Advancements in ball valve technology have focused on improving performance, reliability, and efficiency in various applications. Here are some notable advancements:
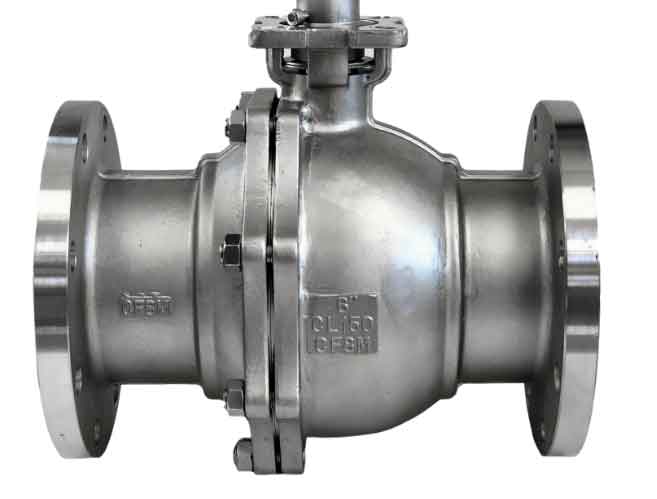
- Advanced Materials: Manufacturers have developed new materials and coatings to enhance the durability, corrosion resistance, and performance of ball valves. For example, advanced alloys and composite materials are being used to increase resistance to corrosive fluids, high temperatures, and abrasive environments.
- Sealing Technology: Advancements in sealing technology have resulted in improved sealing materials, such as enhanced elastomers and high-performance polymers. These materials provide better sealing performance, extended service life, and increased resistance to wear and tear.
- Anti-Cavitation and Noise Reduction: Ball valve designs now incorporate features to mitigate cavitation and reduce noise. Cavitation is the formation and collapse of vapor bubbles, which can cause damage and noise in high-velocity applications. Advanced designs, such as modified ball shapes and trim configurations, help minimize cavitation effects and associated noise.
- Low-Emission Designs: Environmental concerns and regulatory requirements have led to the development of low-emission ball valves. These valves feature improved stem sealing designs and packing materials, reducing the emission of fugitive gases and meeting stringent environmental standards.
- Smart Valve Technology: Integration of smart technologies has enabled the development of intelligent ball valves. These valves are equipped with sensors, actuators, and communication capabilities to provide real-time monitoring, remote control, and data feedback. Smart valves offer enhanced system automation, diagnostics, and predictive maintenance, optimizing process efficiency and reducing downtime.
- Fire-Safe Designs: Fire-safe ball valves incorporate features that allow them to maintain their integrity and functionality in the event of a fire. These designs include fire-safe seals, metal-to-metal sealing, and thermal insulation to prevent leakage and maintain shut-off capabilities during fire emergencies.
- High-Pressure and High-Temperature Applications: Advancements in materials and engineering have enabled the development of ball valves capable of handling extreme pressure and temperature conditions. These valves are used in demanding industries such as oil and gas, petrochemicals, and power generation.
- Improved Flow Characteristics: Manufacturers have focused on optimizing flow characteristics to reduce pressure drop and improve energy efficiency. Enhanced ball designs, such as V-shaped or contoured balls, promote better flow control and minimize turbulence, resulting in improved system performance.
- Automated Valve Systems: The integration of ball valves into automated systems has become more seamless, with advancements in actuator technology. Electric, pneumatic, and hydraulic actuators offer precise control, rapid response, and remote operation, enabling sophisticated automation and process optimization.
- Enhanced Safety Features: Advancements in safety features include the incorporation of emergency shutdown (ESD) systems, fail-safe mechanisms, and position monitoring. These features improve safety, reduce the risk of accidents, and enhance overall system reliability.
These advancements in ball valve technology contribute to increased efficiency, reliability, and safety across a wide range of industries. As research and development continue, we can expect further innovations to meet evolving industry demands and optimize fluid control in various applications.