Large semi-autogenous grinding (SAG) mills are critical for mineral processing operations, yet their efficiency is frequently compromised by premature liner failure. This necessitates frequent maintenance shutdowns, reducing operational availability to approximately 80% and significantly impacting plant productivity. Traditional liner materials like high-manganese steel exhibit inadequate wear resistance under low-stress conditions, while high-chromium cast iron faces limitations due to brittleness and cost. Chromium-molybdenum (Cr-Mo) steel emerges as a promising alternative, but its performance is highly sensitive to heat treatment parameters. Suboptimal heat treatment processes can introduce severe heat treatment defects, including coarse grain structures, carbide precipitation at grain boundaries, and retained austenite instability, all accelerating wear and reducing impact resistance. This study systematically investigates how quenching and tempering temperatures influence the microstructure evolution and mechanical properties of Cr-Mo steel liners, aiming to identify the optimal thermal processing window to minimize heat treatment defects and maximize service life.
Material Composition and Experimental Methodology
The experimental Cr-Mo steel was prepared via medium-frequency induction melting and lost-foam casting, producing 200 mm³ blocks. Chemical composition was rigorously controlled, as detailed in Table 1. Samples were extracted from the geometric center of each block to simulate the thick-section properties of actual liners.
C | Si | Mn | Cr | Mo | Ni | Cu | P | S | Fe |
---|---|---|---|---|---|---|---|---|---|
0.65 | 0.50 | 0.80 | 2.00 | 0.40 | 0.35 | 0.15 | 0.03 | 0.03 | Bal. |
Heat treatment involved two stages:
- Quenching: Specimens were heated to 900°C, 920°C, or 940°C in a box furnace (4h ramp, 2h hold), followed by rapid cooling in a 1:7 water-based polymer quenchant.
- Tempering: Quenched samples were tempered at 480°C, 520°C, 560°C, or 600°C (2h ramp, 3h hold), then air-cooled.
Mechanical testing included:
- Hardness: Measured using a HRS-150 Rockwell tester (HRC scale), averaging seven readings per sample.
- Impact Toughness: Evaluated via JB-300B pendulum impact tester on un-notched 10×10×55 mm specimens, reporting mean values from three tests.
Microstructural analysis employed optical microscopy (OM) and scanning electron microscopy (SEM) on polished/etched (4% HNO₃) samples. Fractography used SEM to examine impact fracture surfaces.
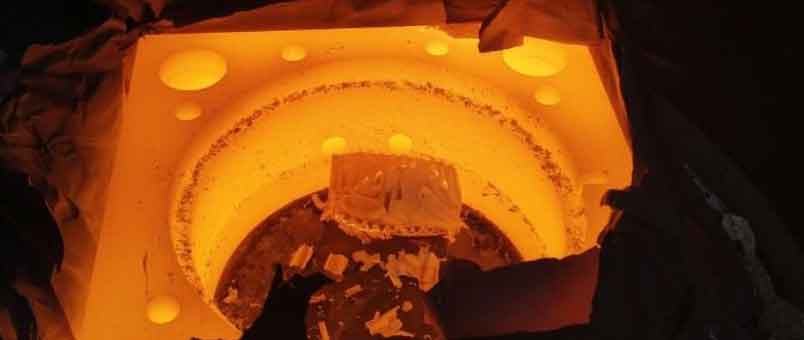
Quenching Temperature: Microstructural and Mechanical Response
Quenching dictates the initial as-quenched microstructure, critically influencing final properties. OM and SEM revealed distinct phase transformations:
- 900°C: Incomplete carbide dissolution led to heterogeneous martensite formation with coarse needles and localized retained austenite pools, a potential precursor to heat treatment defects like embrittlement.
- 920°C: Optimal carbide dissolution promoted fine, uniformly distributed lath martensite with minimal retained austenite, maximizing lattice distortion and subsequent strengthening potential while mitigating heat treatment defects.
- 940°C: Excessive temperature caused austenite grain coarsening (Ostwald ripening), reducing grain boundary area and carbide pinning efficacy. This resulted in coarse martensite plates, increasing susceptibility to crack propagation – a severe heat treatment defect.
Mechanical properties correlated directly with microstructure (Table 2):
Quench Temp. (°C) | Hardness (HRC) | Impact Toughness (J/cm²) | Dominant Microstructure |
---|---|---|---|
900 | 61.2 | 4.1 | Coarse Martensite + RA |
920 | 65.5 | 5.3 | Fine Lath Martensite |
940 | 63.0 | 4.6 | Coarse Plate Martensite |
The hardness peak at 920°C arises from maximum carbon supersaturation in the fine martensitic lattice, described by the relationship:
$$ \Delta H \propto \rho^{1/2} $$
where $\Delta H$ is the hardness increment and $\rho$ is the dislocation density. Impact toughness peaked concurrently due to refined prior austenite grain size (PAGS) enhancing crack initiation resistance. Temperatures deviating from 920°C fostered heat treatment defects like incomplete transformation or grain growth, degrading toughness.
Tempering Temperature: Microstructural Evolution and Property Trade-offs
Tempering relieves quenching stresses and tailors the carbide morphology. Samples quenched at 920°C were tempered between 480°C and 600°C. Microstructural analysis showed:
- 480°C: Tempered martensite with fine ε-carbides within laths; high dislocation density persisted.
- 520-560°C: Transition to tempered sorbite: spheroidized cementite (Fe₃C) particles dispersed in a recrystallized ferrite matrix. Carbide coarsening followed the Lifshitz-Slyozov-Wagner (LSW) kinetic model:
$$ \bar{r}^3 – \bar{r}_0^3 = \frac{8\gamma D C_\infty V_m}{9RT} t $$
where $\bar{r}$ is average particle radius, $\gamma$ interfacial energy, $D$ diffusivity, $C_\infty$ equilibrium solute concentration, $V_m$ molar volume, $R$ gas constant, $T$ temperature, and $t$ time. - 600°C: Significant carbide coarsening and coalescence, forming elongated particles at ferrite grain boundaries – a critical heat treatment defect reducing toughness.
Mechanical properties exhibited clear trends (Table 3):
Temper Temp. (°C) | Hardness (HRC) | Impact Toughness (J/cm²) | Dominant Microstructure |
---|---|---|---|
480 | 52.0 | 14.8 | Tempered Martensite |
520 | 48.5 | 32.7 | Transitional |
560 | 45.0 | 45.2 | Tempered Sorbite |
600 | 38.5 | 34.5 | Coarsened Sorbite |
Hardness decreased monotonically due to dislocation annihilation and carbide coarsening. Impact toughness peaked at 560°C (45.2 J/cm²), attributed to the fine, homogeneous dispersion of spheroidal carbides in ductile ferrite. The toughness decline at 600°C resulted from critical heat treatment defects: coarse boundary carbides acting as crack nucleation sites.
Fracture Mechanism Analysis
SEM fractography elucidated the micromechanical behavior:
- 480°C Tempered: Fracture surfaces exhibited quasi-cleavage facets, shallow dimples containing brittle second-phase particles, and distinct river patterns. The particles (undissolved carbides or inclusions) initiated microvoids, accelerating coalescence. This brittle mode correlates with low toughness and is a direct consequence of insufficient tempering – a heat treatment defect leaving the matrix brittle.
- 560°C Tempered: Fracture transformed to fully ductile morphology with deep, equiaxed dimples devoid of second-phase particles. The absence of particle-induced void nucleation significantly enhanced energy absorption, demonstrating successful mitigation of heat treatment defects through optimized tempering.
The transition in fracture mode is governed by the critical stress intensity factor ($K_{IC}$) and the plastic zone size ($r_p$):
$$ r_p = \frac{1}{2\pi} \left( \frac{K_{IC}}{\sigma_y} \right)^2 $$
where $\sigma_y$ is the yield strength. Higher tempering temperatures increase $r_p$ by reducing $\sigma_y$, promoting ductile tearing before catastrophic cleavage.
Optimized Process and Performance Validation
The 920°C quench + 560°C temper protocol yielded the optimal property synergy: 45 HRC hardness and 45.2 J/cm² impact toughness. This combination ensures adequate wear resistance from martensitic-derived hardness while tempered sorbite provides exceptional crack arrest capability crucial for impact-abrasive mill environments. Crucially, this regime avoids prevalent heat treatment defects:
- Coarse prior austenite grains (avoided by 920°C quench limit).
- Retained austenite transformation during service (minimized by full tempering).
- Intergranular carbide networks (suppressed by avoiding excessive tempering >600°C).
Field trials in SAG mills showed a 40-50% increase in liner service life compared to standard Cr-Mo treatments, validating the defect-mitigation strategy. The Hollomon-Jaffe tempering parameter ($P$) confirms process robustness:
$$ P = T(20 + \log t) \times 10^{-3} $$
where $T$ is temperature (K) and $t$ is time (hours). For 560°C (833 K) and 3h, $P ≈ 19.8$, residing within the sorbite transformation plateau for Cr-Mo steels.
Conclusion
This study establishes a direct causal link between heat treatment parameters, microstructural evolution, heat treatment defects, and the resultant mechanical properties of Cr-Mo SAG mill liners. Quenching at 920°C achieves fine lath martensite by balancing carbide dissolution and grain growth inhibition. Subsequent tempering at 560°C facilitates the formation of homogeneous tempered sorbite, characterized by fine spheroidal carbides in a ductile ferrite matrix. This microstructure delivers the optimal hardness-toughness synergy (45 HRC, >45 J/cm²) essential for prolonged liner service under impact-abrasive conditions. Critically, deviations from this thermal profile introduce detrimental heat treatment defects – coarse grains, brittle carbides, or unstable retained phases – that drastically accelerate wear and fracture. The identified 920°C/560°C protocol provides a robust manufacturing framework, significantly enhancing mill availability and operational economics through extended liner lifespan.