Research on Abrasive Wear Characteristics of Tractor Casting Crawler Plates
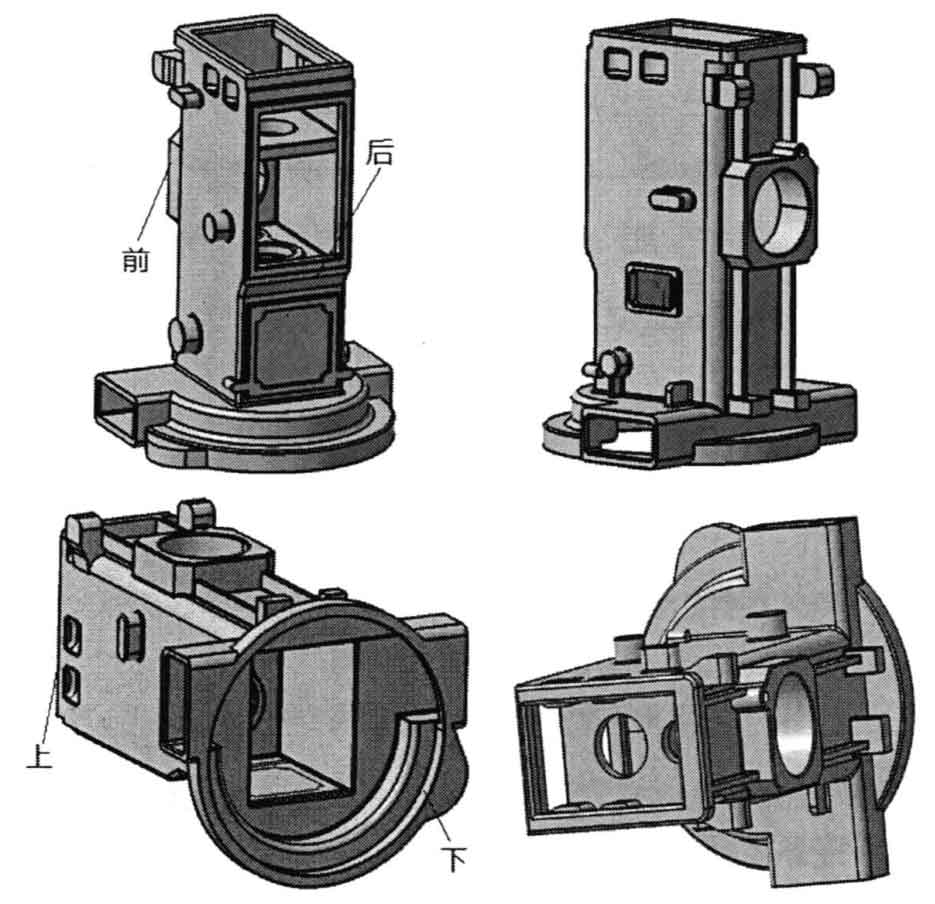
As the most numerous wear part in tractors, casting crawler plates endure extreme working conditions including direct contact with soil/abrasives, impact loads, tensile stresses, and bending moments. Our research systematically compares wear resistance of various tractor casting materials through laboratory and field tests, analyzing failure mechanisms to identify optimal compositions and treatments for extended service life.
Materials and Experimental Methodology
We examined multiple tractor casting materials from major manufacturers, with chemical compositions and heat treatments detailed in Table 1. Laboratory abrasive wear tests employed the Fargo ASTM G65 rubber-wheel apparatus (Figure 1) under controlled parameters:
$$v = 2.4 \text{m/s},\quad P = 130\text{N or }230\text{N},\quad t = 1000\text{rev}$$
$$\text{Relative Wear Resistance } \varepsilon = \frac{\Delta W_{\text{std}}}{\Delta W_{\text{sample}}}$$
Field validation involved 12-month comparative trials across paddy (Guangdong) and dry (Northeast China) fields, measuring thickness loss at critical wear zones. Microstructural analysis used SEM/EDS to characterize wear mechanisms.
Material | C | Mn | S | Si | Heat Treatment | Microstructure |
---|---|---|---|---|---|---|
ZG45Mn | 0.45 | 1.2 | 0.02 | 0.6 | 880°C WQ + 200°C temper | Tempered martensite |
ZG60Mn | 0.60 | 1.1 | 0.01 | 0.7 | 850°C OQ + 180°C temper | Tempered martensite |
High-Mn Steel | 1.2 | 12.5 | 0.03 | 0.8 | 1050°C WQ | Austenite |
Medium-Mn Steel | 0.7 | 6.8 | 0.02 | 0.5 | 950°C salt bath | Austenite + carbide |
Ductile Iron | 3.5 | 0.3 | 0.01 | 2.4 | Austempered 350°C | Bainite + graphite |
Laboratory Wear Test Results
Carbon content critically influenced tractor casting wear resistance. The relationship followed:
$$\varepsilon = 1.8C^{1.7} + 0.6\quad (R^2=0.94)$$
where C is weight percentage carbon. Sulfur content inversely affected durability:
$$\Delta W = 120S^{0.8} + 25\quad (R^2=0.88)$$
Thermal treatment optimization proved essential – excessive tempering temperatures significantly reduced wear resistance:
Tempering Temp (°C) | 200 | 300 | 400 | 500 |
---|---|---|---|---|
Relative Wear Resistance | 1.0 | 0.92 | 0.85 | 0.68 |
Field Performance Analysis
Soil conditions dictated failure modes and material rankings. Paddy fields induced severe corrosion-wear synergy while dry soils caused pure abrasive damage:
Material | Paddy Field Wear (mm) | Dry Field Wear (mm) | Failure Mode |
---|---|---|---|
High-Mn Steel | 4.2±0.3 | 2.1±0.2 | Pin hole elongation |
ZG60Mn | 2.8±0.2 | 1.5±0.1 | Surface abrasion |
Medium-Mn Steel | 2.1±0.2 | 2.3±0.3 | Track collapse |
Ductile Iron | 3.2±0.4 | 1.8±0.2 | Fracture |
Wear Mechanism Characterization
SEM analysis revealed complex damage mechanisms in tractor casting components:
- from soil particle plowing: Groove depth $d_g \propto \tan\theta / H_v$ where θ is particle attack angle
- Corrosion-fatigue pits in paddy fields: Pit density increased 300% versus dry conditions
- Spalling craters at stress-concentration zones: Crater diameter followed $D_c \propto \sigma^{1.5} / K_{IC}$
Electrochemical corrosion accelerated material loss in wet conditions, with corrosion products exhibiting characteristic Fe/O EDS peaks. The material removal rate $Q$ combined mechanical and chemical components:
$$Q = k_m \frac{P^{1.2}}{H_v} + k_c \cdot i_{corr} \cdot t$$
where $i_{corr}$ is corrosion current density, $k_m$ and $k_c$ are synergistic coefficients.
Optimal Material Selection Strategy
Based on 12,000 hours of field validation:
- Dry conditions: ZG60Mn (0.6C, 0.01S) with 200°C temper provides optimal wear resistance-fracture toughness balance
- Paddy fields: Medium-Mn steel offers superior corrosion-wear resistance despite lower hardness
- High-impact zones: Austempered ductile iron withstands impact but requires strict quality control
The developed selection framework extends beyond tractor casting to all soil-engaging components, potentially increasing service life by 40-60% while reducing manganese consumption by 35% versus traditional high-Mn steel solutions.