Isothermal transformation of ductile iron
The specific process of Austempering is as follows: the nodular iron castings are heated to austenitizing temperature and held for a certain time for complete austenitizing treatment rapid quenching into the salt bath furnace, oil bath or flow bed furnace, rapidly cooling to the austenite transformation temperature zone and holding for a certain time air cooling to room temperature. At present, in addition to austempering, ADI can be prepared by continuous cooling quenching and as cast alloying. However, compared with austempering process, the as cast alloying method does not require heat treatment equipment, energy saving, short production cycle and can avoid casting embrittlement, but the amount of alloy elements added is more, the production cost is increased, and the cooling rate is not easy to control, too fast will get martensite, too slow will produce pearlite; although the continuous cooling quenching process is relatively simple, alloy elements However, the microstructure is not stable and easy to form internal stress, so tempering treatment is necessary.
Austempering process of ductile iron
ADI austempering process is shown in Fig. 1. The casting was heated to 870 ~ 980 ℃ and held for about 2 h, so that the matrix was fully austenitized. Then the castings were rapidly cooled to 260 ~ 400 ℃ for 1 ~ 2 h, and then air cooled to room temperature. During isothermal quenching, two phase transformation reactions will occur. In the first reaction, austenite (γ C) is decomposed into acicular ferrite (α b) and high carbon austenite (γ HC)
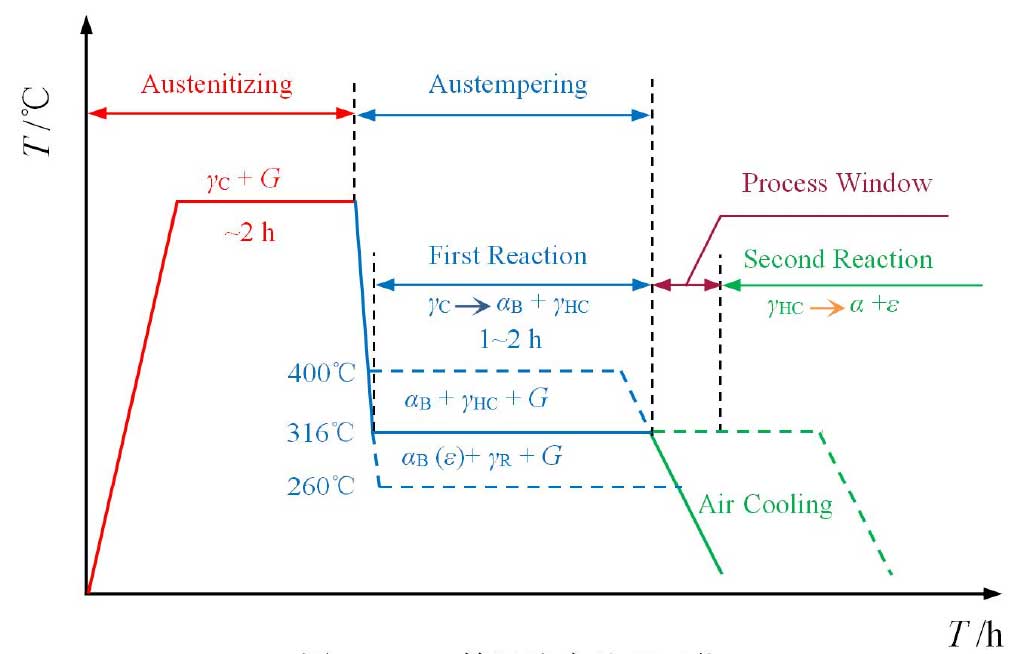
If the casting is kept at the isothermal temperature for a long time, the second adverse reaction will occur, and the high carbon austenite (γ HC) will further decompose into ordinary ferrite (α) and carbide (ε)
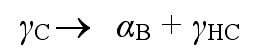
Since the reaction produces carbides, which makes the material brittle, the reaction must be avoided.
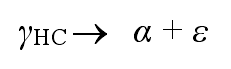
After the completion of the first reaction but before the second reaction, ADI will obtain the optimal performance, which is called the “process window”. The process window can be expanded by the addition of alloying elements, which, when cooled, prevent the decomposition of austenite into pearlite and ferrite. Proper austempering can produce ideal microstructure (high carbon austenite + acicular ferrite + graphite ball) and avoid unnecessary structure (martensite, carbide and pearlite).
The final form of ferrite and carbon is related to the isothermal transformation temperature (TA). When TA < 320 ℃, there may be Fe3C or ε carbides formed in acicular α – crystal of ADI matrix; when TA > 320 ℃, microstructure composed of α + γ HC without carbide is formed in ADI matrix, which is usually called “austenite”. At the same time, the amount of untransformed austenite in ADI matrix is different due to different isothermal transformation temperature and holding time. The increase of the amount of untransformed austenite can accelerate the work hardening rate of ADI, but it can improve the fatigue strength and fracture toughness of ADI.