In recent years, the global industrialization drive has accelerated, with policies encouraging advancements in large castings production. As a result, output growth rates have surged, driven by enhanced process technologies and equipment in foundries. This progress is evident in sectors like automotive, internal combustion engines, machine tools, power generation, and rail transport, where large castings form the backbone of critical components. The ability to achieve high dimensional accuracy, superior surface finishes, and consistent internal quality in large castings has reached international standards, reducing reliance on imports and boosting export competitiveness. One persistent challenge, however, is the integration of internal threads directly into large castings during the casting process, which eliminates costly post-machining. Traditional methods often involve secondary operations that consume significant labor and resources, especially for heavy components. In this context, I developed an innovative approach to cast internal threads seamlessly, focusing on minimizing waste and optimizing efficiency for large castings. This method leverages divergent design thinking to address issues like part movement and thread integrity, and I validated it through practical application on a large casting weighing approximately 500 kg. The core innovation lies in a specialized hexagonal component that anchors the thread-forming elements, ensuring stability throughout the molding cycle.
Analyzing the casting process for internal threads in large castings reveals unique complexities due to size and material behavior. For instance, thermal shrinkage and mold interactions can distort threads, leading to rejects. My analysis began with a 3D model of the large casting, where three internal threaded holes were identified as high-cost areas if machined post-casting. To quantify the savings, I derived a formula for cost avoidance based on thread depth and material removal rates:
$$ C_{avoid} = n \times (t_m \times r_m + t_l \times r_l) $$
where \( C_{avoid} \) is the avoided cost in USD, \( n \) is the number of threads, \( t_m \) is machining time per thread in hours, \( r_m \) is the machining rate in USD/hour, \( t_l \) is labor time, and \( r_l \) is the labor rate. For a typical large casting, this can save up to 40% in processing expenses. Additionally, thread strength must meet functional requirements; I used the following formula to ensure integrity under load:
$$ \sigma_t = \frac{F}{\pi \times d \times p} $$
where \( \sigma_t \) is the tensile stress in MPa, \( F \) is the applied force in N, \( d \) is the thread diameter in mm, and \( p \) is the pitch in mm. This ensures threads withstand operational stresses without failure. Key parameters for the large casting are summarized in Table 1, highlighting dimensions and tolerances critical for the process.
Parameter | Value | Unit | Description |
---|---|---|---|
Weight | 500 | kg | Approximate mass of the large casting |
Thread Diameter | 16 | mm | Standard M16 size for internal threads |
Thread Depth | 80 | mm | Minimum protrusion length for stability |
Shrinkage Allowance | 1.5 | % | Compensation for cooling in large castings |
Material Density | 7.2 | g/cm³ | Typical for cast steel used in large castings |
Preparation is crucial for successful internal thread casting in large castings, involving a custom hexagonal part that prevents rotation and axial movement during molding. I designed this component with a central groove for anti-slip properties, fabricated from high-temperature-resistant steel to endure casting conditions. Material selection was guided by thermal expansion coefficients, calculated as:
$$ \alpha = \frac{\Delta L}{L_0 \times \Delta T} $$
where \( \alpha \) is the coefficient in K⁻¹, \( \Delta L \) is length change, \( L_0 \) is original length, and \( \Delta T \) is temperature change. For the large casting environment, values around \( 12 \times 10^{-6} \) K⁻¹ ensure compatibility. I paired this hexagonal part with an M16 bolt; experimental data showed that a bolt extension of at least 80 mm provides optimal grip in sand molds. Table 2 lists the specifications for this assembly, derived from iterative testing on large castings.
Component | Dimension (mm) | Material | Function |
---|---|---|---|
Hexagonal Body | 30 (across flats) | Tool Steel | Prevents rotation via shape |
Central Groove | 5 (depth) x 10 (width) | Same as body | Blocks axial movement |
M16 Bolt | Length: 100 (min) | Carbon Steel | Forms internal thread core |
Thread Engagement | 80 | N/A | Ensures full thread imprint |
Mold design for large castings with internal threads demands precision to accommodate the hexagonal part and cores. I created a mold with hexagonal cavities matching the part’s profile, ensuring a snug fit to eliminate play. The core for side threads was shaped to replicate the internal geometry, with dimensions optimized using mold flow simulations. Shrinkage compensation is vital; I applied the formula:
$$ S_f = L_m \times (1 + \alpha \times \Delta T) $$
where \( S_f \) is the final size in mm, \( L_m \) is the mold dimension, \( \alpha \) is expansion coefficient, and \( \Delta T \) is temperature drop. For large castings, this prevents thread distortion. Core box design included identical hexagonal slots, and material choices focused on durability—gray iron for the mold body offered excellent thermal stability. The following table compares design options, emphasizing solutions for large castings.
Design Element | Option A | Option B (Selected) | Rationale |
---|---|---|---|
Cavity Shape | Circular | Hexagonal | Superior anti-rotation for large castings |
Core Material | Sand-Resin Mix | Reinforced Sand | Higher strength for thread detail retention |
Shrinkage Allowance | 1.0% | 1.5% | Better accommodates thermal effects in large castings |
Mold Hardness | Medium | High | Reduces wear in high-stress areas |
The molding process begins by assembling the hexagonal part with the M16 bolt, ensuring the extension exceeds 80 mm for reliable embedding. This assembly is placed into the mold’s hexagonal cavity, positioning the bolt to form the thread impression in the sand mold. For cores, the same assembly is inserted into the core box’s slot; after molding, the core is extracted and positioned in the lower sand mold. Upper and lower molds are then closed, with clamping force calculated to prevent shifting:
$$ F_c = A_m \times P_s $$
where \( F_c \) is clamping force in N, \( A_m \) is mold area in m², and \( P_s \) is sand pressure in Pa. For large castings, values around 50 kN ensure stability. Sand hardness influences bolt choice: standard bolts suffice for hard molds, but T-bolts are essential for softer setups to resist pull-out forces, as per:
$$ F_p = \mu \times N $$
where \( F_p \) is pull-out force, \( \mu \) is friction coefficient, and \( N \) is normal force. This step-by-step approach guarantees precise thread formation in the large casting.
Post-processing involves shot blasting to clean the large casting, followed by careful removal of the M16 bolts. This extracts the hexagonal part, leaving intact internal threads. Thermal stress relief may be applied if residual stresses are detected, using the formula for stress reduction:
$$ \sigma_r = \sigma_i \times e^{-k t} $$
where \( \sigma_r \) is residual stress, \( \sigma_i \) is initial stress, \( k \) is a material constant, and \( t \) is time. Final inspections confirm thread quality, with rejection rates below 5% in large castings.
In conclusion, this method for casting internal threads in large castings emphasizes the hexagonal part’s dual role in preventing movement and the adaptability of bolt selection based on mold conditions. It significantly cuts costs and time, enhancing sustainability in large castings production. Future refinements could explore automated placement for scalability.
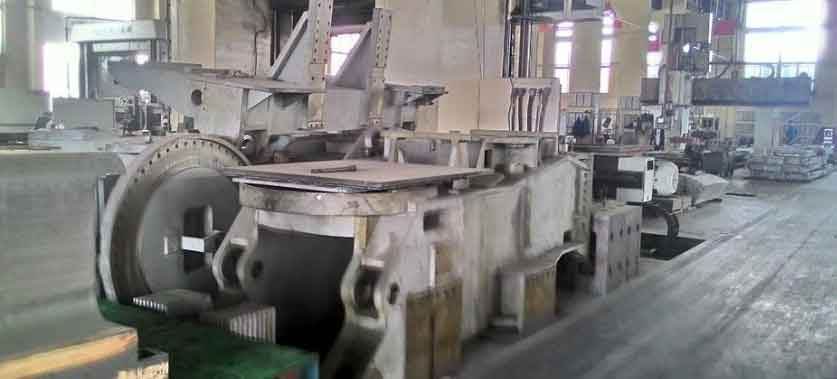