(1) First batch test
The first batch of tests examined the interaction of rare earth oxides with refractories commonly used in the steel casting industry at high temperatures.There are 6 kinds of test specimens of refractories for the test.
CeO2 and La2O3 are used as rare earth oxides with 99% purity and 325 mesh size.Six specimens, weighing 5 g each, were made with two oxides and pressed to 6.4 mm under 280 MPa pressure.Immediately after preparation, the specimens are placed in the middle of the refractory specimens and phase equilibrium tests are carried out.
The heating equipment for phase equilibrium test is a high temperature resistance furnace.After placing the refractory specimens filled with rare earth oxides in the furnace, they are heated to 1590 C for 3 h under atmospheric conditions.Then, it is cooled to room temperature at a cooling rate of 2 C/min to observe the reaction between rare earth oxides and refractories.
The test results show that there is no reaction between rare earth oxide and refractory bricks containing 90% Al2O3 and MgO-based refractories at steelmaking temperature.Refractory materials containing 70% Al2O3 and 50% Al2O3 react with rare earth oxides. The higher the content of SiO2 in the refractories, the stronger the reaction will be.At high temperatures, rare earth oxides are most likely to react with SiO2 to produce silicates with low melting points, which then react further with other oxides.
It can be seen that if rare-earth element treatment process is adopted, the lining material of pouring ladle should be made of high aluminium refractory with low SiO2 content, and the silicon content and deoxidization process should also be strictly controlled during steel smelting.
(2) Second batch test
The second batch of tests examined the interaction between rare earth oxides and refractories in the presence of molten steel [14].The diagram of specimen arrangement in phase equilibrium test is shown in the figure.
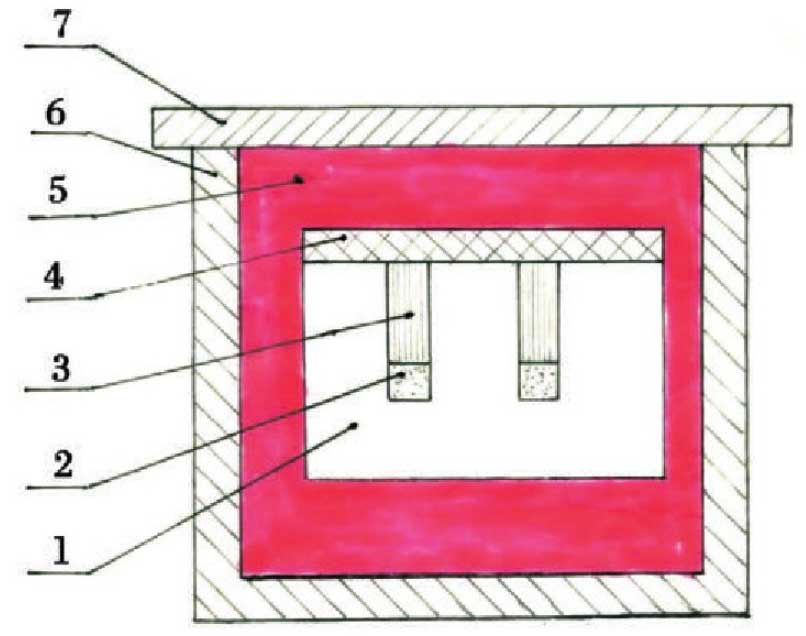
1-refractory test piece; 2-rare-earth oxide; 3-steel pin for test; 4-alumina cover plate; 5-graphite for filling; 6-crucible; 7-outer cover plate for crucible
The test refractories are three kinds of industrial high aluminium refractory bricks with the nominal content of Al2O3 of 90%, 70% and 50%, respectively. The quality condition is basically the same as that used in Test 1.The specimens of 25 mm x 25 mm and 12.5 mm thick are cut with three kinds of refractory bricks, and holes of 2.6 mm and 9.2 mm deep are drilled in the middle to place rare earth oxides and steel.
The quality of rare earth oxides (CeO2 and La2O3) used in the test is the same as that used in test 1. Samples are taken separately, weighing 0.25 g per sample, and placed in the 2.6 mm holes in the refractory bricks.
Two kinds of steel are used for the test: one is carbon steel with 0.18% carbon content, the other is Cr18-Ni8 austenitic stainless steel, the other is American 304 (hereinafter referred to as stainless steel).Cut steel pins from round steel sections, weighing 4.36 g each, and place them in the small holes of 2.6 mm in the refractory brick specimens and above the rare earth oxides.
In the test, the principle of specimen arrangement is to combine two rare earth oxides with two kinds of steel and three kinds of refractories respectively. The assembled specimen is covered with alumina cover plate, then placed in an outer crucible (alumina) with graphite powder at the bottom, and then filled with graphite powder around and above to avoid atmospheric interference.
The arranged specimens are placed in a high-temperature resistance furnace (heated by MoSi2 electrothermal element), heated to 1590 (?) at a heating rate of 5 (?) C/min, heated to room temperature for 2 h, cooled to room temperature at a rate of 5 (?) C/min. The specimens are cut along the steel pin axis with a diamond saw blade and the specimens are polished in profile.Then observe with scanning electron microscope and analyze with energy dispersive spectrometer.
The perception gained from the second batch of tests is broadly consistent with that from the first.The presence of liquid steel has no significant effect on the balance between rare earth oxide and refractories.
Carbon steel added to the specimens: use refractory bricks containing 50% Al2O3, regardless of CeOxygen dioxide or La2O3, there are obvious reaction zones at the joints between rare earth oxide and refractory bricks, and the bottom of steel pin is nodular, indicating that rare earth oxide reacts with refractory materials to form more silicates containing rare earth oxide with low melting point; with refractory bricks containing 70% Al2O3, there is only slight reaction zone at the bottom of steel pin; with refractory bricks containing 90% Al2O3, rare earth oxide reacts with refractory materialsNo reaction; there is no sign of rare earth oxide reacting with carbon steel in the area where steel pin meets refractory material with various alumina refractory bricks.
Stainless steel is added to the specimens: with refractory bricks containing 50% Al2O3, there are obvious reaction zones at the junction between rare earth oxide and refractory bricks at the bottom of steel pin. The reaction between rare earth oxide and refractory is roughly the same as that of carbon steel. At the same time, Cr in stainless steel not only enters into silicate containing rare earth, but also into similar refractory materials; with refractory bricks containing 70% Al2O3, none.Clear reaction band, but still Cr enters similar refractories; with 90% Al2O3 refractory bricks, REO does not react with the refractories, but Cr in steel enters the refractories a little more than the first two.