Spheroidal Graphite Iron, also known as ductile iron or nodular cast iron, is a type of cast iron that offers superior strength, toughness, and ductility compared to traditional gray cast iron. Over the years, advancements in Spheroidal Graphite Iron technology have pushed the limits of its strength and design flexibility, making it a highly versatile material in various industries. Let’s explore some of these advancements:
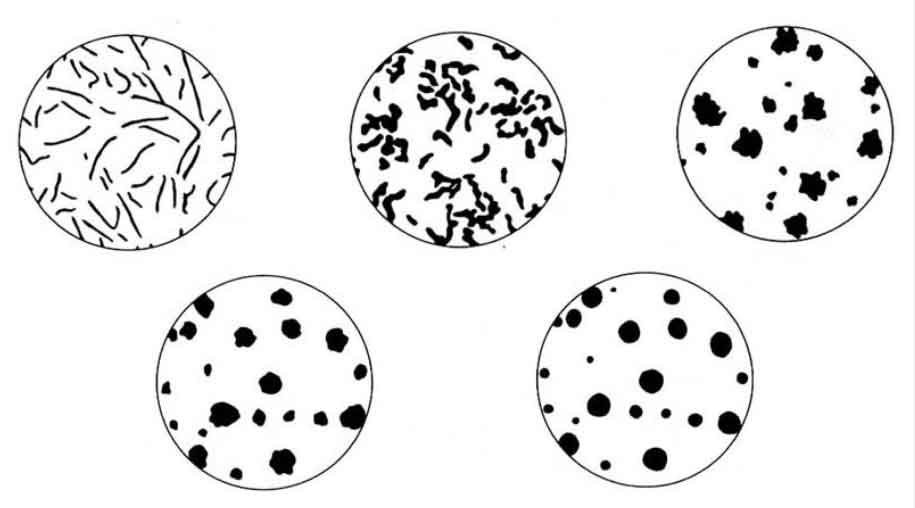
- Alloying and Heat Treatment: Advances in alloying techniques and heat treatment processes have significantly improved the mechanical properties of Spheroidal Graphite Iron. By carefully selecting and controlling the composition of the iron, manufacturers can achieve higher levels of strength and toughness. Heat treatment processes like annealing, quenching, and tempering are employed to refine the microstructure and enhance the material’s properties.
- Graphite Nodularity Control: The presence of spheroidal graphite nodules, which form during the casting process, gives Spheroidal Graphite Iron its unique properties. Advancements in nodularity control techniques have allowed for the production of castings with a high percentage of spheroidal graphite nodules, resulting in improved mechanical properties. Control over the nodularity also enables designers to tailor the material’s properties to specific applications.
- Compacted Graphite Iron (CGI): A variation of Spheroidal Graphite Iron, known as Compacted Graphite Iron (CGI), has gained prominence due to its superior strength-to-weight ratio and thermal conductivity. Graphite Iron has a microstructure that lies between the flake-like graphite of gray iron and the spheroidal graphite of Spheroidal Graphite Iron, resulting in a unique combination of properties. This advancement in SGI technology has opened up new possibilities in weight-sensitive applications such as automotive components.
- Thin-Wall Casting: Spheroidal Graphite Iron’s exceptional castability allows for the production of thin-walled components without sacrificing strength. Advancements in casting techniques, such as the use of optimized gating and risering systems, have minimized the formation of defects and improved the integrity of thin sections. This has expanded the design flexibility of Spheroidal Graphite Iron, enabling the production of intricate and lightweight castings.
- Finite Element Analysis (FEA) and Simulation: Computational tools like FEA and simulation software have revolutionized the design and optimization of spheroidal Graphite Iron components. Engineers can now simulate and analyze the behavior of castings under various loads, temperatures, and environments. This enables the identification of potential design flaws and optimization of the component’s geometry, leading to enhanced strength, durability, and performance.
- Additive Manufacturing: The advent of additive manufacturing, or 3D printing, has also impacted spheroidal Graphite Iron technology. While traditional foundry processes are still prevalent, the use of 3D printing techniques for spheroidal Graphite Iron offers unique opportunities for complex geometries and rapid prototyping. Additive manufacturing allows for the creation of intricate internal structures and the incorporation of functional features within the casting, expanding the design freedom and possibilities for SGI components.
These advancements in spheroidal Graphite Iron technology have extended its applications across various industries, including automotive, aerospace, energy, and machinery. Spheroidal Graphite Iron’s high strength, good machinability, and design flexibility make it a preferred choice for components subjected to heavy loads, shock, and thermal cycling. As research and development in materials science continue, we can expect further innovations in spheroidal Graphite Iron technology, pushing the limits of strength and design flexibility even further.