During pouring, under the action of gravity, the molten metal first enters the cavity through the sprue, enters the runner and ingate, and finally enters the filling process of the axle housing cavity. Figure (a) is the real-time screenshot of the molten metal just filling the runner at the beginning of pouring, and the molten metal enters into the axle housing; the filling ratio of the cavity is 25.3%, and the solidification fraction is 0.0%. Figure (b) reflects the beginning of the flow of molten metal in the axle housing when the molten metal is filling the mold cavity. The filling ratio of the cavity is 30.6%, and the solidification fraction is 30.6% Figure (c) is a screenshot of the middle filling stage of liquid metal, with the cavity filling ratio of 64% and solidification fraction of 4%; and figure (d) of the later stage of liquid metal filling, with the cavity filling ratio of 96.3% and solidification fraction of 12.7%.
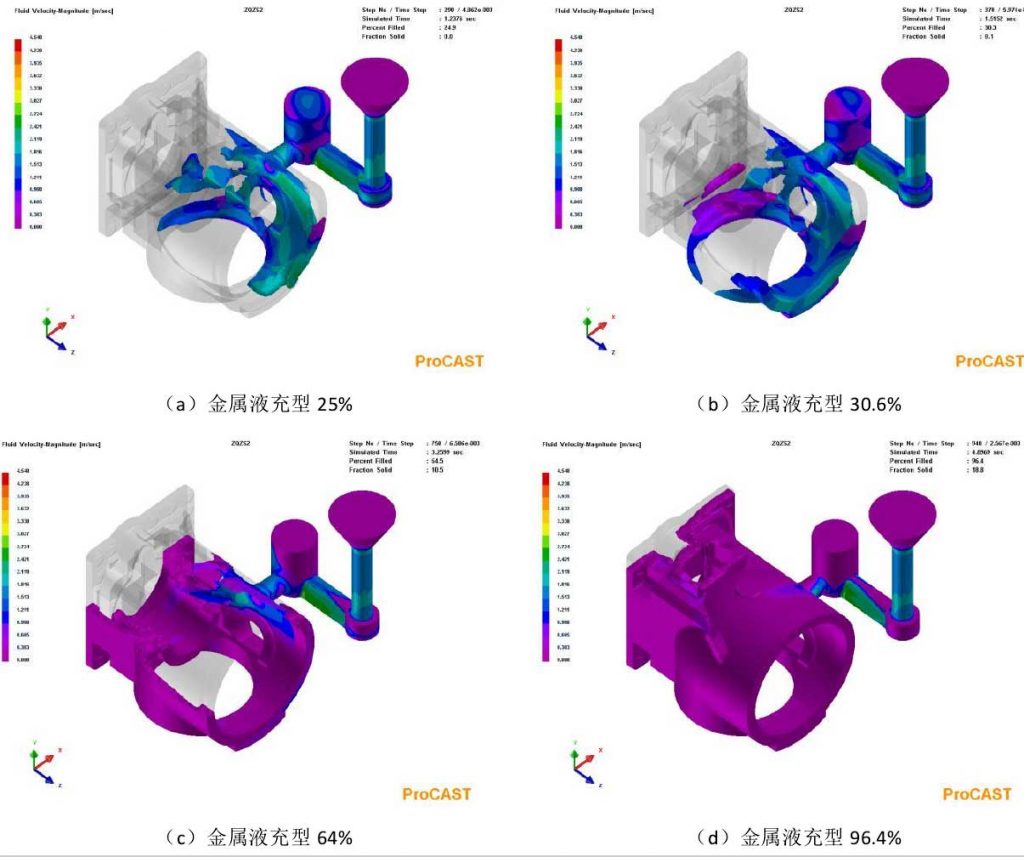
It can be seen from the velocity field shown in the figure (a) and (b) that the flow of molten metal in the whole cavity filling process is very stable, the melt fills the cavity quickly, and there is no cut-off and isolated metal solution. When the cross-sectional area of the runner is smaller than that of the sprue, the molten iron will act as a barrier to the sand during the pouring process, which will not make the molten steel entrain the molding sand, so as not to make the bridge The casting defects such as shrinkage cavity and sand hole are found in the shell, so the scheme is better.