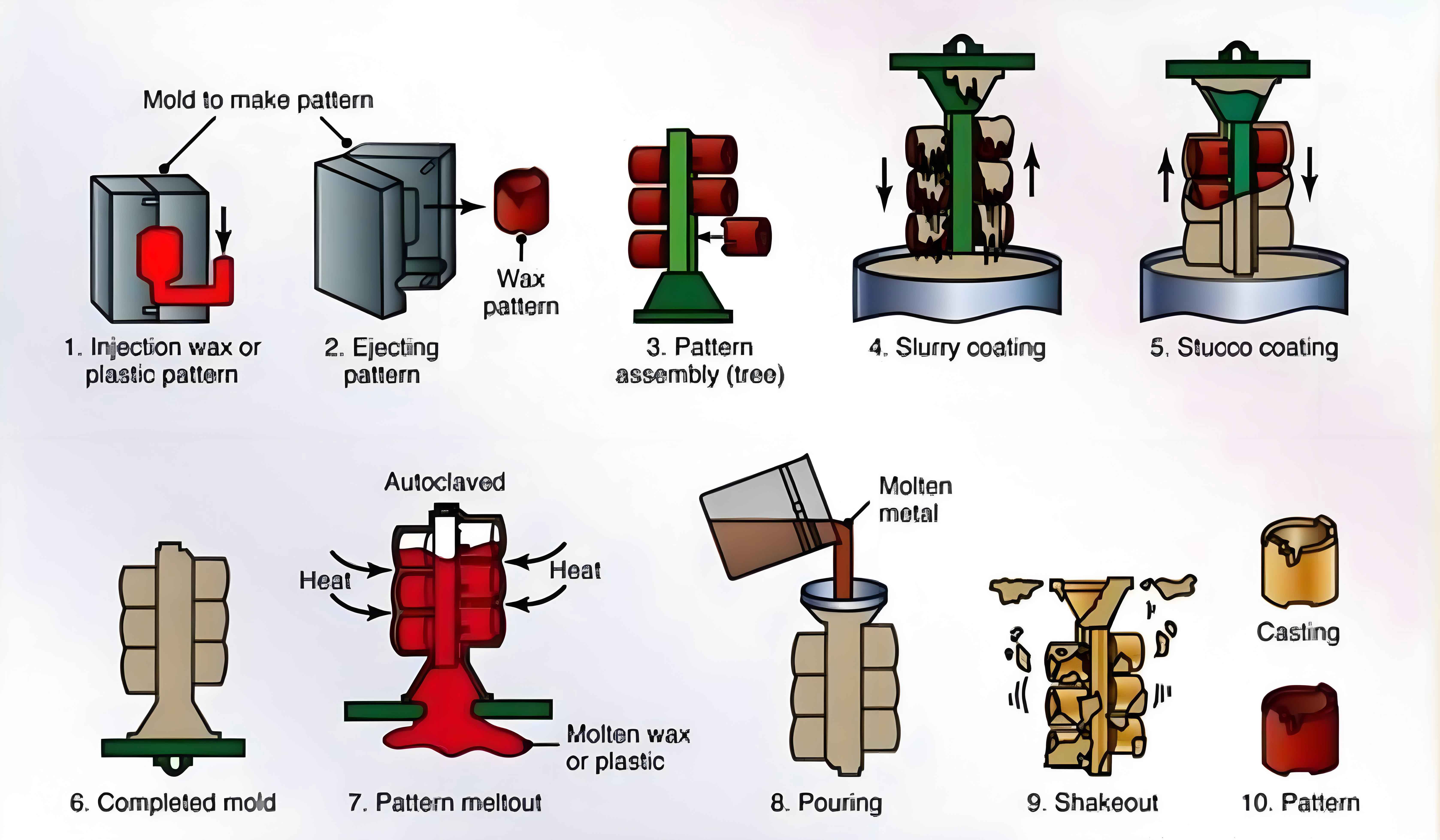
Investment casting has been a fundamental manufacturing process for creating intricate and high-precision components. As industries demand more complex geometries and higher performance standards, investment casting has evolved to incorporate advanced techniques that enhance its capabilities. This article explores the advanced techniques in investment casting that enable the production of complex geometries, highlighting their benefits, applications, and future trends.
Introduction to Investment Casting
Investment casting involves creating a wax model of the desired part, coating it with a ceramic material to form a mold, and then melting away the wax to leave a cavity. Molten metal is poured into this cavity to form the final part. This process allows for the production of components with intricate designs, fine details, and excellent surface finishes. The ability to produce highly detailed and precise parts makes investment casting ideal for applications in aerospace, automotive, medical devices, and other high-tech industries.
Challenges in Casting Complex Geometries
- Precision Mold Creation: Complex geometries require highly detailed molds that can accurately replicate every feature of the design.
- Material Flow and Solidification: Ensuring uniform material flow and solidification within intricate molds to avoid defects like porosity and misruns.
- Dimensional Accuracy: Maintaining tight tolerances while accounting for factors like mold expansion and contraction during the casting process.
- Surface Finish: Achieving a high-quality surface finish on intricate parts, especially those with fine details and thin walls.
- Quality Control: Detecting and addressing defects in complex geometries using non-destructive testing methods.
Advanced Techniques in Investment Casting
1. Computer-Aided Design (CAD) and Simulation
- CAD Software: Advanced CAD software allows for the precise design of complex geometries, enabling the creation of detailed digital models.
- Simulation Tools: Simulation tools can predict material flow, solidification patterns, and potential defects. This helps optimize the casting process before actual production, reducing the risk of errors and improving efficiency.
2. Rapid Prototyping and 3D Printing
- Wax Pattern Printing: 3D printing technologies can be used to create highly detailed wax patterns directly from CAD models. This reduces lead times and improves the accuracy of the final cast parts.
- Direct Mold Printing: Additive manufacturing can also be used to print ceramic molds directly, bypassing the need for traditional wax patterns. This technique allows for greater design freedom and the production of more complex geometries.
3. Advanced Mold Materials and Coatings
- High-Performance Ceramics: Using advanced ceramic materials for molds enhances their strength and thermal stability, allowing for the casting of high-performance alloys.
- Specialized Coatings: Applying specialized coatings to molds can improve surface finish and reduce the likelihood of defects. These coatings can also facilitate easier mold removal and reduce wear on the molds.
4. Precision Gating and Riser Systems
- Optimized Gating Design: Using simulation tools, engineers can design optimized gating and riser systems that promote uniform material flow and minimize turbulence.
- Directional Solidification: Techniques like directional solidification help control the solidification process, ensuring that critical areas of the part solidify first to avoid defects.
5. Real-Time Monitoring and Control
- In-Process Monitoring: Advanced sensors and monitoring systems can track key parameters during the casting process, such as temperature and material flow. This real-time data allows for immediate adjustments to prevent defects.
- Automated Control Systems: Automated control systems can adjust process parameters in real-time based on monitoring data, ensuring consistent quality and reducing variability.
Applications of Advanced Investment Casting Techniques
Aerospace
Investment casting is essential for producing turbine blades, structural components, and engine parts. Advanced techniques allow for the creation of lightweight, high-strength parts with complex cooling channels and aerodynamic features.
Medical Devices
In the medical field, investment casting is used to produce surgical instruments, orthopedic implants, and dental devices. The precision and biocompatibility of cast parts are critical for patient safety and device performance.
Automotive
The automotive industry relies on investment casting for engine components, transmission parts, and suspension systems. Advanced casting techniques enable the production of lightweight and durable parts that improve fuel efficiency and performance.
Energy
Investment casting is used to manufacture components for power generation, including gas and steam turbines. The ability to cast high-performance alloys with intricate cooling passages is essential for the efficiency and reliability of energy systems.
Industrial Machinery
Industrial machinery components, such as pump housings, valve bodies, and gear components, benefit from the precision and complexity achievable through advanced investment casting techniques.
Comparative Analysis of Advanced Techniques
Technique | Benefits | Applications |
---|---|---|
CAD and Simulation | Precise design, error reduction | All industries |
3D Printing | Rapid prototyping, complex geometries | Aerospace, Medical, Automotive |
Advanced Mold Materials | Enhanced strength, thermal stability | Aerospace, Energy |
Precision Gating Systems | Uniform material flow, defect reduction | Aerospace, Automotive |
Real-Time Monitoring | Quality control, process consistency | All industries |
Future Trends in Investment Casting
Integration with Additive Manufacturing
The integration of additive manufacturing with investment casting will continue to advance, enabling the production of even more complex and customized parts. This synergy will reduce lead times, lower costs, and expand design possibilities.
Digital Twin Technology
Digital twin technology, which creates a virtual replica of the casting process, will enhance the ability to predict and optimize casting outcomes. This will further reduce defects and improve overall process efficiency.
Sustainable Practices
The adoption of sustainable materials and energy-efficient processes will become increasingly important. Investment casting will evolve to incorporate eco-friendly practices, reducing its environmental impact.
Advanced Alloys
Ongoing research into new high-performance alloys will expand the capabilities of investment casting. These advanced materials will offer superior mechanical properties, corrosion resistance, and temperature stability.
Conclusion
Investment casting plays a vital role in modern manufacturing, particularly for producing complex geometries with high precision and excellent surface finishes. The incorporation of advanced techniques such as CAD, 3D printing, advanced mold materials, precision gating systems, and real-time monitoring has significantly enhanced the capabilities of investment casting. These advancements have expanded the applications of investment casting across various industries, including aerospace, medical, automotive, energy, and industrial machinery.
As technology continues to evolve, the future of investment casting looks promising. The integration with additive manufacturing, the adoption of digital twin technology, the focus on sustainable practices, and the development of advanced alloys will drive further innovation in this field. Investment casting will remain a critical process in modern manufacturing, enabling the production of high-quality, high-performance components that meet the demands of today’s industries.