As shown in the figure is the schematic diagram of the horizontal continuous casting cast iron profile production line. After treatment, the molten iron flows into the holding furnace, and the self weight molten iron enters the water cooling mold. The water flow in the mold can be controlled artificially to adjust the temperature difference between the hot metal entering and leaving the mold. Finally, the cold solidification of molten iron will be carried out within a certain temperature gradient, and the solidification formation is consistent with the mold aperture Profiles of the same shape and thickness.
After that, the molten iron in the holding furnace continuously enters into the mold for replenishment, and then cools and solidifies. In this way, the continuous production of cast iron profiles can be achieved through repeated cycles. Finally, the end of the production line is grooved and pressed into commercial profiles. The different shape and process of mould lead to different section shape and different material of cast iron profile.
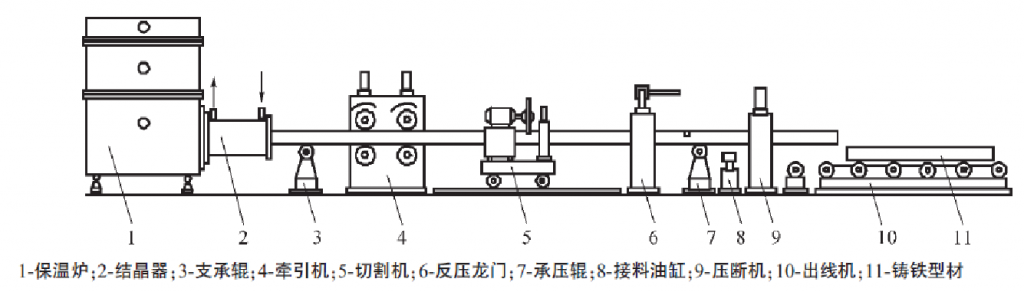
Cast iron profile is called “dense bars” in foreign countries, because this process has many advantages that traditional casting lacks, such as:
(1) The defects produced by traditional casting method can be avoided
The horizontal continuous casting process combined with the closed mold makes the magazine float upward. This is because there are few impurities in the molten iron, and it is difficult to appear some common casting defects after flowing into the mold.
(2) Fine grain size, high density and good mechanical properties
In the process of profile production, the molten iron cooling rate is high and the nucleation rate is strong in the mold. Therefore, the profile produced by this process has small structure density, small grain size and good comprehensive mechanical properties. Therefore, the name “compact rod” is obtained.
(3) The profile has smooth surface, accurate size and small machining allowance
When the profile is finally formed in the graphite sleeve, the graphite is difficult to infiltrate the molten iron and has high fire resistance. The inner wall of graphite sleeve is manufactured by machining, so the inner wall is smooth and has high precision. Therefore, the formed profile is also the sample with accurate size and smooth surface.
(4) The machining performance is good
Compared with sand mold casting, cast iron profile has higher strength, lower hardness and better processability.