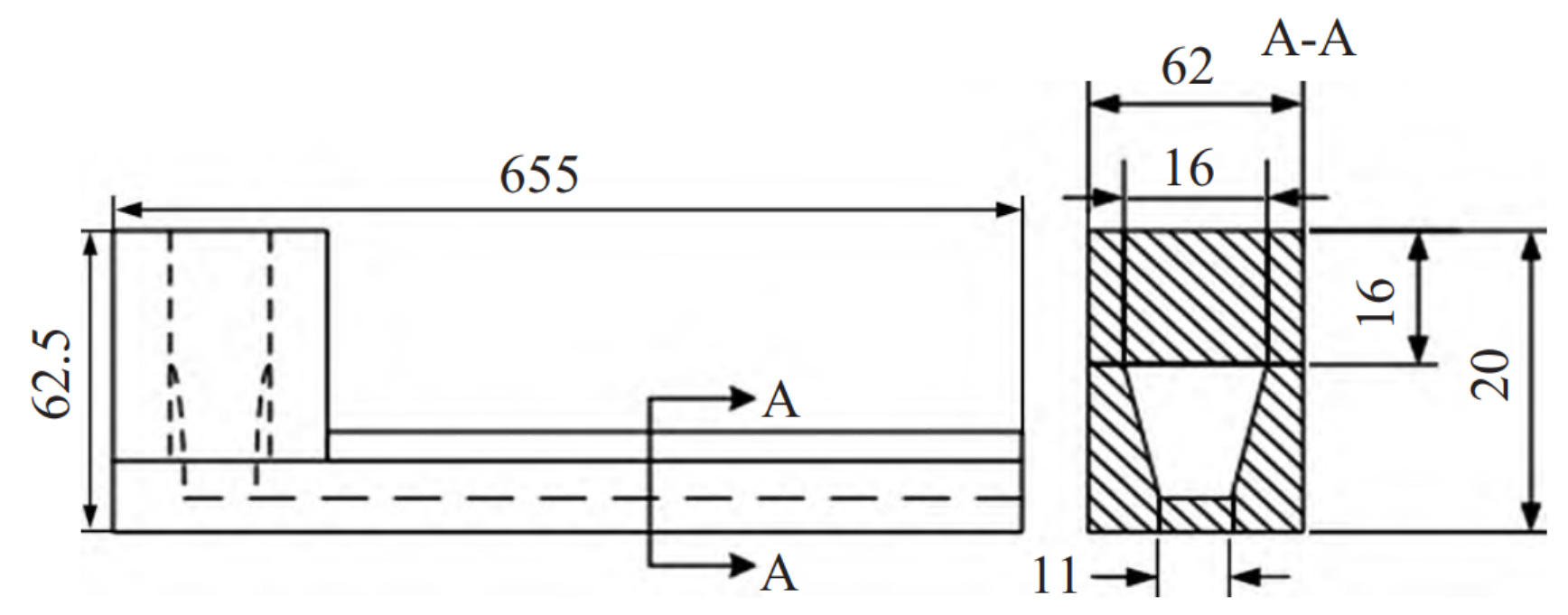
The new aluminum alloy ADC12-0.25ti containing titanium for automobile parts is taken as the research object. The chemical composition of the alloy sample is shown in Table 1. YFL-50 induction melting method is used to prepare alloy samples. The melting temperature is 720 ℃. After slag removal, it is allowed to stand for 30 min before pouring with self-made mold. The pouring temperature of each sample is shown in Table 2.
Si | Cu | Zn | Fe | Mg | Mn | Ni | Ti | Other elements | Al |
10.84 | 2.51 | 0.72 | 0.53 | 0.18 | 0.36 | 0.33 | 0.25 | 0.43 | Other |
The casting performance evaluation of the sample includes fluidity and hot cracking resistance. The test bar for fluidity test is shown in Figure 1. The test bar is poured in a metal mold. The molten aluminum alloy is poured into the metal mold, and the length of the molten aluminum flow is measured. The longer the aluminum flow, the better the fluidity of the sample; On the contrary, the smaller the aluminum flow, the worse the fluidity of the sample. The hot crack ring method is used to test the hot crack resistance of the sample, and the size of the test bar is shown in Figure 2.
Sample No | Pouring temperature / ℃ |
1# | 590 |
2# | 720 |
3# | 750 |
Measure the crack length of the sample. If the crack length is longer, the thermal crack resistance of the sample is worse; On the contrary, the smaller the crack length, the better the thermal cracking resistance of the specimen. Cut a round metallographic sample (size shall be 30 mm) in the middle of the sample × 10 mm), polished with coarse to fine metallographic abrasive paper, etched in metallographic corrosive solution (mixed solution composed of 10 ml HF, 20 ml HNO3 and 70ml H2O) for 10 s, washed and dried, and then observed the microstructure of the sample under Zeiss metallographic microscope.
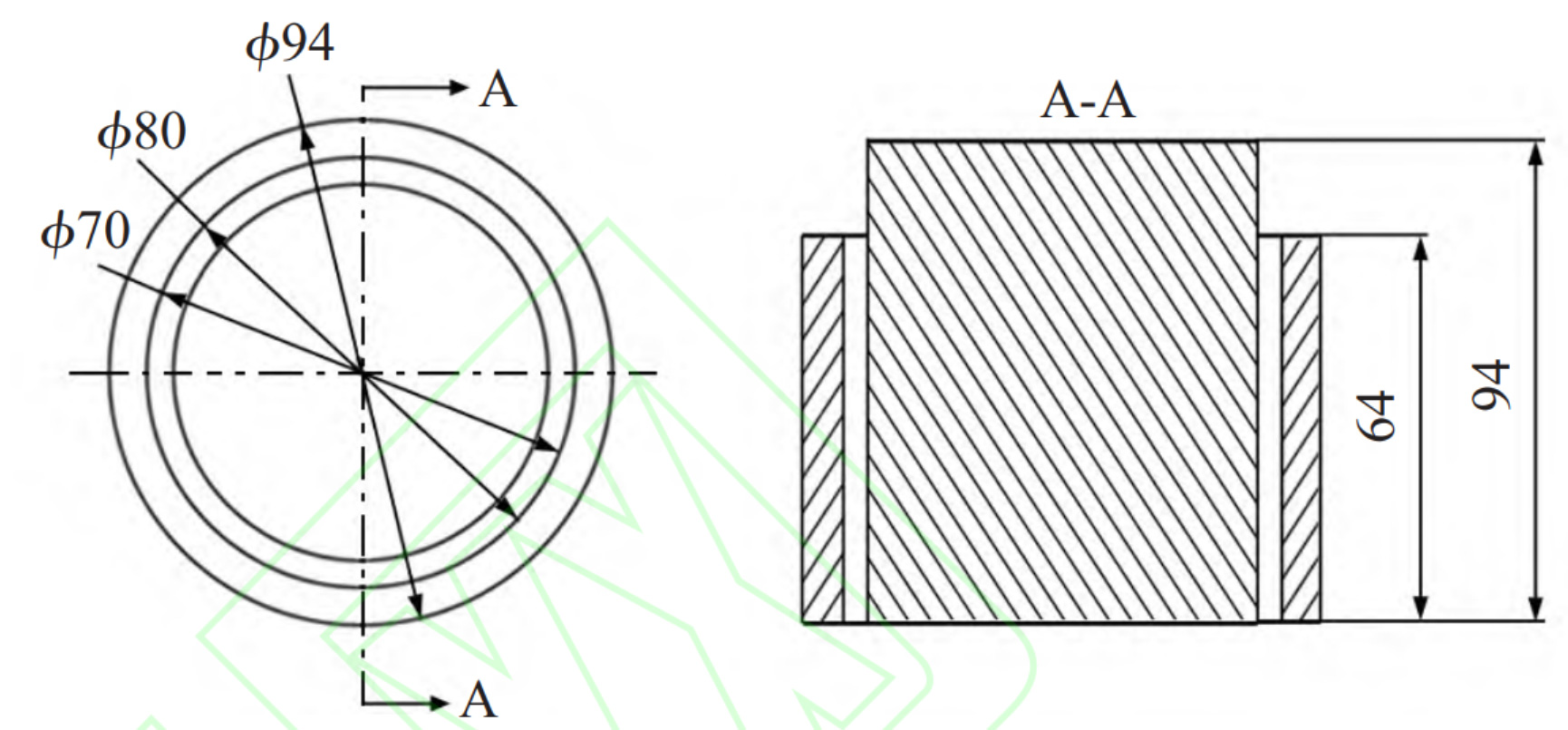