Advanced quality control methods can greatly aid in identifying and addressing casting defects. These methods utilize advanced technologies and techniques to detect defects at various stages of the casting process. Here are some advanced quality control methods commonly used in the casting industry:
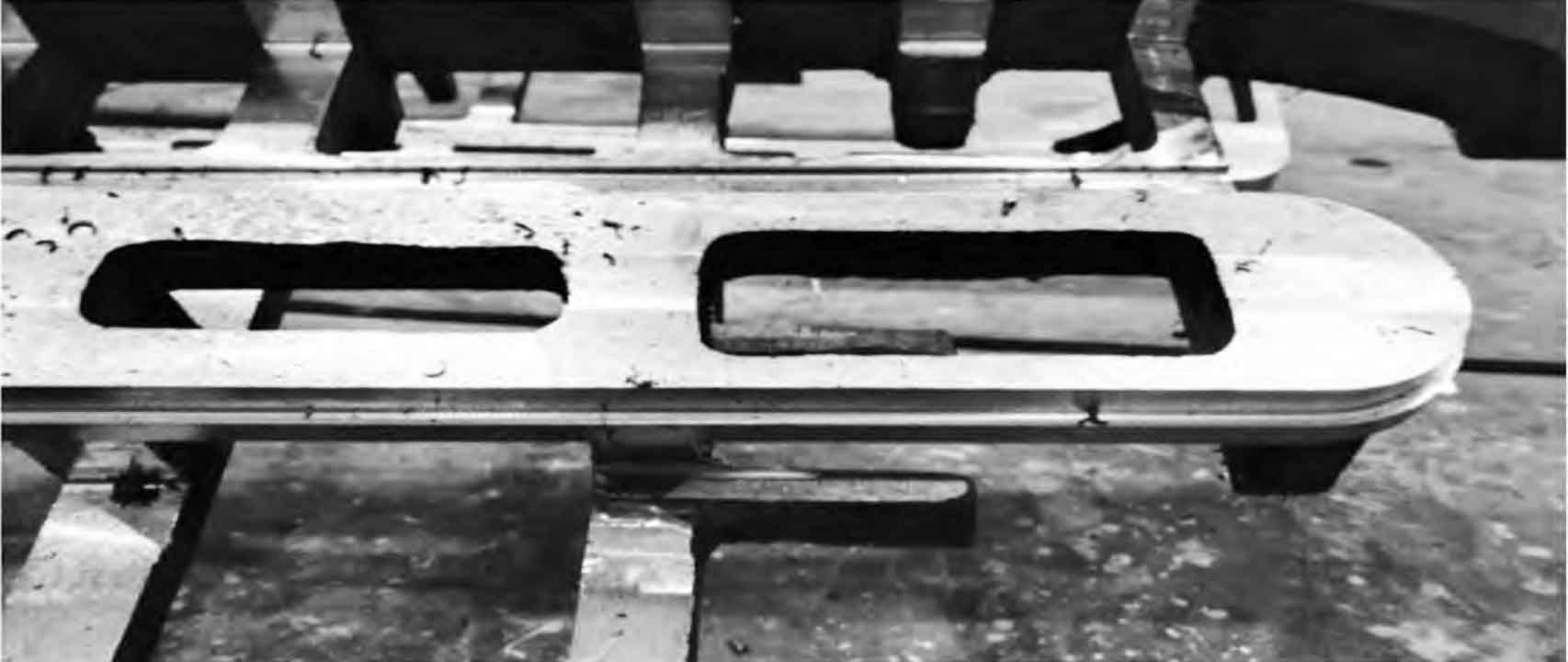
- Non-Destructive Testing (NDT):
- NDT techniques such as radiography, ultrasonic testing, magnetic particle inspection, and liquid penetrant testing are used to detect internal and surface defects without damaging the casting.
- These methods can identify defects like porosity, cracks, inclusions, and dimensional inaccuracies, allowing for timely corrective actions.
- Computerized Tomography (CT) Scanning:
- CT scanning provides a detailed 3D internal view of the casting, enabling precise defect analysis.
- It is particularly effective in identifying complex internal defects, porosity distribution, and dimensional variations that may not be easily detectable through conventional methods.
- 3D Scanning and Metrology:
- 3D scanning techniques capture the surface geometry of the casting and compare it to the CAD model for dimensional accuracy assessment.
- Optical scanners and coordinate measuring machines (CMMs) are commonly used to measure critical dimensions and compare them against design specifications.
- Real-Time Process Monitoring:
- Advanced sensor technologies and real-time monitoring systems enable continuous monitoring of process parameters during casting.
- Temperature sensors, thermal imaging cameras, and pressure sensors provide valuable insights into the casting process, allowing for immediate detection and response to deviations.
- Metallographic Analysis:
- Metallographic analysis involves examining microstructures and grain structures of the casting through metallographic sample preparation, polishing, and microscopic observation.
- This technique helps identify defects such as grain boundary segregation, improper solidification, or metallurgical abnormalities.
- Statistical Process Control (SPC):
- SPC utilizes statistical analysis to monitor and control process variables and detect deviations from control limits.
- By analyzing process data in real-time, SPC can identify trends, variations, and potential out-of-spec conditions, allowing for timely corrective actions.
- Digital Twins and Simulation:
- Digital twin technology involves creating a virtual replica of the casting process and simulating its behavior to predict potential defects and optimize process parameters.
- Simulation software helps in analyzing solidification patterns, predicting shrinkage, simulating mold filling, and optimizing gating and riser designs.
- Artificial Intelligence (AI) and Machine Learning (ML):
- AI and ML techniques can analyze vast amounts of data collected during the casting process to detect patterns, correlations, and anomalies associated with defects.
- These technologies can assist in predictive maintenance, defect classification, and decision-making for defect prevention and process optimization.
By incorporating these advanced quality control methods into the casting process, manufacturers can enhance defect detection capabilities, improve process control, and reduce the likelihood of defects. Early identification and resolution of casting defects lead to improved casting quality, reduced scrap rates, and increased overall productivity.