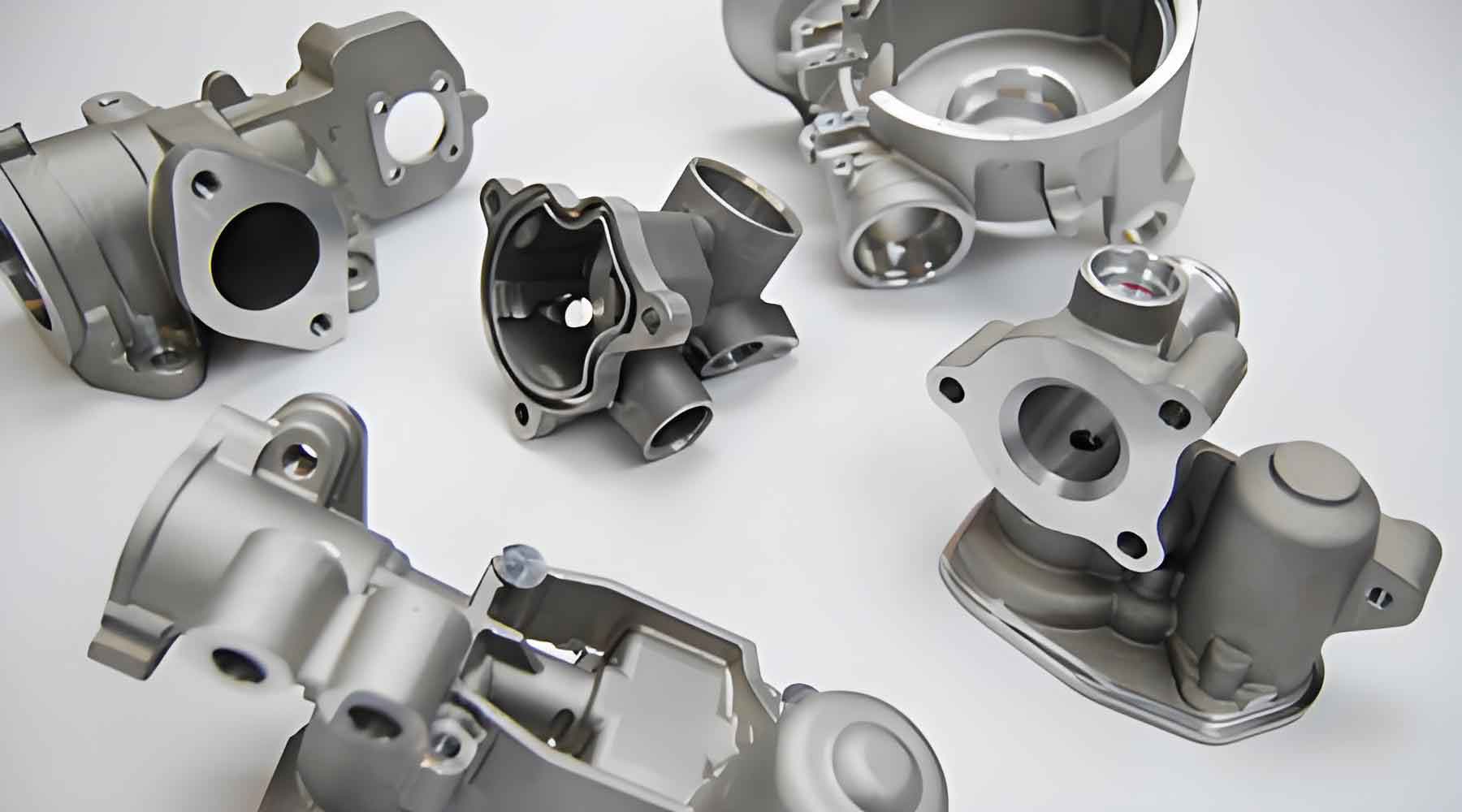
Precision casting is crucial manufacturing process in the aerospace industry. It allows for the creation of complex, high-performance components that meet stringent quality standards. The aerospace sector demands materials and processes that can withstand extreme conditions, such as high temperatures and mechanical stress. This article explores recent advancements in precision casting techniques that are enhancing the capabilities of aerospace applications, including material innovations, process improvements, and quality control measures.
Introduction to Precision Casting
Precision casting is a process where a wax pattern is coated with a refractory ceramic material to form a mold. After the wax is melted and drained away, molten metal is poured into the mold to create a detailed and accurate component. This process is highly valued in aerospace for its ability to produce parts with intricate geometries and excellent surface finishes.
Importance of Precision Casting in Aerospace
The aerospace industry relies on precision casting for several reasons:
- High Performance: Components must perform reliably under extreme conditions.
- Weight Reduction: Lightweight materials and designs are crucial for fuel efficiency.
- Complex Geometries: Ability to cast intricate shapes reduces the need for assembly and machining.
- Material Integrity: High-quality materials are essential for safety and performance.
Recent Advancements in Precision Casting
- Advanced Materials
- Enhanced Process Technologies
- Improved Quality Control
- Sustainability Initiatives
Advanced Materials
The development of new materials has significantly improved the performance of precision-cast components in aerospace applications.
- Superalloys
- Nickel-Based Superalloys: These materials offer exceptional strength and resistance to high temperatures, making them ideal for turbine blades and other engine components.
- Cobalt-Based Superalloys: Known for their high wear resistance and ability to withstand corrosive environments.
- Titanium Alloys
- Ti-6Al-4V: A widely used titanium alloy that combines high strength with lightweight properties, suitable for structural components.
- Titanium Aluminides: Offer excellent high-temperature performance and are used in advanced aerospace engines.
- Ceramic Matrix Composites (CMCs)
- SiC/SiC Composites: Provide high-temperature stability and are used in turbine components to reduce weight and improve fuel efficiency.
Material | Key Properties | Applications |
---|---|---|
Nickel-Based Superalloys | High strength, high-temperature resistance | Turbine blades, engine components |
Cobalt-Based Superalloys | Wear resistance, corrosion resistance | High-stress components |
Ti-6Al-4V | High strength, lightweight | Structural components |
Titanium Aluminides | High-temperature performance | Advanced aerospace engines |
SiC/SiC Composites | High-temperature stability, lightweight | Turbine components |
Enhanced Process Technologies
Recent technological advancements have significantly improved the precision and efficiency of the casting process.
- 3D Printing and Rapid Prototyping
- Direct Metal Laser Sintering (DMLS): Allows for the creation of complex metal parts directly from digital designs, reducing lead times and prototyping costs.
- Investment Casting Patterns: 3D-printed patterns enable faster and more accurate mold creation.
- Vacuum Casting
- Reduced Contamination: Vacuum environments minimize contamination and improve material integrity.
- Enhanced Surface Finish: Produces components with superior surface finishes, reducing the need for post-processing.
- Automated Shell Building
- Robotic Dipping and Spraying: Improves consistency and precision in the creation of ceramic shells, leading to better dimensional accuracy and reduced defects.
Technology | Benefits | Applications |
---|---|---|
Direct Metal Laser Sintering (DMLS) | Fast prototyping, complex geometries | Prototyping, small production runs |
Vacuum Casting | Reduced contamination, superior surface finish | High-integrity components |
Automated Shell Building | Consistency, precision | Large-scale production |
Improved Quality Control
Advancements in quality control are crucial for ensuring the reliability and performance of precision-cast aerospace components.
- Non-Destructive Testing (NDT)
- X-Ray Computed Tomography (CT): Provides detailed 3D images of internal structures, allowing for precise defect detection.
- Ultrasonic Testing: Detects internal flaws and measures material thickness with high accuracy.
- Real-Time Process Monitoring
- Thermal Imaging: Monitors temperature distributions during casting to ensure uniformity and identify potential issues.
- Digital Twins: Virtual replicas of the casting process that allow for real-time monitoring and optimization.
- Automated Inspection Systems
- Machine Vision: Uses cameras and AI to detect surface defects and dimensional deviations.
- Robotic Inspection: Enhances the speed and accuracy of quality control checks.
Technique | Key Features | Applications |
---|---|---|
X-Ray Computed Tomography (CT) | Detailed internal imaging, precise defect detection | Complex internal structures |
Ultrasonic Testing | High accuracy, internal flaw detection | Material integrity assessment |
Thermal Imaging | Real-time temperature monitoring | Process optimization |
Digital Twins | Real-time monitoring, process optimization | Quality control, process improvement |
Machine Vision | Surface defect detection, dimensional accuracy | Automated quality control |
Robotic Inspection | Speed, accuracy | High-volume production |
Sustainability Initiatives
Sustainability is becoming increasingly important in precision casting for aerospace, with a focus on reducing environmental impact.
- Recyclable Materials
- Recycling Superalloys: Reducing waste by recycling and reusing superalloy materials.
- Biodegradable Patterns: Developing wax patterns that are biodegradable, reducing environmental impact.
- Energy Efficiency
- Advanced Melting Techniques: Implementing more energy-efficient melting techniques to reduce energy consumption.
- Heat Recovery Systems: Utilizing waste heat recovery systems to improve overall process efficiency.
- Waste Reduction
- Optimized Mold Design: Reducing material usage through optimized mold design and manufacturing processes.
- Lean Manufacturing Principles: Implementing lean manufacturing principles to minimize waste and enhance efficiency.
Initiative | Key Benefits | Applications |
---|---|---|
Recycling Superalloys | Waste reduction, resource conservation | High-performance components |
Biodegradable Patterns | Environmental impact reduction | Pattern making |
Advanced Melting Techniques | Energy efficiency | Melting processes |
Heat Recovery Systems | Improved efficiency, reduced energy consumption | Foundries |
Optimized Mold Design | Material usage reduction | Mold making |
Lean Manufacturing Principles | Waste minimization, efficiency improvement | Production processes |
Case Studies
Case Study 1: Jet Engine Turbine Blades
A leading aerospace manufacturer implemented advanced precision casting techniques to produce turbine blades. By using nickel-based superalloys and vacuum casting, the company achieved significant improvements in component performance and lifespan.
Metric | Before Advancements | After Advancements |
---|---|---|
Defect Rate | 5% | 1% |
Component Lifespan | 10,000 hours | 15,000 hours |
Production Efficiency | 80% | 90% |
Case Study 2: Structural Aircraft Components
An aerospace firm utilized 3D printing and automated shell building to enhance the production of structural components. This approach resulted in reduced lead times and improved dimensional accuracy.
Metric | Before Advancements | After Advancements |
---|---|---|
Lead Time | 12 weeks | 8 weeks |
Dimensional Accuracy | ±0.5 mm | ±0.2 mm |
Production Efficiency | 75% | 85% |
Future Directions in Precision Casting
The future of precision casting in aerospace is poised for further advancements:
- Smart Manufacturing
- IoT Integration: Using IoT devices for real-time data collection and process optimization.
- AI and Machine Learning: Applying AI and machine learning to predict and prevent defects.
- Advanced Materials Development
- Next-Generation Superalloys: Developing new superalloys with improved properties for even higher performance.
- Nanomaterials: Utilizing nanomaterials to enhance the mechanical properties and performance of cast components.
- Sustainable Practices
- Green Foundries: Implementing sustainable practices in foundries to reduce environmental impact.
- Circular Economy: Promoting a circular economy by recycling materials and reducing waste.
Conclusion
Advancements in precision casting techniques are significantly enhancing the capabilities and performance of aerospace components. Through the development of advanced materials, improved process technologies, enhanced quality control, and sustainability initiatives, the aerospace industry can achieve higher levels of efficiency, reliability, and environmental responsibility. As technology continues to evolve, the future of precision casting in aerospace looks promising, with ongoing innovations poised to meet the growing demands of the industry.