Bucket teeth represent the most severely worn components in mining excavation operations due to enduring impact loads and friction from ore and rock. This results in wear, scratching, or fracture. As high-consumption, frequently replaced components, rising demand substantially increases operational costs. Effective control of bucket tooth consumption thus becomes critical for cost management. By analyzing failure modes, structural design, materials, manufacturing processes, and surface treatments, this research establishes a foundation for domestic bucket tooth selection in projects like Myanmar’s Letpadaung Mining Project.
Functional Requirements and Failure Modes of Bucket Teeth
Bucket teeth serve two primary functions: reducing excavation resistance (approximately 20% lower than toothless buckets) and protecting the bucket’s front arm by absorbing wear. At Letpadaung Copper Mine, diverse geological conditions—surface soil, weathered rock, hard rock, and ore—impose varying loads. Extremely hard volcanic rock significantly increases stress, demanding high load-bearing capacity and wear resistance.
Traditional domestic bucket teeth predominantly use Hadfield manganese steel (11-14% Mn). Under high-impact loads, it hardens via deformation-induced martensite transformation, achieving surface hardness of HB500-800. However, under low-impact conditions (e.g., sandy soil), insufficient hardening leaves hardness at HB300-400, accelerating wear. Furthermore, work-hardened manganese steel exhibits reduced yield strength, increasing fracture risk.
Failure distribution analysis reveals:
$$\text{Wear Failure} \approx 90-95\%, \quad \text{Fracture/Deformation} \approx 5-10\%, \quad \text{Corrosion} < 1\%$$
Optimization must prioritize wear resistance while maintaining structural integrity.
Material Advancements for Enhanced Performance
Material selection must align with operational stresses. Key developments include:
Material Class | Composition | Optimal Use Case | Advantages/Limitations |
---|---|---|---|
High-Mn Alloy Steel | Mn + Cr/Mo/V/Ti | High-impact ore/rock | Improved toughness & hardness; Cost-effective but prone to fracture under extreme loads |
Ultra-High-Mn Steel | Mn15-Mn25 alloys | Volcanic/granitic rock | Superior work-hardening depth (20mm+); 3-4× lifespan vs. standard Mn steel in hard rock |
Low-Carbon Alloy Steel | Micro-alloyed martensite | Soil/weathered rock | High hardness (HB550-650); Low cost; Unsuitable for high-impact loading |
For acidic environments (e.g., Letpadaung’s pit water), corrosion-resistant alloys require further development. Material choice follows:
$$\text{Material Selection} = f(\sigma_{\text{impact}}, \text{Hardness}_{\text{rock}}, \text{Corrosion}_{\text{env}})$$
where $\sigma_{\text{impact}}$ is impact stress, $\text{Hardness}_{\text{rock}}$ is rock abrasiveness, and $\text{Corrosion}_{\text{env}}$ is chemical exposure.
Structural Optimization and Shock Absorption
Premature fracture often originates from poor stress distribution. Finite element analysis (FEA)-guided design minimizes stress concentration. A critical innovation is integrating silicone-rubber damping sleeves between the adapter and bucket tooth:
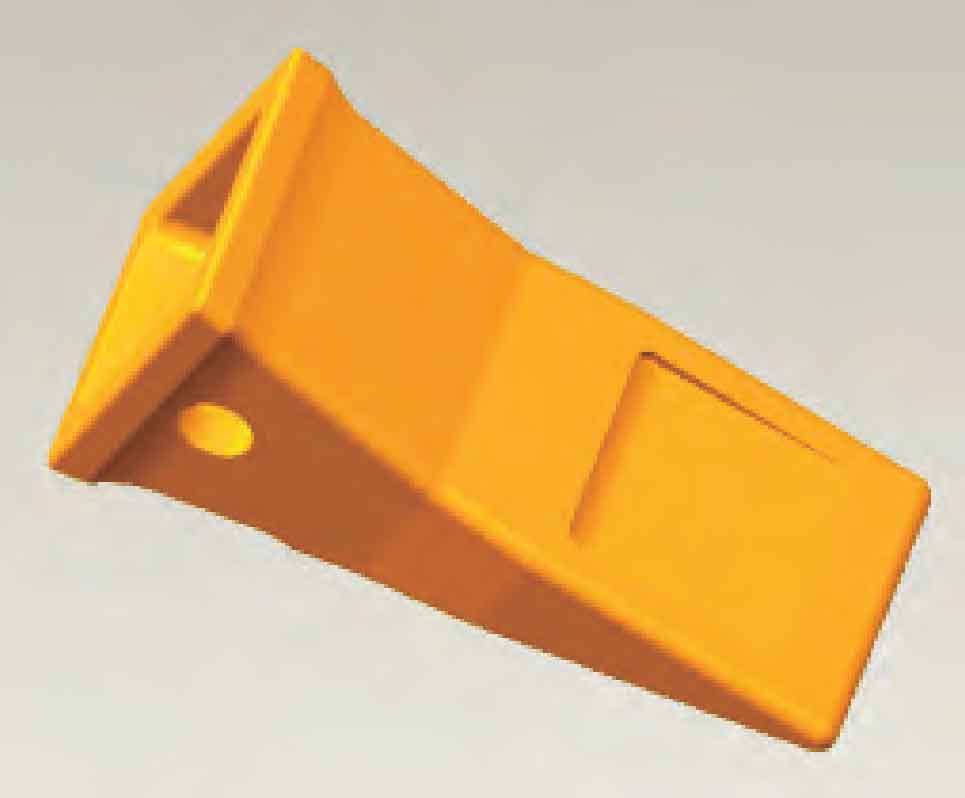
These sleeves absorb shock loads ($F_{\text{shock}}$), reducing peak stress transmission:
$$ \Delta \sigma_{\text{peak}} = k \cdot \mu \cdot F_{\text{shock}} $$
where $k$ is the damping coefficient and $\mu$ is the friction factor. This extends bucket tooth life by 15-20% and protects hydraulic/electrical systems.
Manufacturing and Surface Engineering
Heat treatment determines microstructural efficacy. For high-Mn steels, water toughening (1050°C–1100°C quenching) refines austenite grains and dissolves carbides. Properly treated teeth exhibit 2× longer service life. Low-carbon steels undergo tempering to balance martensitic hardness and toughness.
Surface enhancements further combat wear:
- Hardfacing: Tungsten carbide or Ni-Cr-Mo alloys applied via submerged arc welding (SAW) increase surface hardness to HRC 60-65.
- Explosive Compaction: Shock waves densify the near-surface layer, improving abrasion resistance.
Wear resistance ($R_w$) scales with coating hardness ($H_c$) and thickness ($t_c$):
$$ R_w \propto H_c \cdot \sqrt{t_c} $$
Implementation at Letpadaung Mine
Domestic bucket teeth (high-Mn alloys) achieved 85-90% of imported equivalents’ lifespan at 40-50% lower cost. Key outcomes:
Metric | Imported Teeth | Domestic Teeth | Improvement |
---|---|---|---|
Cost/Unit | $1,200 | $600 | 50% reduction |
Lead Time | 6 months | 6 weeks | 75% reduction |
Avg. Lifespan (Ore) | 180 hours | 160 hours | 89% of benchmark |
Future work will test ultra-high-Mn steel in volcanic strata and develop acid-resistant alloys for pit corrosion.
Conclusion
Optimizing bucket tooth performance requires integrated material selection, structural design, and surface engineering. Domestic alternatives now offer viable solutions for import substitution, reducing costs and lead times while maintaining reliability. Continuous innovation in alloy development and shock-absorbing technologies will further bridge performance gaps in demanding mining environments.