | 35 days | 5 days | 85% reduction |
Core Components | 21 individual cores | Monolithic mold | 100% consolidation |
Dimensional Tolerance | CT10-CT13 | CT8-CT11 | 2-grade improvement |
Surface Roughness (Ra) | 50 μm | 25 μm | 50% reduction |
Labor Intensity | High physical demand | Automated operation | 70% reduction |
Dimensional precision enhancement follows the statistical process control model:
$$\sigma_{total} = \sqrt{ \sigma_{tooling}^2 + \sigma_{process}^2 + \sigma_{handling}^2 }$$
Where 3DP eliminates \(\sigma_{tooling}\) and minimizes \(\sigma_{handling}\) through digital integration.
Economic and Quality Advantages
Material consumption comparison:
Material | Traditional (%) | 3DP (%) | Cost Impact |
---|---|---|---|
Resin Binder | 1.2-1.4 | 1.5-2.0 | +36% unit cost |
Catalyst | 40-50 | 15-20 | -62% consumption |
Base Sand | 100 | 100 | +78% unit cost |
Coatings | Standard | Optional | -40% usage |
Comprehensive cost analysis for 500 shell castings:
Cost Factor | Traditional ($/unit) | 3DP ($/unit) |
---|---|---|
Tooling Investment | 12.00 | 0.00 |
Material Consumption | 14.20 | 15.50 |
Surface Treatment | 0.50 | 0.25 |
Labor Operations | 4.50 | 1.50 |
Rejection Losses | 8.00 | 2.00 |
Total Cost | 39.20 | 19.25 |
The quality-cost relationship demonstrates:
$$C_{effective} = C_{production} \cdot \frac{1}{1 – R}$$
Where \(R\) represents rejection rate. With 3DP reducing rejection by 15%, effective costs decrease despite marginally higher material expenses.
Technical Superiority in Shell Casting
3DP delivers measurable advantages in critical casting metrics:
- Dimensional Precision: Achieves ±0.5mm mold accuracy yielding ≤1mm wall thickness variation
- Surface Integrity: Maintains consistent Ra25 surfaces without dressing operations
- Geometric Freedom: Enables consolidation of multiple components into unitary shell castings
- Process Stability: Reduces human-dependent variables through digital continuity
The surface quality enhancement correlates with binder penetration depth:
$$d_p = \sqrt{\frac{\gamma \cdot r \cdot \cos\theta}{2\eta}} \cdot \sqrt{t}$$
Where \(d_p\) is penetration depth, \(r\) pore radius, \(\eta\) viscosity, and \(t\) time.
Industrial Transformation and Future Development
3DP enables the transition toward green intelligent foundries through:
- Elimination of high-decibel core shooting machines
- Removal of airborne particulate emissions
- Energy consumption reduction via direct digital manufacturing
- Workforce upskilling toward technical supervision
The technology adoption curve follows the logistic growth model:
$$A(t) = \frac{K}{1 + e^{-r(t-t_0)}}$$
Where \(A(t)\) is adoption rate, \(K\) carrying capacity, \(r\) intrinsic growth rate, and \(t_0\) inflection point.
Operational Impact and Validation
Since implementation, our facility has:
- Developed 75 distinct turbocharger shell castings
- Transitioned 25 designs to serial production
- Reduced development iterations by 80%
- Improved first-pass yield by 15% across all shell casting products
- Achieved 98% dimensional conformity on complex geometries
Production scalability follows the experience curve:
$$C_n = C_1 \cdot n^{-b}$$
Where \(C_n\) is unit cost of the \(n^{th}\) unit, \(C_1\) initial unit cost, and \(b\) the experience exponent.
Conclusion
3DP technology fundamentally transforms complex shell casting manufacturing by eliminating tooling constraints while enhancing geometric capability. The direct digital approach delivers superior dimensional control, surface quality, and production flexibility compared to traditional methods. Though material costs remain marginally higher, significant reductions in tooling investment, labor requirements, and rejection losses yield compelling economic advantages. As additive manufacturing systems evolve toward higher productivity and material efficiency, 3DP will increasingly dominate specialized shell casting production where complexity, precision, and rapid iteration provide competitive differentiation. The technology establishes the foundation for sustainable, human-centric foundry operations aligned with Industry 4.0 principles.